Table of Contents
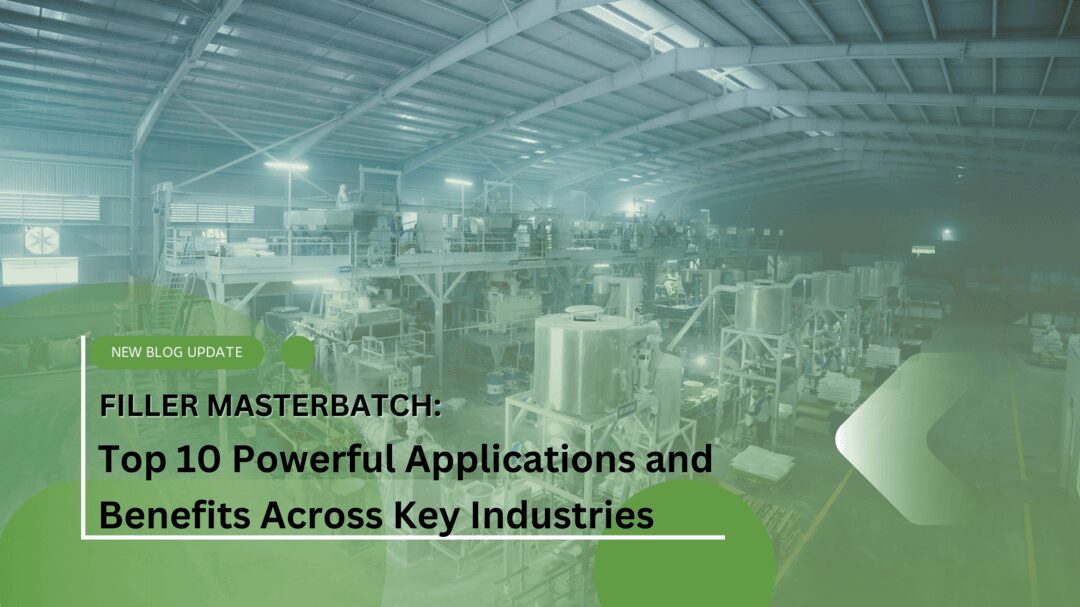
In the world of plastic manufacturing, Filler Masterbatch or Calcium Carbonate (CaCO3) Filler Masterbatch has become an essential component for optimizing production costs, enhancing product durability, and improving overall performance. Used across a wide range of industries, Filler Masterbatch helps manufacturers maintain product quality while reducing reliance on expensive virgin resin. Whether it’s in Injection Moulding, Extrusion, Blow Moulding, or Film Blowing, Filler Masterbatch plays a vital role in driving efficiency and competitiveness.
Thanks to the strategic partnership with a calcium carbonate factory Global Minerals, Megaplast is able to offer Filler Masterbatch at lower production costs, providing a competitive edge for manufacturers. Calcium carbonate is the main raw material used in filler production, ensuring both quality and cost stability. This enables customers not only to reduce production costs by 20% but also to enhance their competitiveness in the global market.
In this article, we will explore the key applications of Filler Masterbatch in different industries, its benefits, and real-world examples of how it contributes to cost-effective manufacturing.
Key Industries and Applications of Filler Masterbatch
Filler Masterbatch is used across a variety of industries, each with specific production needs and benefits. Below, we explore its use in the most common processes, including Injection Moulding, Extrusion, Blow Moulding, and Film Blowing.
1. Filler Masterbatch in Injection Moulding
What is Injection Moulding?
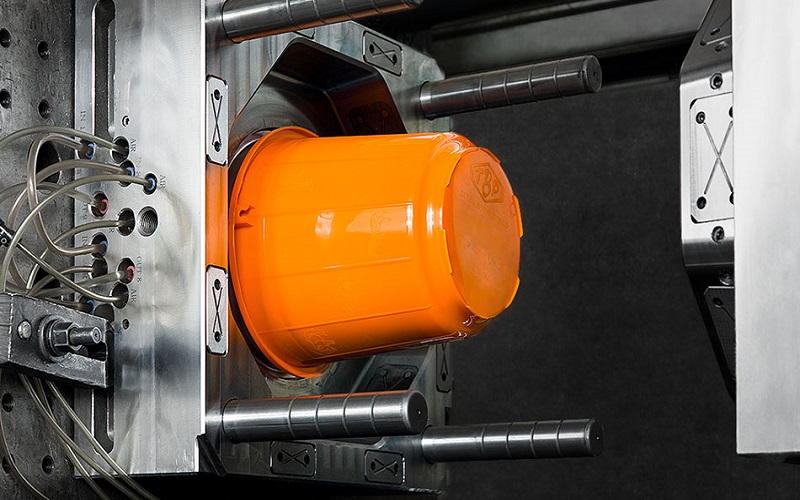
Injection Moulding is a manufacturing process used to produce plastic parts by injecting molten plastic into a mould. This process is widely used for producing durable plastic products, especially in household goods, automotive parts, and industrial components.
