In today’s competitive manufacturing landscape, the ability to offer personalized and precise solutions is paramount. At Mega Plast, we understand that each industry and client has unique requirements, and we strive to meet these needs with our customized masterbatch solutions. This blog post will explore how Mega Plast tailors its masterbatch products to cater to specific industry demands, ensuring optimal performance, cost efficiency, and superior quality.
Understanding the Importance of Customization
The manufacturing sector is diverse, with each segment having distinct challenges and requirements. Whether it’s the household goods industry needing materials with specific aesthetic qualities, the packaging industry requiring enhanced functional properties, or the textile industry seeking improved fiber properties, the need for specialized solutions is evident. Customization in masterbatch solutions allows manufacturers to:
- Achieve specific mechanical and physical properties.
- Enhance aesthetic appeal with precise color matching.
- Improve processability and production efficiency.
- Meet regulatory and environmental standards.
Mega Plast’s Approach to Customized Solutions
At Mega Plast, we take a comprehensive customization approach, from understanding our clients’ needs to providing ongoing support and refinement. Here’s how we ensure our masterbatch solutions are perfectly tailored to meet specific industry requirements:
1. In-depth consultation and Needs Assessment
Our journey with clients begins with a thorough consultation. We take the time to understand their production processes’ specific challenges, goals, and requirements. This involves:
- Detailed discussions about the desired properties of the final product.
- Analysis of existing production processes and materials.
- Identification of any issues or inefficiencies that need to be addressed.
2. Collaborative Development and Testing
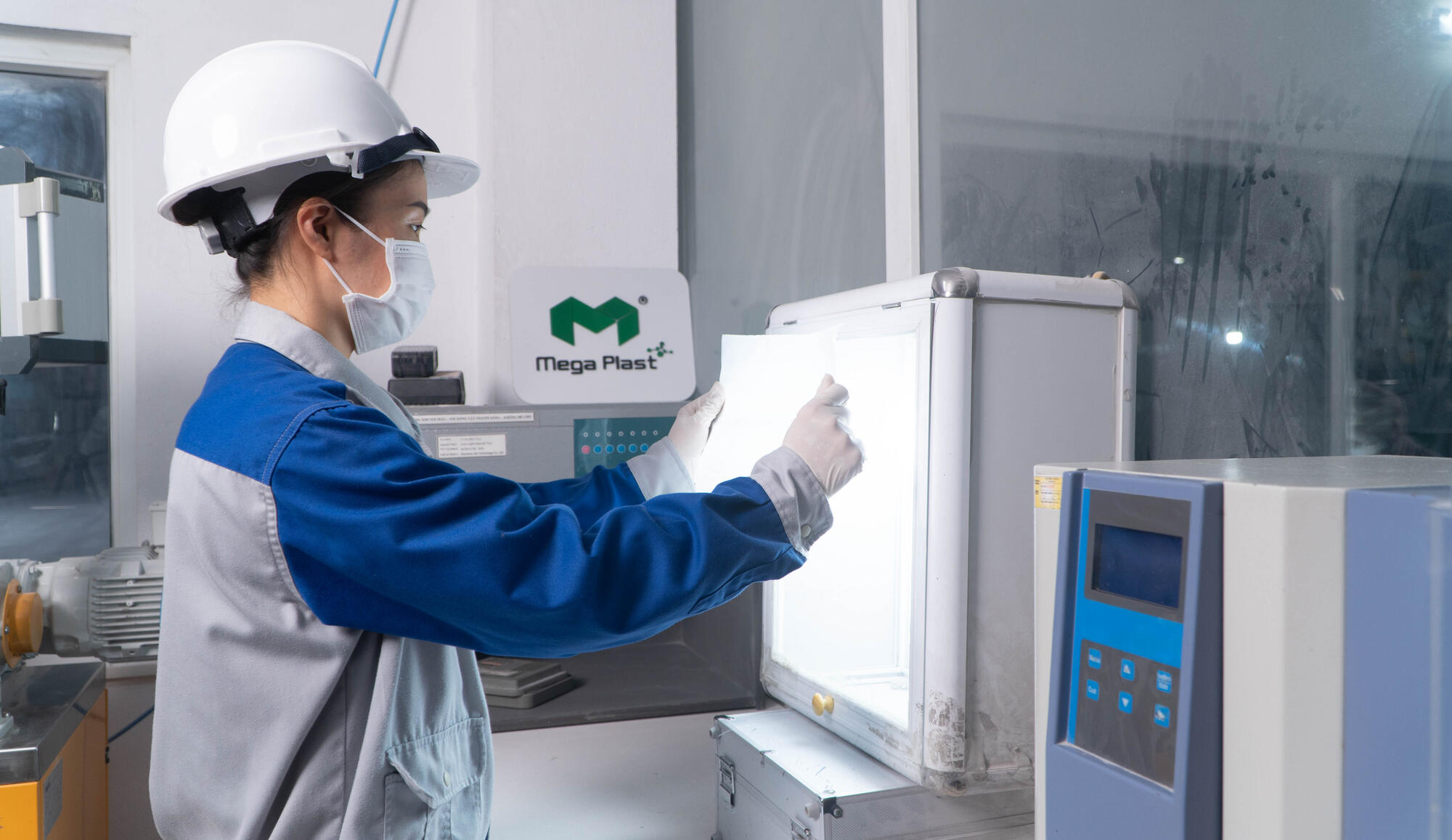
Once we have a clear understanding of our client’s needs, our R&D team collaborates closely with them to develop customized masterbatch formulations. This phase includes:
- Experimenting with different formulations to achieve the desired properties.
- Conducting rigorous testing to ensure compatibility and performance.
- Iterating based on feedback and test results to refine the product.
3. Precision Manufacturing
