In blow film extrusion manufacturing, the use of filler masterbatch for blow film has become increasingly important for enhancing product quality, reducing production costs, and improving environmental sustainability. This comprehensive guide explores the key benefits, diverse applications, and significant cost-saving advantages of incorporating filler masterbatch into the blow film extrusion manufacturing process.
Table of Contents
1. Introduction to Filler Masterbatch in Blow Film Extrusion Production
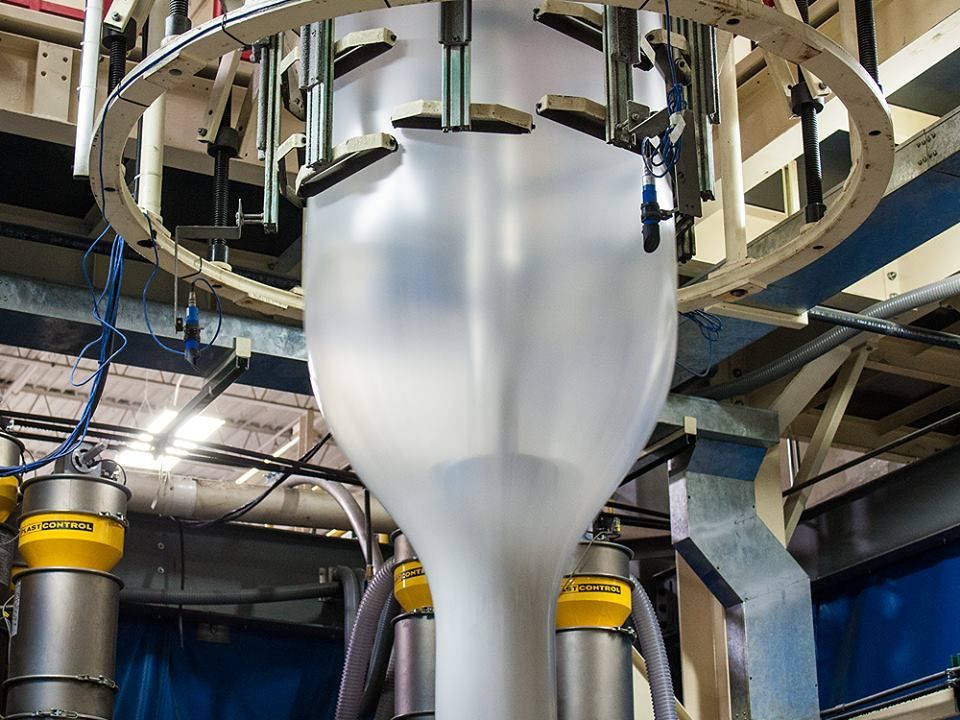
Filler masterbatch (Calcium Carbonate Filler Masterbatch) is a compound consisting of a high concentration of fillers like calcium carbonate (CaCO3) or talc, dispersed in a carrier resin. In blow film manufacturing, filler masterbatch is blended with primary polymer materials, such as polyethylene (PE) or polypropylene (PP), to create films with specific desired properties. This process not only optimizes raw material usage but also brings enhanced qualities to the final product.
Blow film is a popular process used in the production of plastic films for packaging, shopping bags, and agricultural covers, among other applications. Filler masterbatch plays a crucial role in this process by balancing cost and performance to meet market demands for both affordability and durability.
Understanding more about blowing film process
2. Key Benefits of Using Filler Masterbatch for Blow Film Extrusion
2.1 Cost Reduction
One of the most attractive advantages of using filler masterbatch in blow film production is its cost-saving potential. By substituting a portion of the more expensive base resin with filler masterbatch, manufacturers can significantly reduce the amount of virgin polymer required, leading to immediate cost savings. For example, calcium carbonate, one of the most commonly used fillers, is cheaper than traditional polymers, allowing manufacturers to decrease raw material expenses without compromising product quality.