How Filler Masterbatch Enhances Injection Moulding
- Cost savings: Filler Masterbatch can replace apart of virgin resin, significantly reducing material costs.
- Improved strength: Adding Filler Masterbatch enhances the stiffness and durability of products like household appliances, automotive parts, and electronic casings.
Examples of Products
- Household items: Plastic chairs, containers, kitchenware, and other durable products are made more cost-effective and stronger with Filler Masterbatch.
- Automotive parts: High-performance filler materials are used in producing lightweight yet durable components like bumpers, dashboards, and internal panels.
Learn more about Filler Masterbatch applications in Injection Moulding →
2. Filler Masterbatch in Extrusion
What is Extrusion?

Extrusion is the process of creating objects with a fixed cross-sectional profile by forcing molten plastic through a die. It is primarily used to produce continuous plastic items like pipes, sheets, and profiles.
How Filler Masterbatch Benefits Extrusion
- Reduced costs: Filler Plastic Masterbatch allows manufacturers to lower the use of virgin resin, which reduces production costs.
- Increased stiffness: Filler Plastic Masterbatch strengthens the extruded plastic products without compromising flexibility.
Examples of Products
- Pipes: Filler Masterbatch is widely used in the production of PVC, PE, and HDPE pipes, improving their strength and reducing costs.