With the final formulation ready, we move into the manufacturing phase. Mega Plast utilizes state-of-the-art equipment and strict quality control measures to ensure consistency and reliability. Our manufacturing process includes:
- High-precision mixing and compounding to achieve uniformity.
- Stringent quality checks at every stage to maintain product integrity.
- Flexibility in production runs to accommodate varying order sizes.
4. Comprehensive Support and Optimization
Our commitment to clients doesn’t end with the delivery of the masterbatch. We provide ongoing support to ensure the successful integration and optimal performance of our products. This support includes:
- Technical assistance during the initial implementation phase.
- Regular follow-ups to address any issues or adjustments needed.
- Continuous improvement and updates to keep up with evolving industry needs.
Case Studies: Success Stories of Customized Solutions
Household Goods Industry: Enhanced Aesthetics and Functionality
A leading household goods manufacturer approached Mega Plast with the need for a masterbatch that could enhance the aesthetic qualities and functionality of their products. Through collaborative development, we formulated a masterbatch with specific additives and pigments that significantly improved the visual appeal and durability of their items. The result was a more attractive and reliable product line, leading to higher customer satisfaction and increased market share.
Packaging Industry: Superior Aesthetics and Processability
An innovative packaging company needed a masterbatch that could provide vibrant colors while also improving the processability of their materials. Mega Plast worked closely with their team to develop a color masterbatch that not only met their aesthetic requirements but also enhanced the flow properties of the polymer melt. This led to smoother production processes, reduced cycle times, and eye-catching packaging that stood out on the shelves.
Textile Industry: Improved Fiber Quality
A textile manufacturer faced issues with the consistency and quality of their fibers. Mega Plast developed a customized masterbatch that included specific additives to enhance fiber strength and uniformity. The implementation of this solution resulted in higher-quality textiles, increased production efficiency, and reduced material waste.
