Tabla de contenido
Introduction to Non-Woven Bag Production
In an era where sustainability and environmental protection are top priorities, Non-Woven bags are becoming the leading choice to replace traditional plastic bags. Non-Woven bags are not only environmentally friendly but also durable and reusable multiple times. However, with the increasing demand for Non-Woven bag production, manufacturers face significant challenges in reducing production costs while maintaining product quality.
In this article, we will share two success stories from Kenia y Burundi, where Mega helped manufacturers reduce up to 20% of Non-Woven bag production costs by using relleno masterbatch blanco. This is an excellent solution that allows manufacturers to not only reduce costs but also remain competitive in an increasingly competitive market.
Non-Woven Bags and the Sustainable Production Trend
Non-Woven bags are increasingly popular because they are environmentally friendly, durable, and reusable. Unlike traditional plastic bags, Non-Woven bags are not only biodegradable but also create a positive image for brands, helping them score points with consumers in terms of environmental protection.
Benefits of Non-Woven Bags
- Environmentally Friendly: Non-polluting, biodegradable, and recyclable.
- Durable and Long-Lasting: Sturdy, reusable, reducing waste production.
- Aesthetic and Diverse: Can be printed with logos and brand information in a variety of colors and designs.
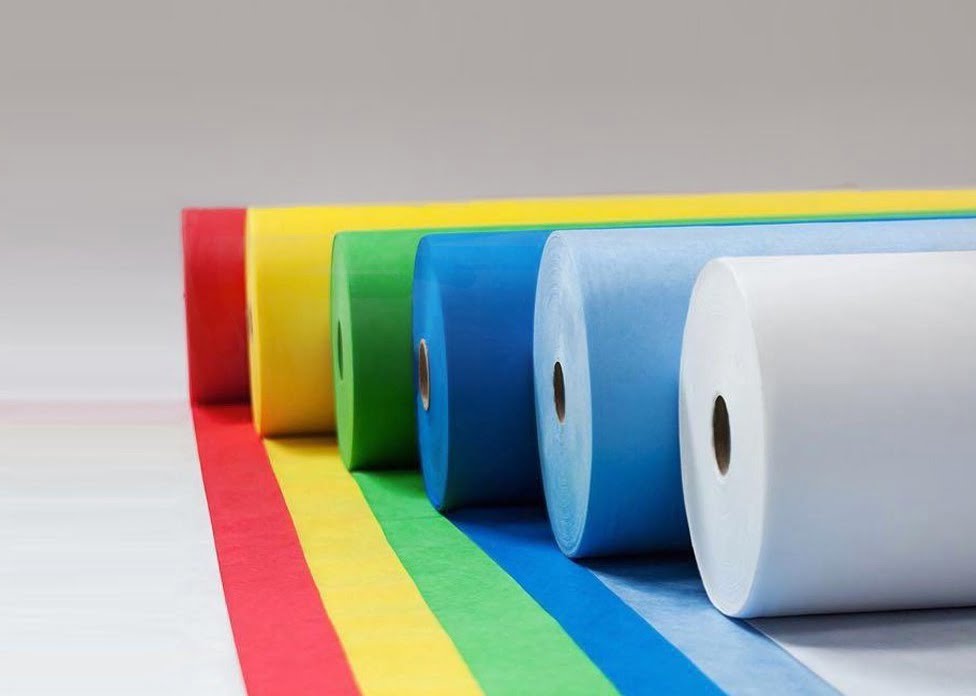
However, producing Non-Woven bags often costs more than traditional plastic bags, especially when using virgin resin. This is why many manufacturers are seeking solutions to optimize Non-Woven bag production costs without compromising product quality.
Case Study 1: Reducing 20% of Non-Woven Bag Production Costs in Kenya
Context: The Kenyan Government Bans Plastic Bags
In 2018, the Kenyan government banned the use of plastic bags, forcing many manufacturers to switch to producing Non-Woven bags. These bags are not only environmentally friendly but also meet aesthetic needs and can be reused multiple times. However, using 100% virgin resin to produce Non-Woven bags increased production costs, making it difficult to compete in the market.