- Plastic sheets: Used in construction and packaging, plastic sheets made with Filler Masterbatch are more durable and cost-efficient.
Discover how Filler Masterbatch optimizes the Extrusion process →
3. Filler Masterbatch in Blow Moulding
What is Blow Moulding?
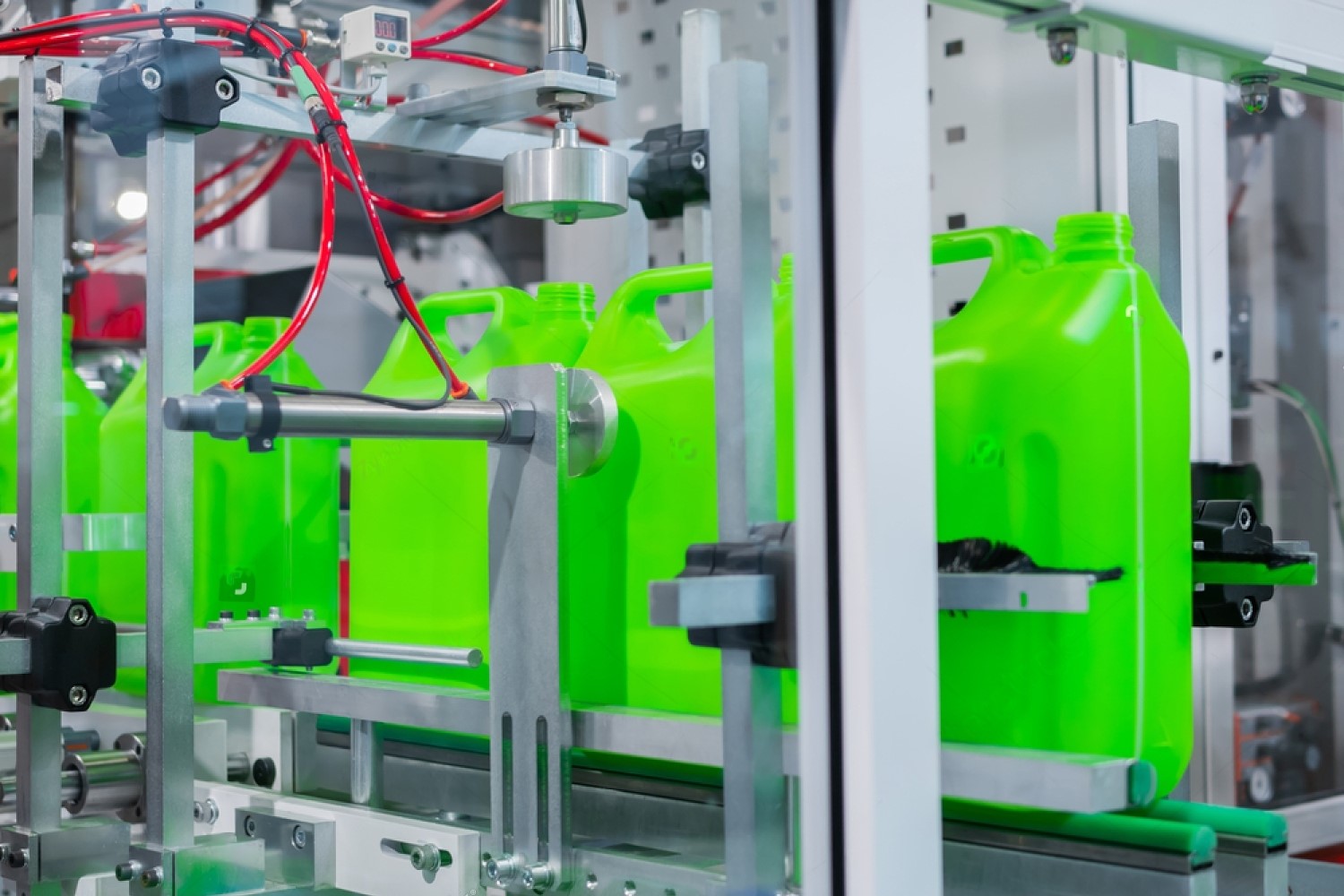
Blow Moulding is a process used to manufacture hollow plastic products, such as bottles, containers, and tanks, by blowing air into molten plastic to shape it within a mould.
How Filler Masterbatch Improves Blow Moulding
- Cost efficiency: Filler Masterbatch reduces the need for virgin resin, lowering production costs for large-volume items.
- Strength and durability: Products created using Filler Masterbatch are stronger and more resistant to wear and tear.
Examples of Products
- Plastic bottles: Filler Masterbatch is commonly used in manufacturing water bottles, detergent bottles, and other containers, providing cost savings and increased strength.
- Plastic tanks: Larger products such as water tanks and storage containers benefit from the use of Filler Masterbatch for cost reduction and durability.
Explore Filler Masterbatch applications in Blow Moulding →
4. Filler Masterbatch in Film Blowing
What is Film Blowing?
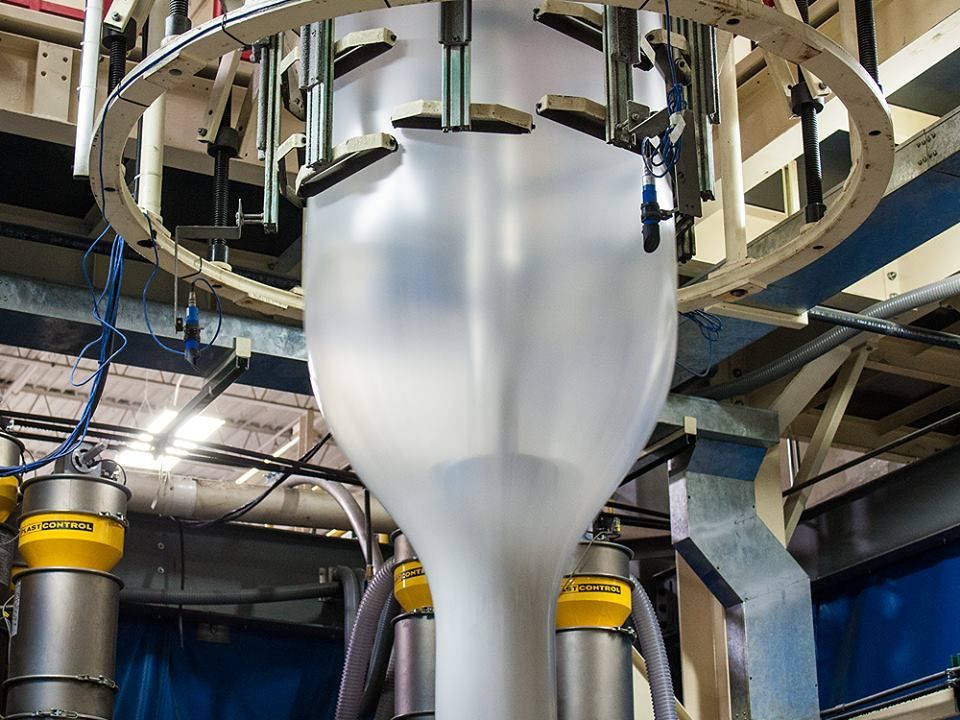
Film Blowing is the process used to produce plastic films by blowing molten plastic into a bubble, then flattening it into thin layers. This technique is commonly used in packaging, agriculture, and industrial films.
