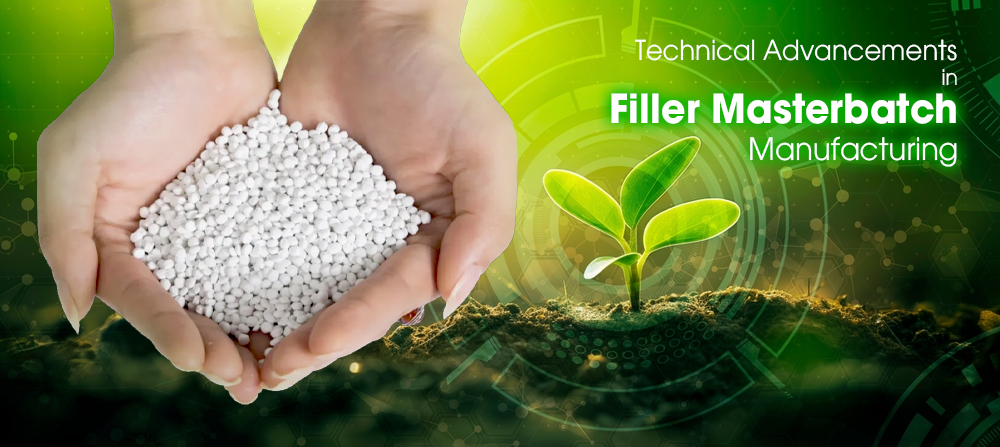
In the fast-paced world of plastics manufacturing, every granule, pellet, or speck of filler masterbatch represents not just a component in a material, but also a stepping stone to a more efficient, sustainable, and sophisticated production line.
Manufacturers across all sectors, from automotive to consumer electronics, are keenly aware that staying ahead of the curve in filler masterbatch technology is no longer a luxury but a strategic necessity.
This blog post dives deep into the world of filler masterbatch manufacturing.
Here you will learn about not just the basics of masterbatch production or its roles across different industries but also the groundbreaking technological advancements driving this industry forward.
We’ll explore innovative materials, sophisticated processing, smart manufacturing applications, and the profound implications of each on the broader manufacturing landscape, sector by sector.
Background on Filler Masterbatch
Before we can fully appreciate the cutting-edge advancements, it’s important to set the stage with an understanding of what filler masterbatch is and why it’s so pivotal.
In basic terms, a filler masterbatch is a concentrated mixture of additives and pigments in a carrier resin. It serves multiple purposes, primarily to impart color or specific functional characteristics to the base polymer in which it is dispersed. These masterbatches are widely used in manufacturing processes such as injection molding, blow molding, or extrusion and find applications across a wide range of industries.
Fillers, as the name suggests, essentially ‘fill’ the resin matrix, affecting properties like density, tensile strength, and heat resistance. They may be organic (wood fiber, rice husk) or inorganic (talc, glass beads) and can significantly impact performance and cost.
Common challenges in the manufacturing of filler masterbatch include achieving optimal dispersion of the fillers within the carrier resin, consistency in color or functional properties, and cost-effective production without compromising on quality.
Breakthrough Technologies in Manufacturing the Masterbatch
The recent surge in technological advancements within the filler masterbatch manufacturing sector has ushered in an era of precision, quality, and efficiency that was previously unattainable.
These innovations touch every aspect of the value chain, from material selection and compounding to distribution and end-of-line processes.
Cutting-Edge Mixing Arrangements
Modern mixers and compounding machines boast sophisticated designs that combine various principles of material agitation, melt flow, and heat transfer. Continuous mixer designs like the ZSK MEGAvolume PLUS from Coperion have led to more homogenous and consistent polymer melt blends, reducing production downtime and enhancing quality control.
Micro-Pelletization
Micro-pelletization is another key area of advancement, allowing for the formation of smaller, more uniform pellets. This translates into improved dispersion, reduced machine wear, and more stable production processes.
Energy-Efficient Extrusion
The latest generation of twin-screw extruders, driven by energy-efficient servo motors, significantly reduce energy consumption. Additionally, innovations such as the ‘mechanical torque limitation’ have made these extruders safer and dramatically diminished maintenance needs.
High-Throughput Compounding Lines
High-throughput compounding lines are capable of processing greater quantities of filler masterbatch with high precision. The scale and speed of these lines enable shorter processing times and larger batch sizes, resulting in economies of scale and a lower cost per unit of masterbatch produced.
