Introduction: Mastering the Art of Masterbatch Production
Masterbatch, a vital component in the plastics industry, plays a pivotal role in enhancing the properties of plastic products. The production of masterbatch involves intricate processes, each designed to meet specific requirements and deliver optimal results. In this article, we delve into the methods of producing masterbatch, exploring both single-stage and two-stage processes that contribute to the creation of high-quality masterbatch solutions.
Understanding the Masterbatch Production Process
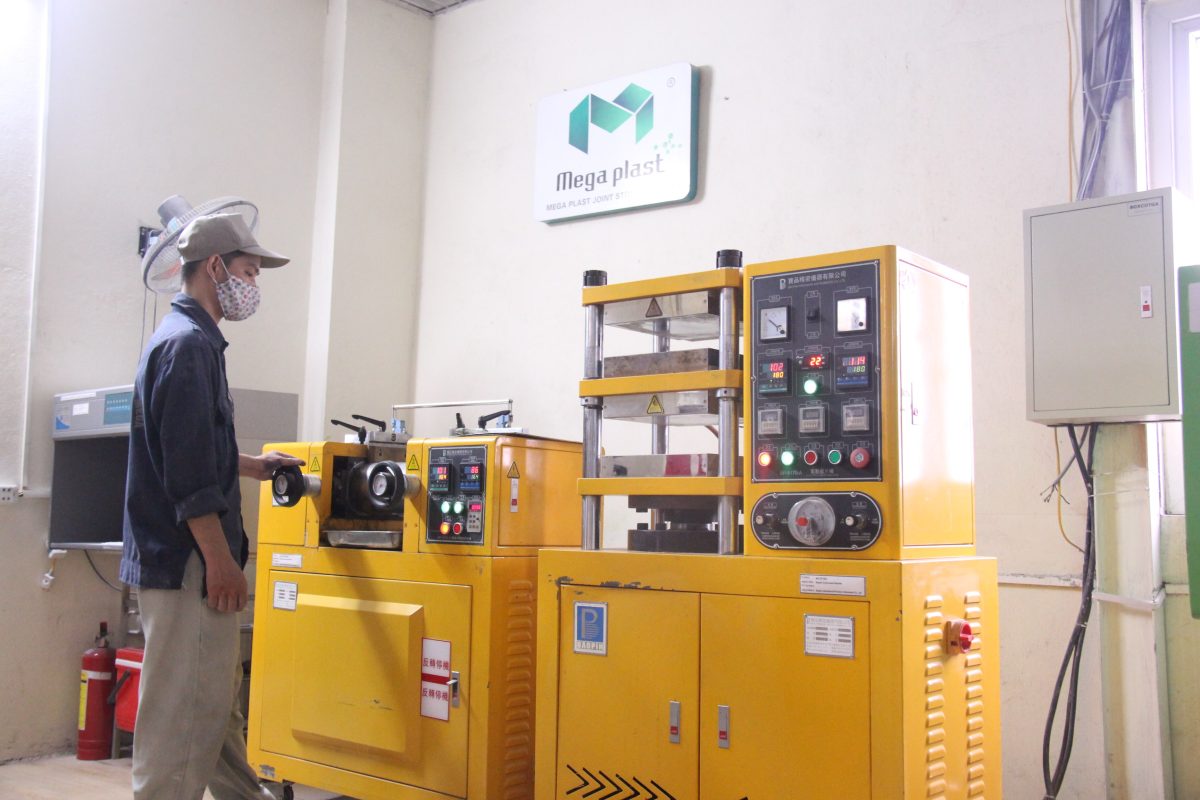
The production of masterbatch is a carefully orchestrated process, where various components are combined to achieve the desired characteristics in the final plastic product. Let’s break down the key steps involved in the masterbatch production process:
- Premixing:
- A premix, consisting of polymer, pigment, and dispersion additive, serves as the foundation.
- This premix is fed into an extruder, the heart of the production process.
- Extrusion:
- The premix undergoes extrusion, where it is subjected to heat and pressure.
- This process ensures the thorough mixing of polymer, pigment, and dispersion additive.
- Container Mixing:
- Container mixers further refine the mixture, enhancing dispersion and distribution.
- Degassing and Venting:
- To eliminate any trapped gases and ensure the quality of the final product, degassing and venting steps are crucial.
- Volumetric Dosing Unit:
- A precisely controlled dosing unit adds specific quantities of components to achieve the desired masterbatch composition.
- Pelletization:
- The processed mixture is pelletized to create uniform, manageable particles.
- ZSE MAXX and Water Bath:
- Specialized equipment like ZSE MAXX may be employed for specific applications, and a water bath is used to cool and solidify the pellets.