How Filler Masterbatch Enhances Film Blowing
- Lower production costs: Filler Masterbatch replaces part of the virgin resin, significantly cutting down on production expenses.
- Improved mechanical properties: It strengthens the plastic film, making it more tear-resistant and suitable for demanding applications.
Examples of Products
- Plastic bags: Filler Masterbatch is used in producing PE, PP, and HDPE bags, improving their durability and reducing production costs.
- Agricultural films: Widely used in crop protection, Filler Masterbatch helps enhance the strength and lifespan of agricultural films.
Learn more about Filler Masterbatch in Film Blowing →
5. Filler Masterbatch in Non-Woven Fabrics
What is Non-Woven Fabric?
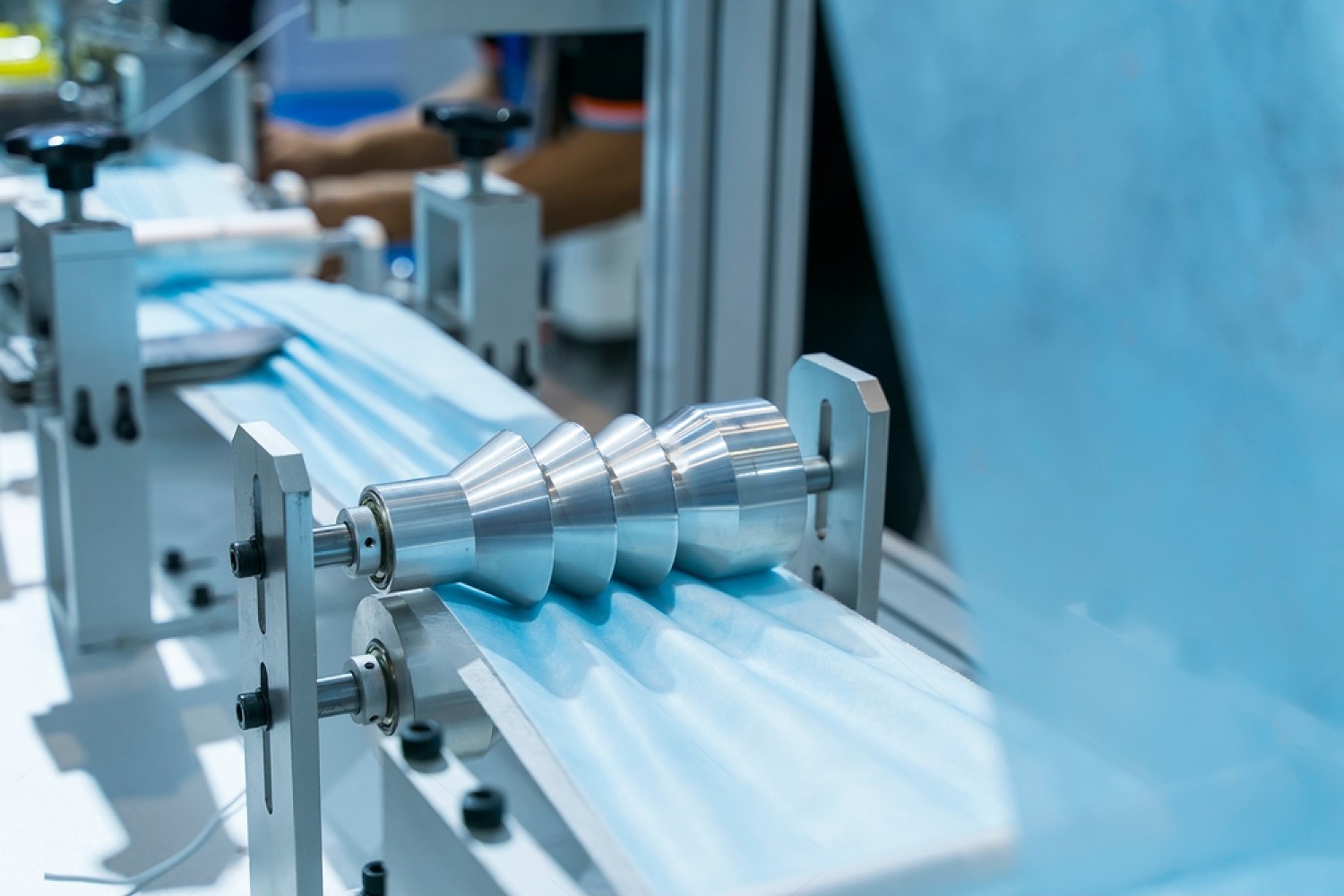
Non-woven fabrics are made from short fibers or filaments bonded together by mechanical, chemical, or thermal processes. Commonly used in products like face masks, medical gowns, and reusable bags, these fabrics are known for their versatility and cost-effectiveness.