The Mega Plast Advantage
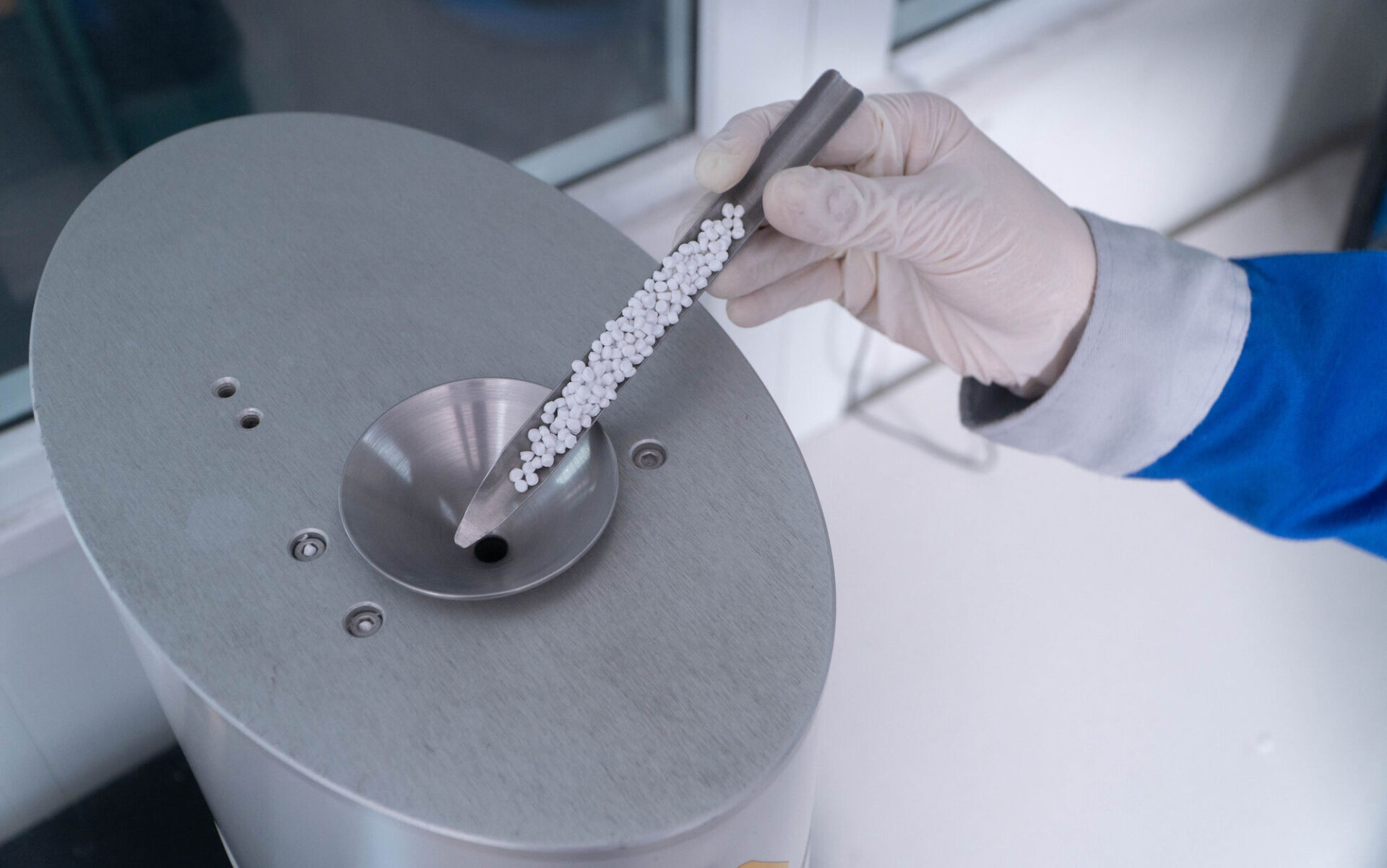
Choosing Mega Plast for your masterbatch needs offers several distinct advantages:
- Expertise and Experience: With years of experience in the industry, our team has the knowledge and skills to develop solutions that meet the highest standards.
- Innovation and Flexibility: We stay ahead of industry trends and continuously innovate to offer the latest in masterbatch technology.
- Customer-Centric Approach: Our focus is on building strong, lasting relationships with our clients, ensuring their success is our top priority.
- Sustainability: We are committed to providing environmentally friendly solutions that help our clients reduce their ecological footprint.
Conclusion
In a world where one-size-fits-all solutions often fall short, Mega Plast stands out by offering customized masterbatch solutions that are specifically designed to meet the unique needs of different industries. Our comprehensive approach—from initial consultation to ongoing support—ensures that our clients receive products that meet their requirements and drive efficiency, quality, and success.
Contact us today for more information on how Mega Plast can provide customized masterbatch solutions for your industry. Let’s collaborate to create innovative solutions that set you apart from the competition.