Table of Contents
CaCO3 Filler Masterbatch for PE Film is a key strategy for modern manufacturers aiming to optimize costs without compromising quality. In the competitive and technically demanding European market, producers face growing pressure to deliver high-performance films at reduced costs for packaging, industrial, and agricultural applications. This case study reveals how Mega Plast, a leader in filler masterbatch innovation, partnered with a European PE film manufacturer to break through the limitations of the traditional “one-grade-fits-all” approach. The result? A tailored multi-grade solution that slashed production costs by 30–35% while maintaining top-tier film performance across a wide thickness range.
1. Introduction: The European Crucible of Cost and Quality
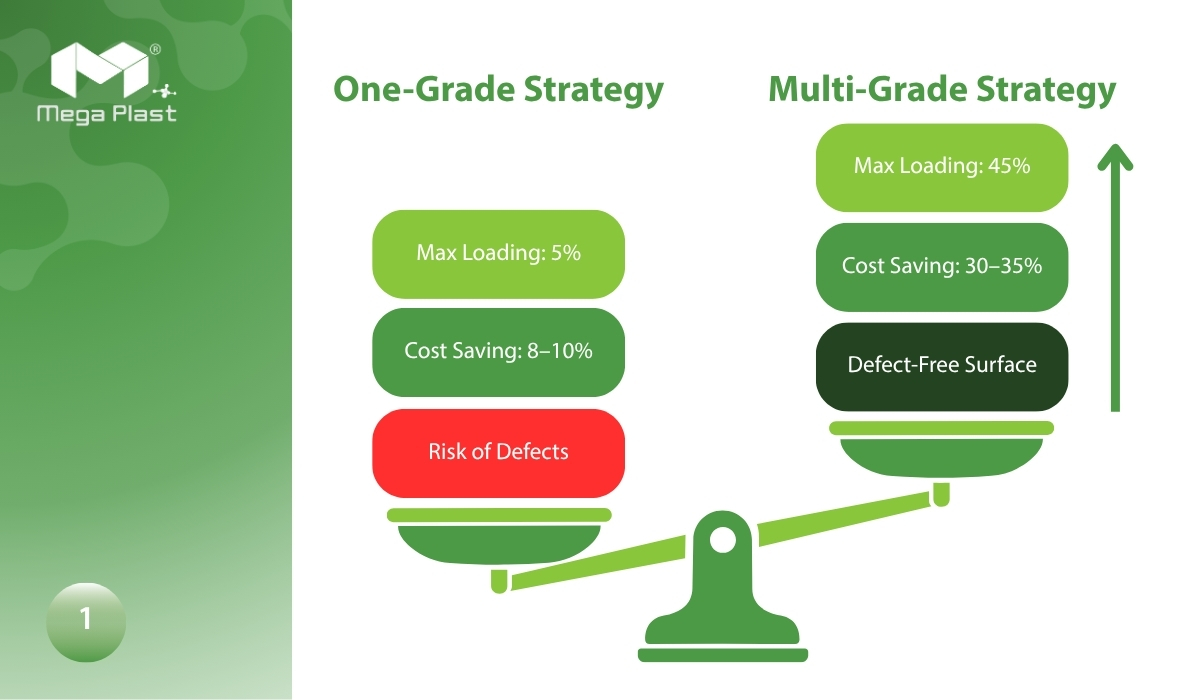
The European flexible packaging and industrial film market is defined by a complex interplay of economic pressures and rigorous technical mandates. End-users, from food and beverage giants to medical device companies and construction firms, demand impeccable film quality. This includes specific requirements for mechanical strength, optical clarity, surface finish, and barrier properties. Concurrently, European Union regulations, such as REACH (Registration, Evaluation, Authorisation and Restriction of Chemicals), impose strict compliance standards on all materials used in production.
Within this environment, raw material costs—primarily driven by the price of virgin polyethylene resins like LLDPE and LDPE—represent the largest portion of a film manufacturer’s operational expenditure. Any fluctuation in polymer pricing directly impacts profitability. Consequently, the use of high-quality filler masterbatches, typically based on calcium carbonate (CaCO3), has become a standard industry practice to displace a portion of the more expensive virgin resin.
This case study focuses on a leading European film manufacturer with a diverse product portfolio. Their offerings spanned the full spectrum of PE film applications, from ultra-thin 10-micron films for delicate packaging to robust 150-micron films for heavy-duty industrial use. This diversification, while a market strength, presented a significant and previously unsolved challenge in their production process. They approached Mega Plast with a critical strategic question: How could they move beyond incremental cost savings and achieve a profound reduction in raw material expenditure without jeopardizing the quality that defined their brand in the exacting European market?
2. The Challenge: Plateauing Performance of a Monolithic Strategy
The client’s existing production methodology was rooted in operational simplicity. For years, they had relied on a single, universal grade of calcium carbonate filler masterbatch for their entire product range. This approach, while straightforward from a procurement and inventory management perspective, had created a significant barrier to cost optimization.