How Filler Masterbatch Improves Non-Woven Fabrics
- Cost efficiency: Filler Masterbatch reduces the need for expensive virgin resin, making it a more economical option in the production of non-woven fabrics.
- Improved product properties: It enhances the strength, durability, and breathability of non-woven fabrics without affecting their lightweight nature.
Examples of Products
- Face masks: Filler Masterbatch ensures that masks maintain their integrity, providing both comfort and protection.
- Reusable bags: Used in eco-friendly shopping bags, filler helps reduce costs while ensuring durability.
Explore Filler Masterbatch applications in Non-Woven Fabrics →
6. Filler Masterbatch in Woven Fabrics
What is Woven Fabric?
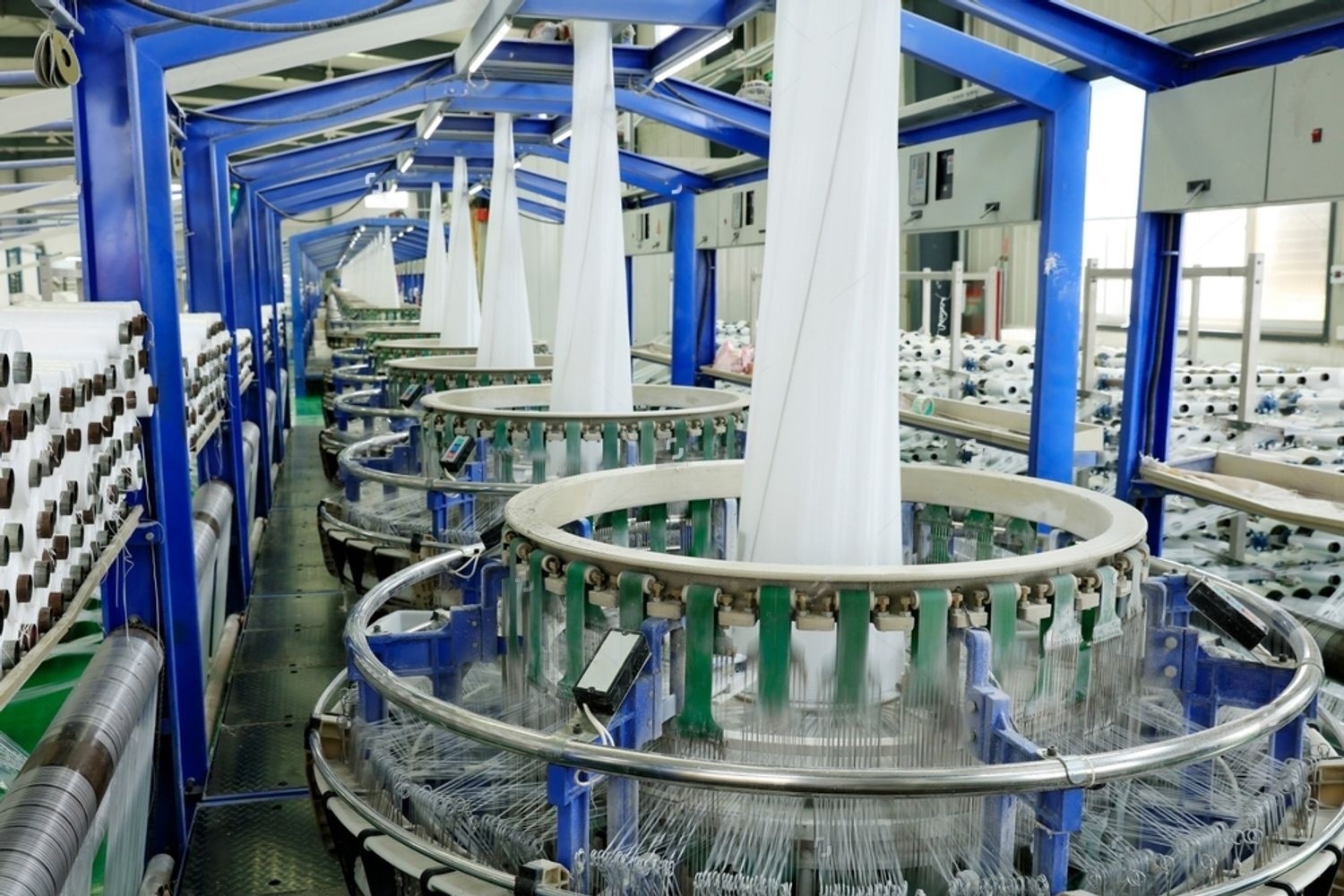
Woven fabrics are produced by interlacing two sets of yarns or threads at right angles. These fabrics are commonly used in industrial sacks, packaging materials, and geotextiles due to their high strength and durability.