Material Innovations
One of the most notable developments is the extensive research in filler materials. New types of fillers are being identified and their properties fine-tuned to match the stringent demands of modern manufacturing.
Nano-Fillers: A Nano Revolution
Nanotechnology has made its way into filler masterbatch manufacturing with the advent of nano-fillers—materials with particle sizes in the nanometer range. These nano-fillers offer unprecedented improvements in mechanical properties and surface finish when dispersed in plastics, albeit with special control requirements during processing.
Sustainable Fillers
The industry-wide push for sustainability has led to the exploration of natural and recycled fillers that can contribute to reducing the environmental impact of plastic products. Innovations like biocompatible fillers made from agricultural byproducts or post-consumer recycled fillers are gaining traction for their environmental benefits without compromising on performance.
Functional Fillers
The versatility of fillers has been expanded with the development of functional fillers. These fillers serve a dual-purpose by not only modifying the material’s physical properties but also making it ‘self-cleaning,’ ‘antibacterial,’ or ‘electrically conductive.’ This has unlocked novel applications in consumer goods, healthcare, and automotive industries, among others.
Process Enhancements
Dynamic advancements in the manufacturing process itself have led to tighter control over the quality, homogeneity, and efficiency of filler masterbatch production.
Advanced Blending Methods
New blending methods have emerged, leveraging technologies like melt mixing, which can yield a more uniform dispersion of the fillers. Furthermore, improvements in gravimetric feeding and proportioning systems ensure greater accuracy in the blend, resulting in a more consistent and predictable product.
Reactive Extrusion
Reactive extrusion involves the compounding of polymers with a chemical reaction. This advanced process can lead to enhanced polymer-filler interaction, resulting in higher-performance materials with customized properties that traditional mixing cannot achieve.
Intelligent Dosing Control
The incorporation of intelligent dosing systems in compounding lines allows for the precise adjustment of filler concentrations in real-time. These systems can automatically compensate for raw material variations, maintain set-point performance targets, and fine-tune feed rates according to dynamic processing conditions. Such levels of automation lead to a more stable and efficient production line.
Environmental Impact and Sustainability
Groundbreaking innovations in filler masterbatch manufacturing are not just about process improvements; they carry profound implications for sustainability and environmental responsibility.
Biodegradable Masterbatches
The development of biodegradable masterbatches that facilitate the degradation of plastics into harmless compounds has gained significant attention. These masterbatches offer a solution for applications where recyclability or biodegradability is a priority, such as in packaging or disposable products.
Energy-Efficient Processes
Many of the technological advancements in filler masterbatch production revolve around energy efficiency. From high-efficiency motors to innovative insulation and heat-exchange designs, manufacturers are reducing their carbon footprint while also cutting operational costs.
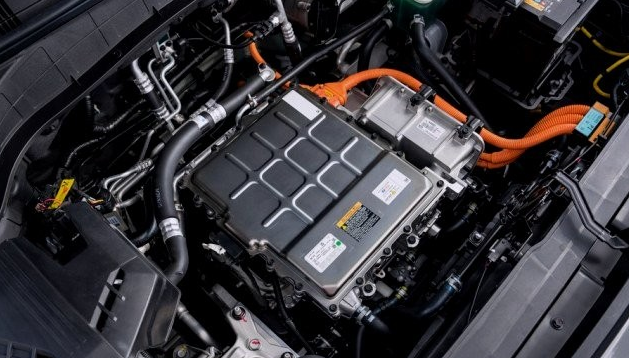
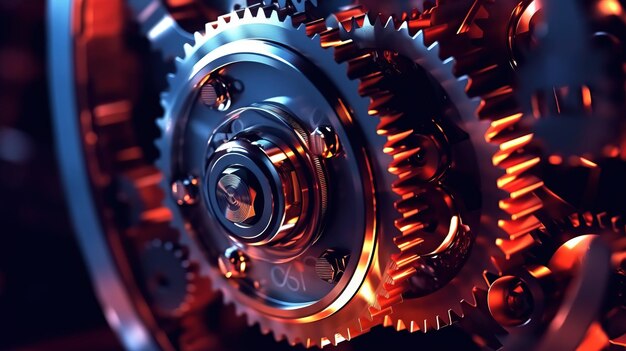
Closed-Loop Recycling
In some advanced setups, waste and surplus material are re-integrated into the manufacturing process, closing the loop and minimizing production waste. This circular economy approach is as economical as it is environmentally sound.