2.2 Enhanced Film Strength and Durability
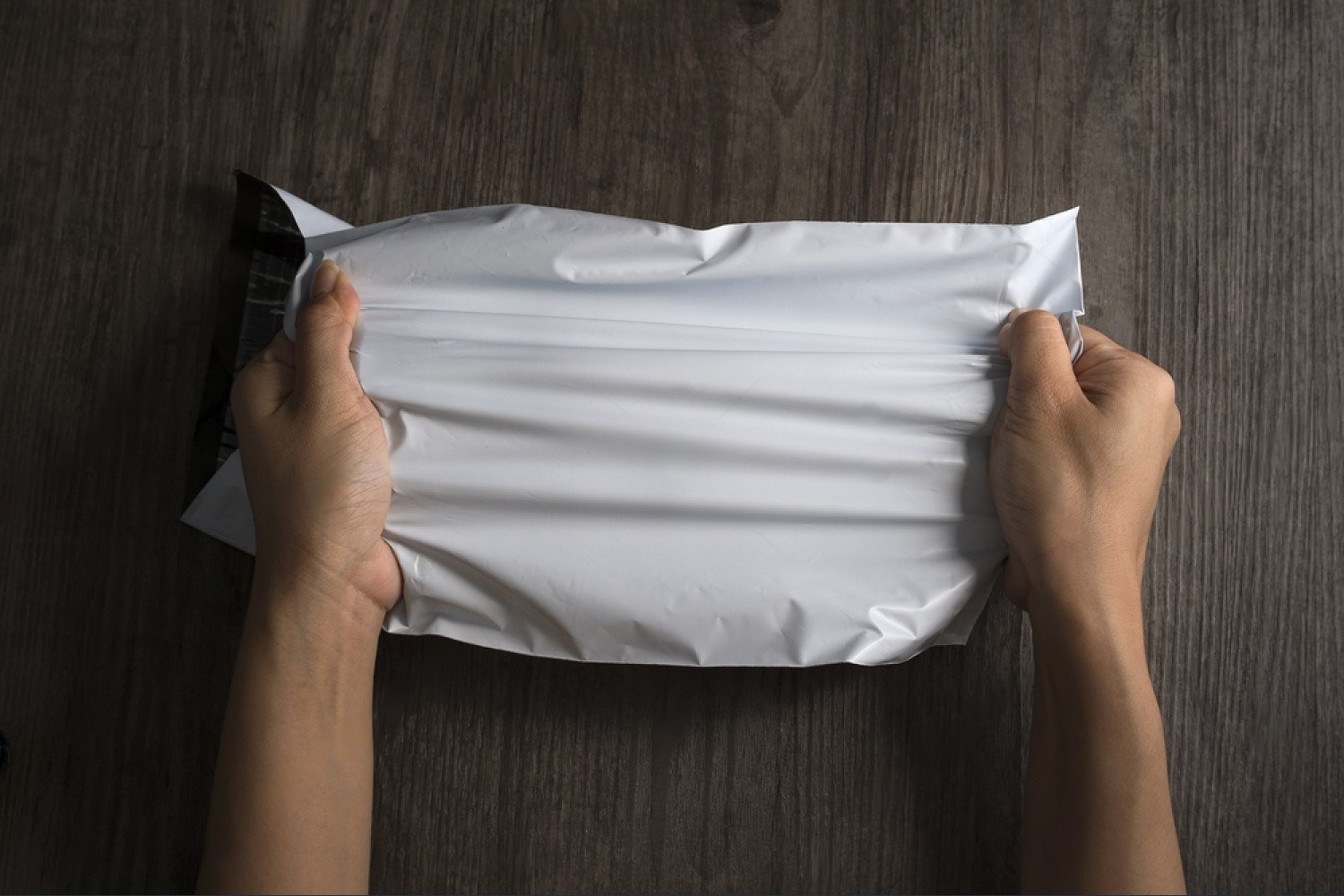
Filler masterbatch for blow film can enhance the mechanical properties of the final film, including tensile strength, tear resistance, and puncture resistance. These improvements contribute to better overall durability, allowing for the production of robust films that are less likely to tear or break during use. The filler particles help reinforce the polymer matrix, resulting in stronger and more resilient films suitable for demanding applications.