How Filler Masterbatch Improves Woven Fabrics
- Cost savings: Filler Masterbatch reduces the reliance on virgin resin, lowering production costs significantly.
- Enhanced durability: It increases the tensile strength and tear resistance of woven fabrics, making them more suitable for heavy-duty applications.
Examples of Products
- Woven sacks: Filler Masterbatch is widely used in producing durable woven sacks for agricultural and industrial use.
- Geotextiles: In civil engineering, woven fabrics enhanced with filler masterbatch are used to provide strength and stability for infrastructure projects.
Learn more about Filler Masterbatch in Woven Fabrics →
7. Filler Masterbatch in Tarpaulin
What is Tarpaulin?
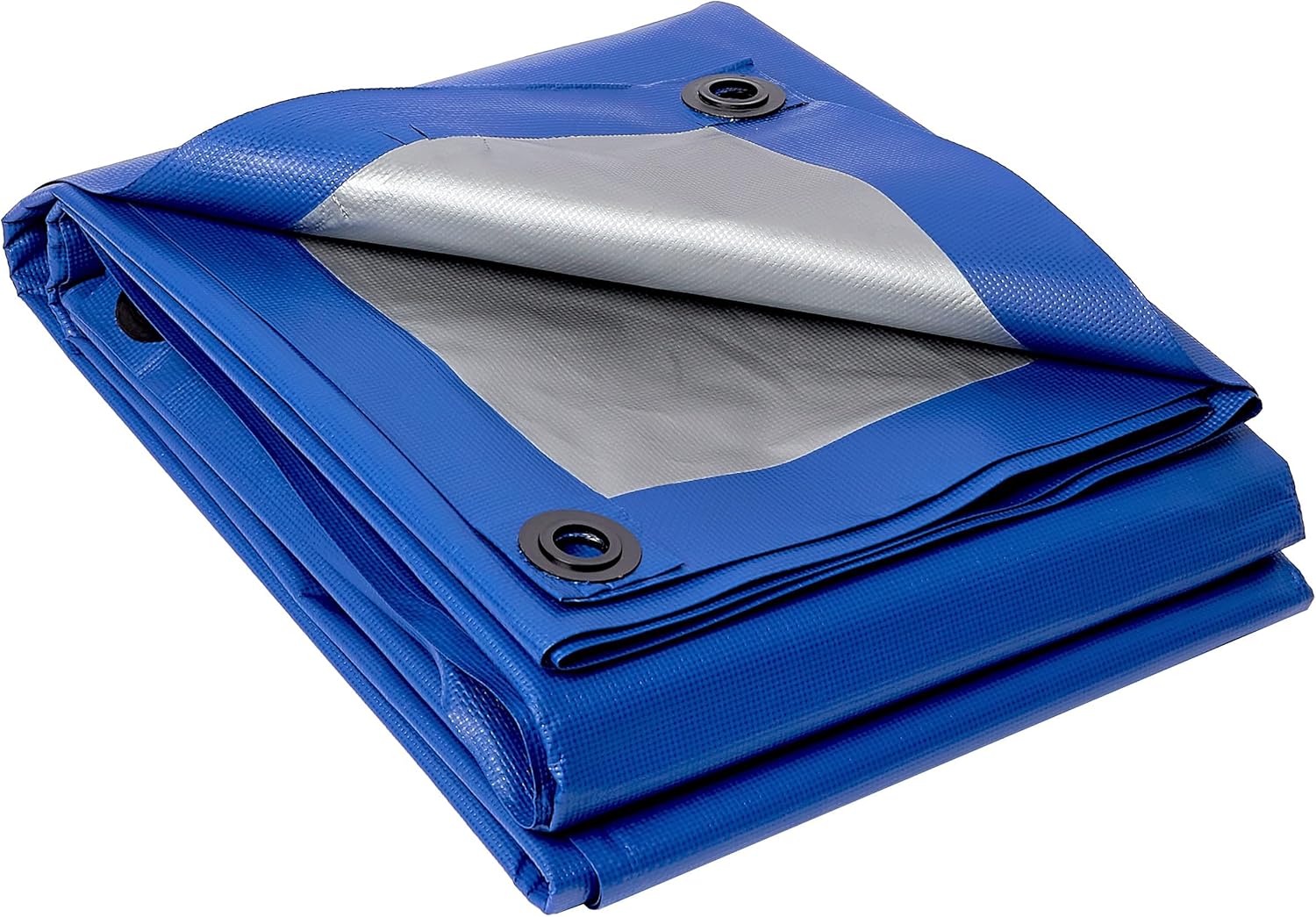
Tarpaulin is a large sheet of strong, flexible material typically used to cover and protect objects from weather elements. Made from plastic, it is used for truck covers, construction site protection, and agricultural purposes.
How Filler Masterbatch Improves Tarpaulin
- Cost-effectiveness: Using filler masterbatch reduces the overall cost of producing tarpaulin by decreasing the amount of virgin resin required.
- Enhanced durability: Filler Masterbatch improves the tear resistance, waterproof properties, and UV stability of tarpaulins, ensuring they last longer in harsh outdoor environments.
Examples of Products
- Truck covers: Tarpaulin made with filler masterbatch provides durable protection against rain and sun for trucks.
- Agricultural covers: Tarps used in farming benefit from increased UV resistance and strength.
Explore Filler Masterbatch applications in Tarpaulin →
8. Filler Masterbatch in Thermoforming
What is Thermoforming?

