Table of Contents
Injection molding is one of the most widely used plastic processing methods, requiring high precision, stability, and efficiency. Selecting the right filler masterbatch plays a crucial role in achieving these objectives while keeping costs under control. The correct choice can significantly enhance product quality, boost productivity, and improve profitability.
With over 21 years of expertise and a leading position in Vietnam’s filler masterbatch industry, Mega Plast proudly delivers optimized solutions for injection molding applications—trusted by customers in 60+ countries worldwide. This guide provides essential knowledge for R&D managers seeking perfect technical specifications and procurement specialists evaluating cost-effective solutions, ensuring an informed selection of the best filler masterbatch for injection molding.
Why Selecting the Right Filler Masterbatch for Injection Molding Is Crucial ?
Injection molding requires materials with excellent flowability under high pressure and temperature to quickly and evenly fill molds, followed by rapid solidification to shorten cycle times. When used correctly, filler can enhance these processing requirements. However, the wrong selection can cause numerous issues:
Reduced Flowability: An unsuitable filler may increase viscosity, making it harder for the plastic mixture to fill the mold properly. This can result in short shots or poor weld lines, affecting product integrity.
Compromised Mechanical Properties: The wrong filler can lower impact resistance, tensile strength, or elongation, failing to meet technical specifications.
Equipment Wear and Tear: Fillers with high hardness or poor dispersion can accelerate wear on screws, barrels, and molds, leading to higher maintenance costs and shorter equipment lifespan.
Surface Appearance Issues: Poor filler dispersion can cause white spots or streaks on the surface, impacting aesthetics and printability.
Increased Scrap Rate: All these problems contribute to higher defect rates, increasing waste and cutting into profits.
Thus, selecting the right filler masterbatch is not just about cost reduction—it is a strategic decision that directly affects product quality, manufacturing efficiency, and overall profitability
Key Considerations When Selecting Filler Masterbatch for Injection Molding
To make the optimal selection, manufacturers must evaluate core technical factors and the supplier’s capabilities:
+ MFI Compatibility
MFI (Melting Flow Index – MFI) is a critical parameter in injection molding, indicating the flowability of molten plastic under specific conditions. Filler Masterbatch itself does not possess an independent MFI like base resins, but when blended, it directly affects the overall melt flow behavior of the mixture. High-quality filler masterbatch is engineered for optimal MFI compatibility with commonly used resins such as PP, PE, ABS, ensuring that any MFI changes remain within predictable and acceptable limits. This stability in melt flow enables efficient mold filling, achieving perfect mold coverage while reducing processing strain on machinery.
Selecting a filler masterbatch with compatible MFI is non-negotiable for maintaining smooth injection molding operations, minimizing defects, and optimizing cycle times for high-quality, cost-effective production.
+ Core Technical Properties of Filler Masterbatch
Particle Size and Distribution of CaCO₃: Smaller, uniformly distributed particles increase surface area contact with the base resin, leading to better dispersion and improved mechanical properties.
Surface Treatment (Coating): CaCO₃ powder must undergo surface treatment with coupling agents to enhance compatibility with hydrophobic resins. This improves dispersion and strengthens mechanical performance, especially impact resistance.
Whiteness and Purity of Calcium Carbonate Powder: These factors affect the final product’s coloration, making them critical for bright-colored products or precise color matching.
Moisture Content: High moisture levels in filler masterbatch can cause voids, streaks, and defects on plastic surfaces, negatively impacting both appearance and mechanical integrity.
Dispersion in Base Resin: For optimal performance, fillers must fully and evenly disperse in the base resin during processing. Poor dispersion leads to localized weaknesses that affect mechanical properties and surface aesthetics.
Impact on Mechanical Properties: High-quality filler masterbatch can increase stiffness in plastic products while retaining desired attributes like flexural strength and Vicat softening temperature.
Discover Global Mineral
Suggested Filler Masterbatch Codes for Optimal Injection Molding from Mega Plast
Drawing from extensive industry experience, Mega Plast offers a range of optimized filler masterbatch solutions for injection molding, designed to provide cost efficiency while ensuring high-quality performance. Here are some of the most commonly recommended codes:
Code I202: A balanced filler ratio, optimizing cost vs. performance. Features a compatible melt flow index (MFI), helps increase stiffness, and enhances mold filling efficiency.
Code I262: A higher filler ratio with a special formulation, providing superior stiffness while maintaining MFI compatibility for smooth processing.