2.3 Improved Film Appearance and Opacity
In many blow film applications, especially packaging, a certain level of opacity is preferred. Filler masterbatch enhances the opacity of the film, giving it a more desirable, uniform appearance that is often required in packaging. This property is especially beneficial in retail packaging, where appearance plays a role in consumer perception.
2.4 Better Processability and Stability
Filler masterbatch can improve the processability of the polymer melt during blow film production. The presence of fillers allows for better stability and control over the film’s thickness, which is essential for uniformity in packaging applications. Moreover, the fillers can reduce shrinkage, a common issue in blow film production, resulting in consistent film dimensions.
2.5 Enhanced Thermal Properties
The addition of filler masterbatch improves the film’s thermal stability, allowing it to withstand higher temperatures during production and usage. This feature is crucial in applications where films are exposed to varying temperature conditions, such as agricultural or industrial films.
Explore more Filler Masterbatch Benefits in other applications
3. Applications of Filler Masterbatch for Blow Film
Filler masterbatch is widely used in various blow film applications due to its versatility and cost-effectiveness. Here are some of the common applications:
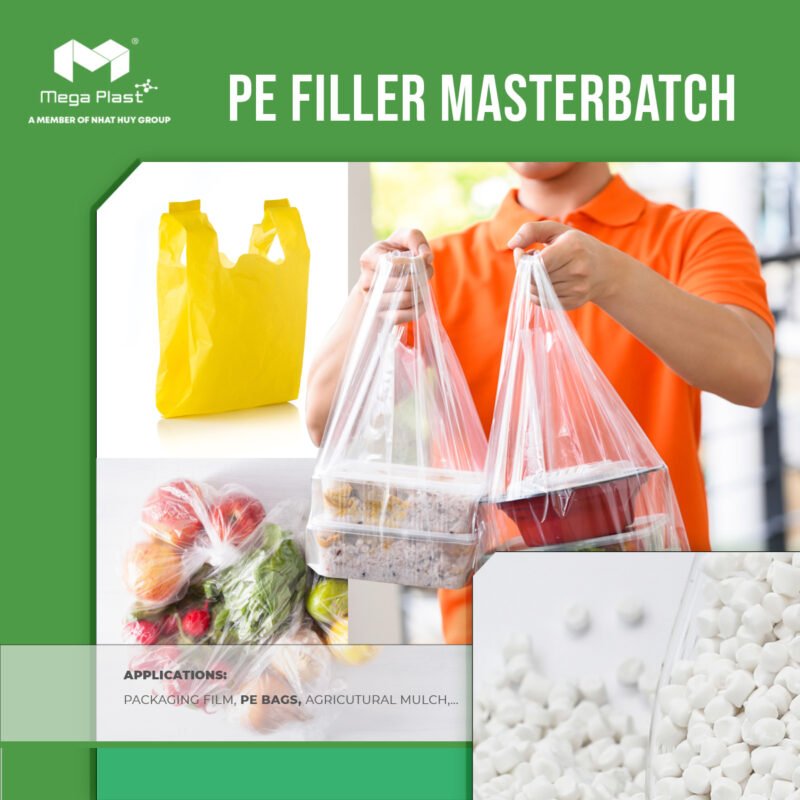
3.1 Packaging Films
In packaging, filler masterbatch enhances film strength and reduces material costs, making it ideal for producing retail bags, garbage bags, and industrial packaging films. The added durability and opacity provided by filler masterbatch meet consumer demands for quality while helping manufacturers achieve cost savings.
3.2 Agricultural Films
Blow films are extensively used in agriculture for mulch films, greenhouse covers, and silage bags. Filler masterbatch offers improved tear resistance and thermal stability, making it suitable for use in harsh outdoor environments. Its cost-effective nature is particularly advantageous for agricultural applications where large quantities of film are required.