The core limitations of their “one-grade-fits-all” strategy were:
- Non-Optimized Formulations: The universal filler was a compromise product, designed to be adequate for all applications but exceptional for none. For ultra-thin films, its particle size and dispersion characteristics were too coarse, posing a risk to film integrity. For thick films, its formulation was not engineered for the highest possible loading levels, leaving significant cost-saving potential untapped.
- Conservative Loading Rates: Fear of quality degradation was the primary constraint. To avoid issues like film tearing, “fisheyes” (gels or undispersed particles), surface scratches, or a reduction in tensile strength, the client capped the filler loading rate at a very conservative 5% across all film thicknesses. This was particularly true for their sub-25-micron films, where even minor imperfections could lead to catastrophic product failure.
- Marginal Cost Savings: A 5% loading rate translated into a raw material cost reduction of only 8-10%. While beneficial, this figure had stagnated for years and was insufficient to give them a decisive edge in a market where competitors were constantly innovating to lower their price points. The management team recognized that they had reached the performance plateau of their current strategy.
Their challenge to Mega Plast was not merely to supply a better filler; it was to re-engineer their entire approach to raw material formulation. They needed a strategic partner to help them break the 10% savings barrier and unlock the next level of production efficiency, all while guaranteeing compliance with Europe’s uncompromising technical standards.
3. The Mega Plast Solution: Tailored CaCO3 Filler Masterbatch for PE Film
The R&D and technical teams at Mega Plast approached the client’s problem not as a materials issue, but as a process engineering challenge. The central hypothesis was that a single filler grade could not possibly satisfy the vastly different rheological and mechanical demands of a 10-micron film versus a 150-micron film. The solution lay in specialization.
After a thorough audit of the client’s production lines, polymer formulations, and end-product technical data sheets, Mega Plast proposed a groundbreaking strategy: replacing the single universal grade with a system of three specialized, high-performance filler masterbatch grades. Each grade was meticulously engineered for a specific film thickness range, allowing for dramatically increased loading rates without compromising performance.

This multi-pronged solution was rolled out in three distinct categories:
✅ Category 1: Ultra-Thin Films (10–25µm)
- Recommended Product: MEGA PLAST F201
- Optimized Loading Rate: 25% (a 400% increase from the previous 5%)
- The Science Behind It: For ultra-thin films, the primary challenges are dispersion and particle size. Any agglomeration of filler particles can cause pinholes or lead to film tearing during the high-speed stretching of the film blowing process. F201 is manufactured using an exceptionally fine grade of ground calcium carbonate (D50 < 1.8µm) which undergoes a specialized surface treatment. This proprietary coating technology ensures hydrophilic CaCO3 particles are rendered hydrophobic, promoting seamless integration within the non-polar polyethylene matrix. The result is outstanding dispersion, eliminating the risk of film scratches and maintaining the superior tensile strength and clarity essential for premium packaging applications.
✅ Category 2: Thin to Medium-Thickness Films (25–35µm)
- Recommended Product: MEGA PLAST F261
- Optimized Loading Rate: 35% (a 600% increase from the previous 5%)
- The Science Behind It: This film range represents the “workhorse” of many packaging applications, such as shopping bags and standard food packaging. The quality requirements are still high, but there is more tolerance than in the ultra-thin category. F261 is engineered to provide the perfect equilibrium between particle size, dispersion, and cost-effectiveness. Its formulation allows for a significantly higher volume of filler to be incorporated, substantially displacing virgin resin. The particle distribution is carefully controlled to ensure a smooth surface finish and preserve the required mechanical properties, such as dart impact strength and elongation.
✅ Category 3: Thick Films (>35µm)
- Recommended Product: MEGA PLAST F251
- Optimized Loading Rate: 45% (an 800% increase from the previous 5%)
- The Science Behind It: In thicker films, such as those used for heavy-duty sacks, agricultural film, and construction sheeting, the primary goal is to maximize cost reduction while maintaining structural integrity and durability. F251 is an economic powerhouse, designed specifically for maximum filler incorporation. While still using high-purity calcium carbonate, the particle size can be slightly larger without impacting the film’s functional properties. This optimization for bulk loading delivers dramatic cost savings. Crucially, the formulation of F251 ensures excellent bonding with the polymer matrix, preventing delamination and maintaining the film’s puncture resistance and overall toughness, even at a near 50% loading rate.
4. Quantifiable Results: Exceeding All Expectations
The implementation of Mega Plast’s tailored, three-grade filler strategy was a resounding success, delivering transformative results that surpassed the client’s most optimistic projections. The impact was felt across financial, quality, and operational metrics.