Thermoforming is a manufacturing process where a plastic sheet is heated and formed into specific shapes using a mould. This process is commonly used for producing food packaging, trays, and plastic containers.
How Filler Masterbatch Improves Thermoforming
- Cost reduction: Filler Masterbatch reduces the need for virgin resin, cutting down production costs while maintaining product quality.
- Increased rigidity: Thermoformed products benefit from the added stiffness and structural integrity that filler masterbatch provides.
Examples of Products
- Food packaging: Filler Masterbatch is used to create sturdy and cost-effective packaging solutions in the food industry.
- Plastic trays: Durable plastic trays and containers for food or industrial use are often enhanced with filler masterbatch.
Learn more about Filler Masterbatch in Thermoforming →
9. Filler Masterbatch in Lamination
What is Lamination?

Lamination involves bonding multiple layers of material together to improve strength, durability, and barrier properties. This process is widely used in food packaging, construction materials, and industrial films.
How Filler Masterbatch Improves Lamination
- Cost savings: Filler Masterbatch helps reduce the cost of lamination by replacing a portion of the virgin resin used in the process.
- Improved strength and stiffness: It enhances the mechanical properties of laminated products, ensuring they are more robust and durable.
Examples of Products
- Food packaging: Laminated films with filler masterbatch are used to create flexible, durable packaging for food items.
- Construction materials: Laminated sheets and films used in construction benefit from increased strength and longevity when enhanced with filler masterbatch.
Explore Filler Masterbatch applications in Lamination →
10. Filler Masterbatch in Roto Moulding
What is Pipe Extrusion?