3.3 Construction Films
Construction films, such as vapor barriers and protective covers, benefit from the strength and durability provided by filler masterbatch. These films are used to protect materials on construction sites and often require enhanced tear and puncture resistance, both of which are achieved by adding filler masterbatch.
3.4 Industrial Films
Industrial blow films used for pallet covers, shrink films, and heavy-duty liners require robust mechanical properties. Filler masterbatch reinforces the film’s structure, providing the necessary durability for these demanding applications.
3.5 Consumer Goods Packaging
Filler masterbatch is commonly used in the production of packaging films for consumer goods. With increased opacity and an improved appearance, these films are used to package products ranging from electronics to food items, ensuring that they remain visually appealing while offering protection.
4. Cost Savings Analysis of Filler Masterbatch in Blow Film Manufacturing
Using filler masterbatch in blow film manufacturing can result in substantial cost savings. Here’s how:
4.1 Reduced Polymer Usage
Substituting part of the virgin polymer with filler masterbatch can reduce overall material costs. Since filler materials like calcium carbonate are less expensive than base polymers, replacing even a small percentage of the polymer with filler masterbatch translates to considerable savings.
4.2 Lower Energy Consumption
Filler masterbatch can help lower the energy consumption required in the blow film process. The fillers modify the melt behavior, allowing for lower processing temperatures and reducing energy usage, which can be particularly advantageous in large-scale production facilities.
4.3 Waste Reduction
Increased film strength and stability reduce the likelihood of defects and product waste. By minimizing rejects and waste during production, manufacturers can save on raw material costs and reduce waste management expenses.
4.4 Enhanced Production Efficiency
Filler masterbatch improves the processability of the film, allowing for faster production speeds and reducing downtime caused by production issues. This efficiency leads to increased output, optimizing the manufacturing process and saving on labor costs.
4.5 Long-Term Cost Benefits
While the initial investment in quality filler masterbatch may be slightly higher, the long-term savings on material, energy, and production efficiency make it a cost-effective choice for blow film manufacturers. Additionally, the improved durability of the film reduces the likelihood of returns or product recalls due to defects, leading to further cost benefits.
5. Choosing the Right Filler Masterbatch for Blow Film Applications
When selecting a filler masterbatch for blow film, consider the following factors to ensure the best results:
- Compatibility with Base Polymer: Ensure that the filler masterbatch is compatible with the primary polymer (PE, PP, etc.) used in your blow film application.
- Filler Type and Quality: Choose high-quality fillers, such as finely ground calcium carbonate, for better dispersion and enhanced film properties.
- Filler Loading Ratio: Determine the optimal loading ratio of filler to polymer based on the specific requirements of your film application, balancing cost savings with desired performance characteristics.
- Supplier Reliability: Partner with reputable suppliers who provide consistent, high-quality filler masterbatch products to avoid fluctuations in film quality.
Read more about case study using Filler Masterbatch in Produce Plastic Bag
6. Filler Masterbatch for Blow Film Application
7. Conclusion: The Future of Filler Masterbatch in Blow Film Manufacturing
The use of filler masterbatch for blow film manufacturing offers manufacturers a versatile, cost-effective solution for producing high-quality, durable films across various industries. From packaging to agriculture, the benefits of filler masterbatch—including cost savings, enhanced durability, improved appearance, and increased thermal stability—make it an indispensable component in modern blow film production.
As industries continue to prioritize sustainability and efficiency, filler masterbatch will likely play an increasingly important role in reducing production costs and raw material usage. Manufacturers who adopt filler masterbatch in blow film production can expect not only improved product quality but also a competitive edge in a market that demands both affordability and performance.
Incorporating filler masterbatch for blow film is a smart, sustainable choice that drives down costs, enhances film properties, and contributes to more efficient and eco-friendly production practices.