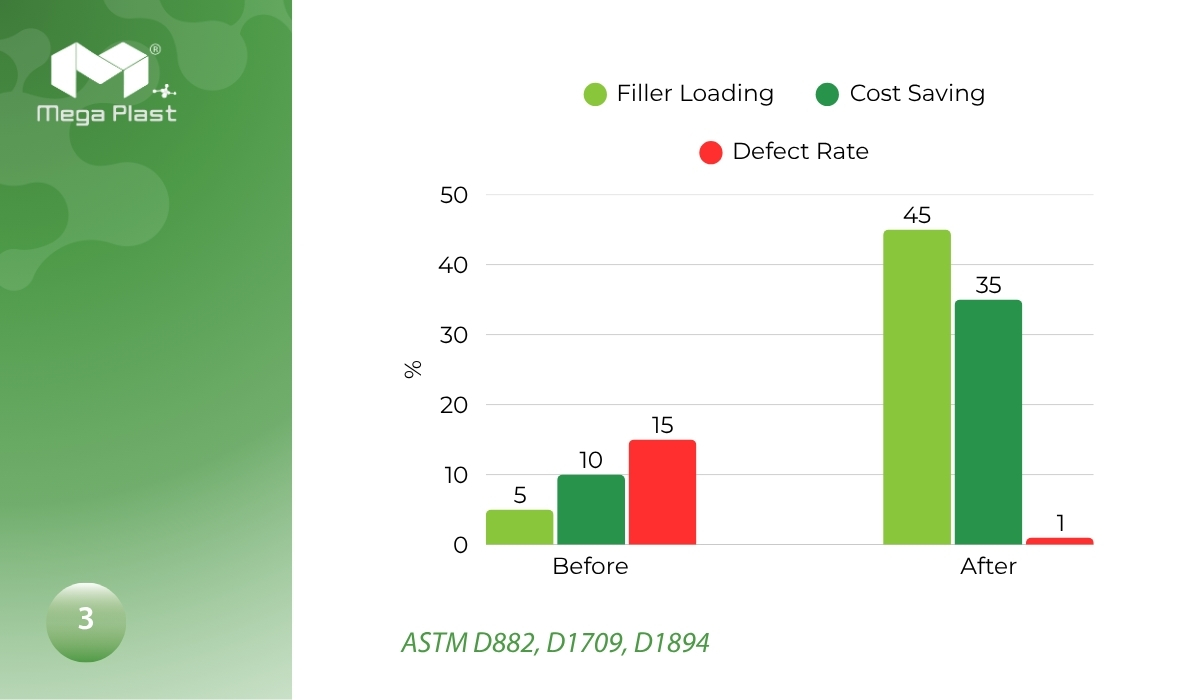
- ✨ Financial Impact: A Leap to 30-35% Cost Savings The most significant outcome was the drastic reduction in raw material costs. By strategically increasing loading rates from a flat 5% to as high as 45%, the overall production cost per kilogram of film plummeted. The initial savings of 8-10% were replaced by a new, sustainable saving of 30-35%. For a large-scale manufacturer, this translated into millions of Euros in annual savings, fundamentally strengthening their financial position and providing a massive competitive advantage in the price-sensitive European market.
- ✨ Quality Assurance: Uncompromised Technical Excellence A major concern at the outset was whether such high filler loads could pass Europe’s stringent quality tests. The results were definitive: every batch of film produced with the specialized F201, F261, and F251 grades met or exceeded all required technical specifications. Key performance indicators such as Tensile Strength and Elongation (ASTM D882), Dart Drop Impact Resistance (ASTM D1709), and Coefficient of Friction (ASTM D1894) were all within the acceptable ranges. The films exhibited flawless surface quality with no scratches or black spots, and the optical properties of the thinner films were maintained.
- ✨ Operational Efficiency: Smoother Production, Less Waste The tailored strategy introduced unforeseen operational benefits. Using a filler optimized for each specific process led to a more stable extrusion process. Issues like die lip buildup were significantly reduced, leading to less downtime for cleaning and maintenance. The excellent dispersion of the masterbatches resulted in more uniform film thickness and consistent roll geometry, which in turn reduced the scrap rate. This minimization of production waste not only saved material costs but also improved overall plant efficiency and throughput.
5. Conclusion: From Supplier to Strategic Partner
This case study provides unequivocal evidence that a “one-grade-fits-all” approach to filler masterbatch is a relic of a less optimized era. In today’s competitive landscape, true cost and quality optimization demand a more intelligent, scientific, and customized approach.
By deeply analyzing the customer’s unique production challenges and leveraging deep expertise in polymer science and material formulation, Mega Plast demonstrated its role not merely as a supplier of goods, but as a strategic partner in value creation. The courage to move away from a long-standing but inefficient tradition, combined with a data-driven, tailored solution, unlocked breakthrough results. This collaboration underscores a fundamental principle: innovative thinking and a commitment to customized solutions are the primary drivers of success in the modern manufacturing industry.
For manufacturers of PE films across multiple thicknesses, this case stands as a blueprint for success. If your organization has hit a plateau in cost savings, it may be time to challenge the status quo. Contact the experts at Mega Plast to design a tailored filler strategy that can unlock your production’s full potential for both quality and profitability.
Discover 100+ Types of Masterbatch: Mega Plast Provides Diverse Solutions for the Plastics Industry