Challenge: High Production Costs
By using 100% virgin resin, manufacturers in Kenya faced high production costs, making their products less competitive in terms of price.
Mega’s Solution: Using Filler Masterbatch N202
Mega advised manufacturers in Kenya to replace 30% of virgin resin with Filler Masterbatch N202. The Filler Masterbatch costs only one-third of the price of virgin resin, significantly reducing production costs while maintaining the quality of Non-Woven bags.
Results: 20% Reduction in Total Production Costs
By using Filler Masterbatch N202, the manufacturer in Kenya was able to reduce 20% of production costs, while maintaining the durability, aesthetics, and reusability of the Non-Woven bags.
Case Study 2: Increasing Competitiveness in Burundi with Filler Masterbatch
Context: Fierce Competition in the Burundi Market
A customer in Burundi had been using 30% locally sourced Filler Masterbatch in Non-Woven bag production. However, production costs remained too high, making it difficult to compete on price with other market players.
Challenge: Finding a Solution to Reduce Production Costs
Although the customer had already been using filler, they hadn’t seen significant cost-saving results. They needed a new filler solution to further reduce costs while maintaining the quality of Non-Woven bags.
Mega’s Solution: Using Filler Masterbatch N202 with a 50% Filler Ratio
Mega provided Filler Masterbatch N202, allowing the manufacturer to use a 50% filler ratio, greatly reducing the amount of virgin resin required in the production of Non-Woven bags. Despite the high filler ratio, the product’s quality was maintained thanks to the superior quality of N202.
Results: Optimized 15% of Production Costs
By using Filler Masterbatch N202, the customer in Burundi was able to reduce 15% of production costs for Non-Woven bags, thus enhancing their competitiveness in the international market.
Why Use Filler Masterbatch in Non-Woven Bag Production?
1. Reduce Production Costs
Using Filler Masterbatch such as N202 can help Non-Woven bag manufacturers reduce up to 20% of production costs while maintaining product quality.
2. Maintain Product Quality
Filler Masterbatch N202 is designed to replace virgin resin without affecting the durability, aesthetics, and reusability of Non-Woven bags.
3. Increase Competitiveness
With lower production costs, Non-Woven bag manufacturers can better compete on price, thus increasing their market reach.
4. Megaplast make diffirent
Gracias a la alianza estratégica con un carbonato de calcio Fábrica Global Minerals, Megaplast is able to offer Filler Masterbatch N202 at lower production costs, providing a competitive edge for Non-Woven bag manufacturers. Calcium carbonate is the main raw material used in filler production, ensuring both quality and cost stability. This enables customers not only to reduce production costs by 20% but also to enhance their competitiveness in the global marke
Conclusion: The Optimal Solution for Non-Woven Bag Production
The use of Filler Masterbatch N202 has helped manufacturers in Kenia y Burundi significantly reduce Non-Woven bag production costs while maintaining product quality. This is an effective solution for manufacturers looking to improve their competitiveness in a sustainable market.
If you’re looking for ways to reduce Non-Woven bag production costs while maintaining product quality, Contáctenos today for detailed consultation on Filler Masterbatch solutions tailored to your business!
Download the Detailed Case Study
Want to know more about how MegaPlast helped manufacturers in Kenya and Burundi optimize their production costs? Download the detailed case study here to get more information and the right solutions for your needs.
Grupo Nhat Huy es un fabricante y exportador pionero de productos plásticos en Vietnam, establecido en 2004. Ofrecemos una gama de productos de alta calidad que incluyen polvo mineral, masterbatch de relleno y compuestos de PVC, para atender a los mercados globales. Comprometido con la innovación y la mejora, Nhat Huy Group se dedica a proporcionar soluciones plásticas sostenibles, eficientes y respetuosas con el medio ambiente, contribuyendo al desarrollo comunitario y social. Nuestro equipo de expertos está siempre listo para ofrecer productos y servicios que cumplan con los estándares internacionales, garantizando la máxima satisfacción de nuestros clientes.