The Economic Implications in the masterbatch field
The impact of technology in filler masterbatch manufacturing goes beyond the factory floor. These advancements are shaping the competitive landscape and opening new avenues for growth.
Cost Reductions and Market Access
By lowering the cost of production and expanding product capabilities, technological innovations in filler masterbatch manufacturing are helping companies access new markets and drive growth. The ability to offer high-quality products with innovative properties at competitive prices can be a game-changer in an industry.
Strategic Partnerships
In the midst of these changes, strategic partnerships are becoming more common, as manufacturers seek to leverage complementary technologies and capabilities. Collaborations between material suppliers, machinery providers, and end-users are accelerating innovation and the adoption of new solutions.
Fostering Innovation Ecosystems
The industry’s rapid evolution is fostering new innovation ecosystems, with emerging players and startups disrupting traditional markets. These newcomers are bringing fresh perspectives, technologies, and business models that challenge industry norms and drive further innovation.
Continue your journey into the world of masterbatch by reading ‘The Economic Benefits of Using Filler Masterbatch’.Click here to read more and expand your understanding.
Case Studies: Success Stories and Real-World Applications
To enrich our understanding of how these advancements are catalyzing real change, it’s essential to examine actual case studies and their tangible impacts.
Automotive Interiors
In the automotive industry, advancements in filler masterbatch technology have allowed for the creation of piano-black finishes that are not only scratch-resistant but also provide a deep luster that rivals the finish of natural materials. Such advances have been instrumental in elevating the quality and perceived value of automotive interiors, with cost and environmental benefits being additional drivers.
Food Packaging
Filler masterbatch technologies have rapidly evolved to address the unique needs of the food packaging sector, ensuring the safety, shelf life, and quality of packaged goods. Additives that render packaging materials UV-resistant, oxygen-barrier, or antistatic have become commonplace, preserving food while allowing for attractive and informative packaging designs.
Electrical and Electronic Applications
In electrical and electronic applications, filler masterbatch serves as a crucial tool in the production of insulating materials with tailored functional properties. Recent advancements have led to materials with exceptional electrical resistance, flame retardancy, and heat dissipation capabilities, safeguarding high-tech equipment and promoting safety.
Future Outlook
The pace at which technology is advancing filler masterbatch manufacturing is extraordinary, promising an exciting future of enhanced materials, streamlined processes, and sustainable production solutions.
Predictions and Trends
Looking ahead, we anticipate even finer control over material properties, with dynamic and reactive materials becoming more prevalent. The interplay between materials, manufacturing processes, and post-processing treatments will open up new possibilities for advanced product features and functions.
Transformative Possibilities
The potential for filler masterbatch technology to reshape entire industries is immense. With advancements in smart manufacturing, we foresee a landscape where customized products are the norm, rather than the exception, tailored to meet specific end-user requirements and industry standards.
Market Dynamics and Competitiveness
The impact on market dynamics is already evident, with early adopters gaining a leading edge. Those who are quick to integrate the latest advancements will be better positioned to compete, offering products that are not only superior in performance but also aligned with the global sustainability agenda.
Conclusion
Technological advancements in filler masterbatch manufacturing represent much more than a series of mechanical and chemical feats. They embody the innovative spirit of an industry committed to progress, quality, and sustainability. For manufacturers, the message is clear: the future belongs to those who dare to advance, to learn, and to adapt.
By staying informed and engaged with the latest innovations, companies can position themselves at the forefront of progress. The quest for the ultimate filler masterbatch—a material that embodies all the qualities of the future—continues, and the industry is collectively taking steps to redefine manufacturing excellence.
Call to Action
We hope this detailed exploration of filler masterbatch advancements has inspired you to think critically about your role in the manufacturing ecosystem.
What are your experiences with these technologies?
What do you think the future holds for the filler masterbatch industry?
We encourage you to continue the conversation. Share your thoughts, experiences, and insights in the comments section below. The exchange of knowledge and ideas is essential if we are to collectively unlock the potential of filler masterbatch technology and drive the industry forward.
Whether you’re looking for a reliable supplier, interested in exploring our product range, or simply wish to learn more about our cutting-edge manufacturing processes, our team is ready to assist you. Contact us today to schedule a visit or consultation, and let’s explore how Megaplast can elevate your business to new heights. Your partnership in innovation starts here.