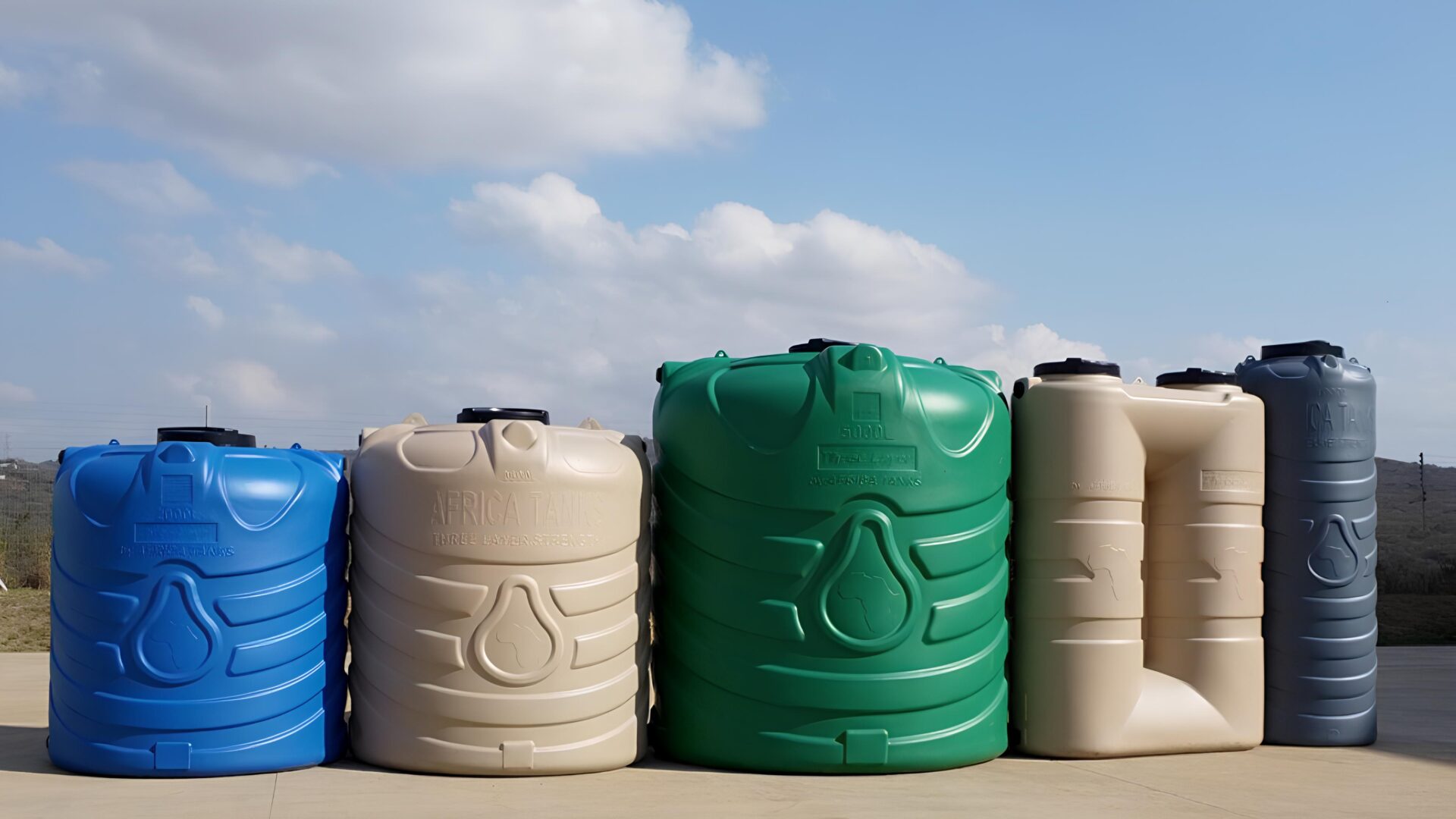
Rotational moulding for hollow products like tanks and bins, allowing complex shapes.
How Filler Masterbatch Enhances Roto Moulding:
- Reduced Costs: Replaces virgin resin, lowering production expenses.
- Improved Rigidity: Ensures structural integrity in large items.
Examples of Products
- Water Tanks: Provides durable and cost-effective storage.
- Plastic Bins: Ideal for robust and long-lasting waste containers.
Learn more about Filler Masterbatch in Roto Moulding →
The Advantages of Using Filler Masterbatch Across Industries
Using Filler Masterbatch provides several key benefits that apply to all industries:
- Cost Savings: Reduces the need for virgin resin, significantly lowering production costs.
- Improved Product Quality: Enhances stiffness, durability, and mechanical properties.
- Sustainability: Decreases virgin plastic usage, contributing to eco-friendly production.
Conclusion: Why Choose Filler Masterbatch for Your Production Process
Whether you’re manufacturing household items, automotive parts, pipes, or plastic films, Filler Masterbatch offers an effective way to reduce production costs and enhance product quality. Its versatility and cost-saving benefits make it an essential component in modern plastic manufacturing.
If you’re looking for a way to optimize your production process, consider incorporating Filler Masterbatch into your operations.
Contact us today for more information on how Filler Masterbatch can help your business save on costs and improve product quality.