- Specialized equipment like ZSE MAXX may be employed for specific applications, and a water bath is used to cool and solidify the pellets.
Methods of Producing Masterbatch: Single-Stage Process
Overview:
- In the single-stage process, all components, including polymer, pigment, and additives, are combined in one processing step.
- This streamlined approach simplifies the production process and can be applied to various types of masterbatch.
Advantages:
- Simplicity: The single-stage process is straightforward and efficient.
- Applicability: Suitable for producing all three types of masterbatch – color, additive, and filler masterbatch.
Considerations:
- Compatibility: Ensuring compatibility of all components is crucial for a successful single-stage process.
- Process Flexibility: While versatile, this method may have limitations in specific applications.
Methods of Producing Masterbatch: Two-Stage Process
Overview:
- The two-stage process involves producing single pigments in the first stage.
- The second extrusion step combines the required ratio of colorant and additive, specifically applicable to color masterbatch.
Advantages:
- Precision: Allows for precise control over colorant and additive ratios.
- Specialization: Ideal for applications where color accuracy is paramount.
Considerations:
- Limited Applicability: Primarily used for color masterbatch production.
- Process Complexity: The two-stage process involves additional steps, requiring careful coordination.
Conclusion: Mastering Masterbatch Production
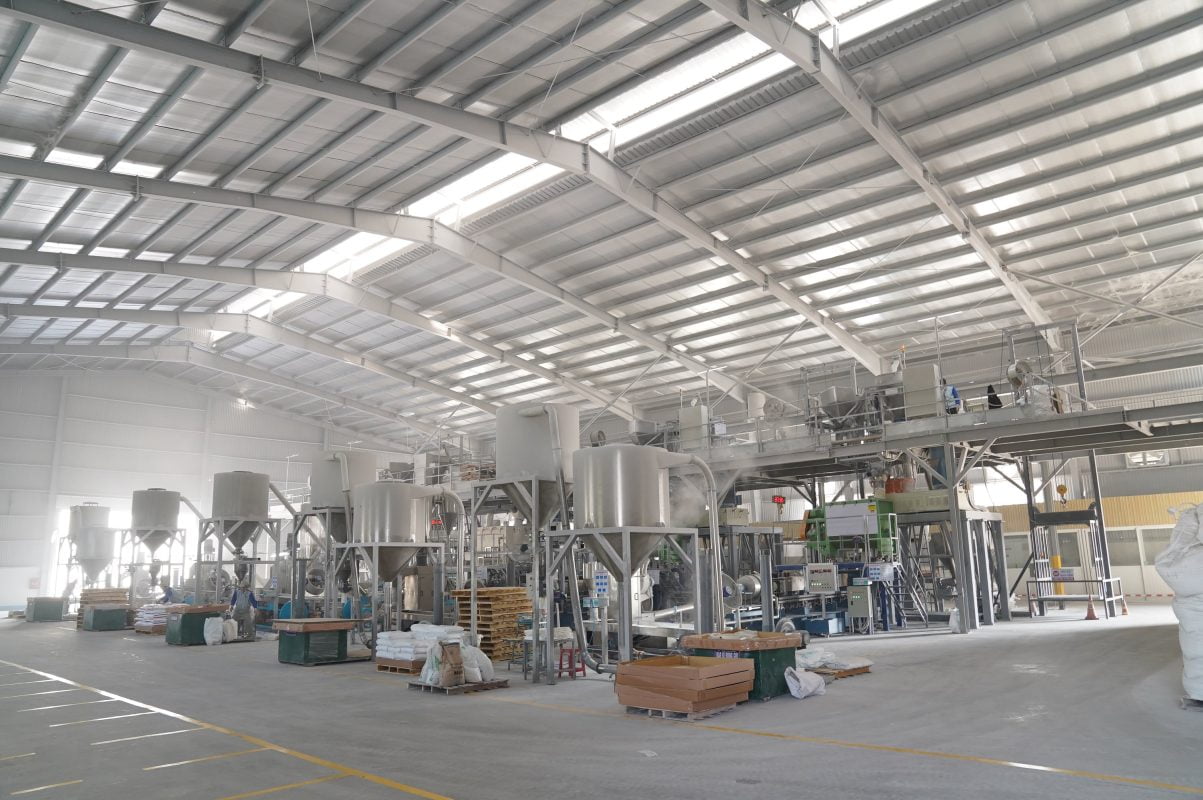
Understanding the methods of producing masterbatch is essential for manufacturers aiming to deliver high-quality plastic products. Whether opting for the simplicity of the single-stage process or the precision of the two-stage process, manufacturers can tailor their approach to meet specific industry needs. By mastering the art of masterbatch production, the plastics industry can continue to innovate, ensuring that products meet stringent standards and customer expectations.