Code I261: A customizable variant with adjustable MFI and dispersion properties, tailored for specialized applications. Selection depends on the base resin, product requirements, and injection molding machine specifications.
Choosing between I202, I262, I261, or other codes from Mega Plast’s extensive catalog of 100+ filler masterbatch options depends on several key factors: base resin compatibility (PP, PE, ABS, etc.); final product requirements (desired stiffness, impact strength); injection molding machine characteristics
Selecting the right filler masterbatch is a strategic decision that drives cost optimization, production efficiency, and product quality. With over 21 years of expertise, advanced triple-screw extrusion technology, rigorous quality control, and a closed-loop supply chain, Mega Plast ensures the highest standards in filler masterbatch solutions.Trusted in 60+ countries, Mega Plast adheres to global export standards, reinforcing its position as Vietnam’s leading filler masterbatch manufacturer and a reliable global partner.
Let Mega Plast guide you in selecting the most optimized filler masterbatch solution for your injection molding needs. Contact our team of experts today for technical consultation and tailored recommendations, turning manufacturing challenges into profit-driving opportunities!
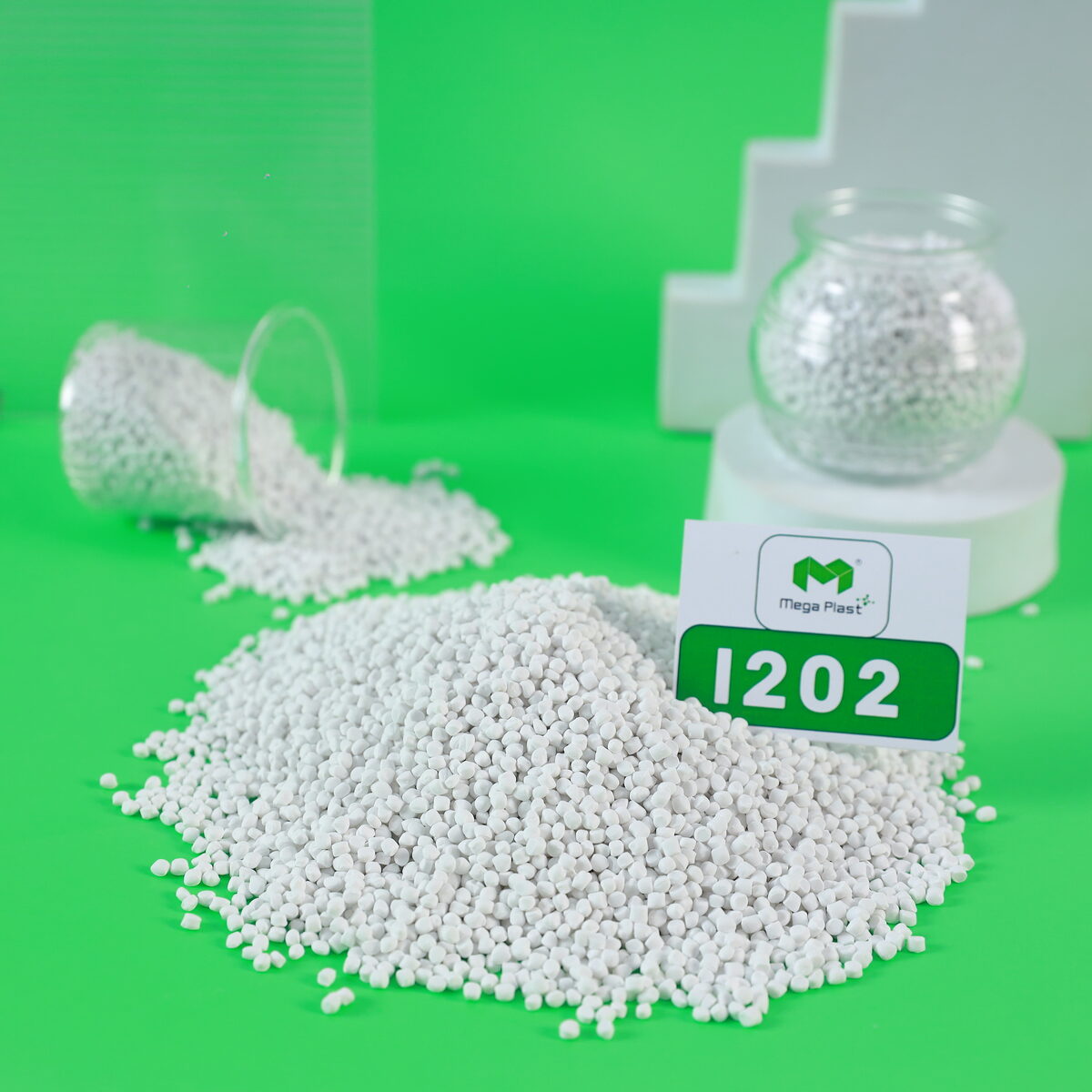
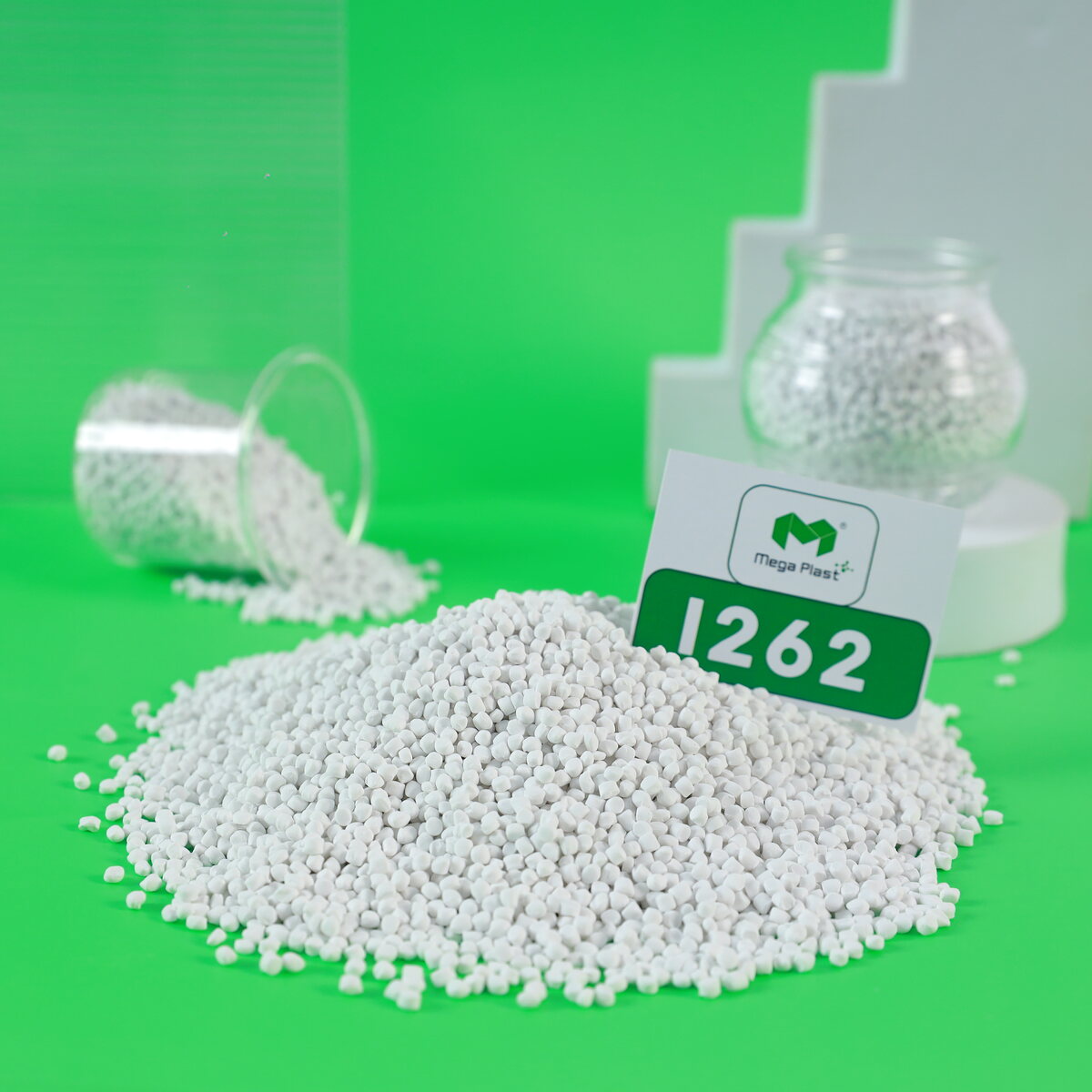
Discover more about: CaCO₃ Filler Masterbatch products