In plastic production, the imperative to innovate while curbing production costs drives research and development (R&D) efforts. A notable breakthrough in this endeavor is the strategic use of filler masterbatch, which promises significant raw material cost savings and enhances the properties of plastic products. This blog post explores the scientific foundations and research contributions that underline the effectiveness of filler masterbatch in the plastics industry, focusing on its role in reducing raw material costs.
Scientific Basis of Filler Masterbatch

Filler masterbatch is a compound material designed to be mixed with polymer resins, consisting of a carrier polymer and added filler materials such as calcium carbonate (CaCO3), talc, or barium sulfate. The choice of filler is crucial; it is selected based on its ability to improve product properties like rigidity, thermal stability, and impact resistance while contributing to material cost reductions. From a scientific standpoint, the interaction between filler particles and the polymer matrix is of paramount interest, as this relationship directly influences the composite’s mechanical and thermal properties.
Cost-Effective Production Through Material Science
The economic appeal of filler masterbatch stems from its capacity to reduce the volume of more expensive polymer required, effectively lowering overall material costs. Scientific research has quantified these benefits, revealing that appropriate filler incorporation can lead to 20-30% cost reductions without compromising, and sometimes even enhancing, product quality. This is achieved through a meticulous balance between filler concentration and dispersion within the polymer matrix, a topic of ongoing material science research.
Empirical Evidence and Innovations
Recent studies underscore the dual benefits of filler masterbatch, highlighting cost savings and performance improvements. For instance, the inclusion of nano-sized fillers has been shown to significantly enhance plastic films’ barrier properties and strength at much lower filler concentrations, owing to the increased surface area and improved filler-polymer interactions. Such advancements underscore the critical role of R&D in optimizing filler masterbatch compositions for specific applications.
Enhancing Sustainability
Beyond cost implications, the use of filler masterbatch aligns with sustainability goals. Reducing polymer usage decreases the environmental impact of plastic production. Moreover, exploring bio-based fillers introduces a new dimension of eco-friendliness to the industry. Scientific investigations into these alternatives promise not only to reduce the carbon footprint of products but also to open up new avenues for biodegradability and recycling.
Customization Through Chemistry
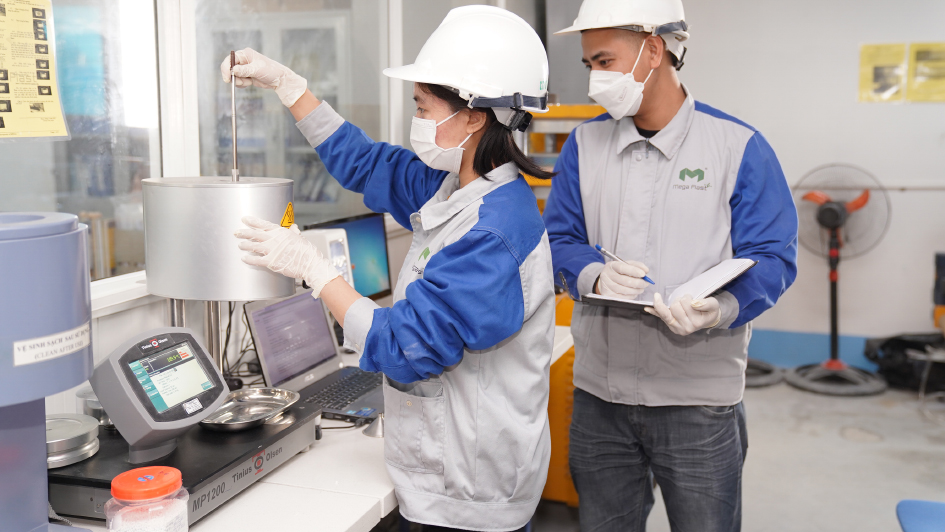
The adaptability of filler masterbatch to specific application needs is a testament to its chemistry. R&D teams are at the forefront of customizing filler types and concentrations to modify plastics’ physical, chemical, and mechanical properties, tailoring them to diverse industry requirements. This level of customization is pivotal for applications ranging from consumer packaging to automotive components, where specific attributes like UV resistance or weight reduction are crucial.
Case Studies: A Research Perspective
Case studies from the packaging and automotive sectors highlight the application of scientific principles and reveal the practical benefits of filler masterbatch. In packaging, transitioning to a specific high-performance filler masterbatch led to a 25% material cost reduction while improving the product’s mechanical strength and moisture resistance. On the other hand, automotive parts manufacturers have leveraged customized filler masterbatches to achieve lighter components with improved fuel efficiency without compromising durability.
Future Research Trajectories
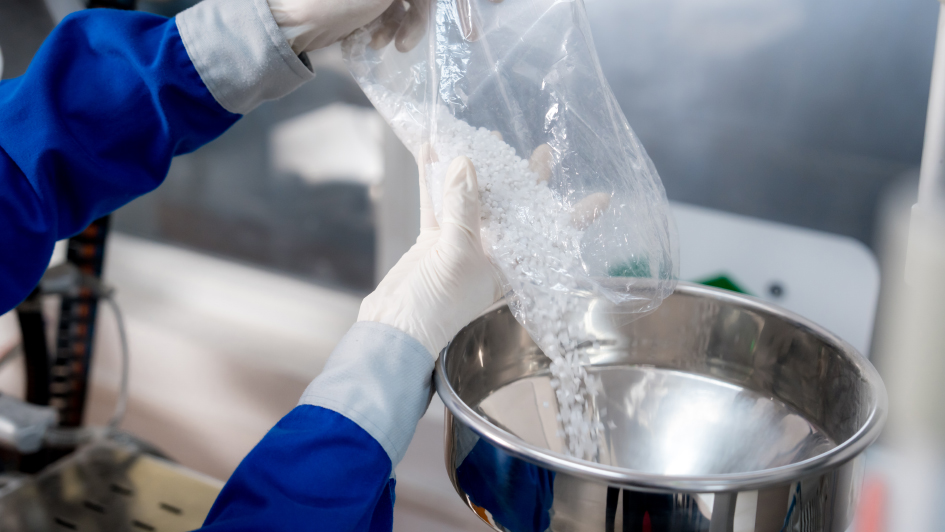
The trajectory of filler masterbatch research points toward further innovations in material science, particularly in developing novel filler materials and compounding techniques. The exploration of nanotechnology and sustainable bio-based fillers holds the potential to revolutionize the plastics industry, offering unprecedented improvements in product performance and environmental sustainability.
Conclusion
Integrating filler masterbatch into plastic production epitomizes the synergy between cost efficiency and scientific innovation. As research continues to deepen our understanding and application of these materials, the plastics industry stands on the cusp of a new era of sustainable, cost-effective manufacturing solutions. The ongoing exploration of filler masterbatch underscores its economic and environmental benefits and highlights the critical role of scientific research in shaping the future of plastic production.