Table of Contents
Filler masterbatch in Injection molding is a process for making plastic objects. This process brings economic opportunities to the plastic industry and solves challenges for manufacturers to seek raw materials at the lowest cost while maintaining production.
This article explores how filler masterbatch in injection molding can reduce costs, optimize productivity, and maintain high quality.
Overview of Filler Masterbatch and Injection Molding
Injection molding is a process that involves injecting molten plastic into molds to produce complex and precision-shaped items. It’s commonly used in making automotive components, household items, and packaging. However, the cost of production can rise due to the high price of pure resin.
Filler masterbatch is a plastic additive, often containing calcium carbonate (CaCO₃) or other materials. When blended with resin, it reduces the need for pure resin, resulting in cost savings while maintaining the mechanical properties of the final product.
Filler Masterbatch in Injection Molding: to Reduce Cost and Improve Product Properties
Filler Masterbatch in Injection Molding: Reduce Raw Material Costs
Manufacturers can reduce raw material costs without sacrificing product quality by substituting a portion of pure resin with filler masterbatch. This helps achieve a lower cost per unit while maintaining product integrity.
Let’s see an example. Our customers in Egypt used 100% virgin resin for the plastic injection molding of washing machine casings, making it difficult to price them competitively in the market. Mega Plast introduced Filler Masterbatch I202H, tailored to the manufacturer’s needs, allowing them to reduce virgin resin usage without sacrificing quality. By incorporating Filler Masterbatch I202H, the manufacturer achieved a 10% reduction in production costs while maintaining product quality. The washing machine casings continued to meet durability standards, enabling the manufacturer to stay competitive.
Filler Masterbatch in Injection Molding: Improve Product Properties
In addition to cost savings, filler masterbatch can enhance the physical and chemical properties of the final plastic products, such as increased stiffness and heat resistance, making them more durable and suitable for various applications.
Filler masterbatch, especially those containing calcium carbonate (CaCO₃), increases the stiffness and rigidity of plastic products. This property benefits items that must withstand mechanical stress or heavy loads, such as large containers, automotive parts, or appliance casings. The enhanced stiffness also improves the product’s dimensional stability, preventing warping or deformation under pressure.
In some cases, filler masterbatches can enhance the impact resistance of plastic products. This is especially important for washing machine casings, which must endure mechanical shocks and stress. Filler materials help distribute impact forces more evenly, reducing the risk of cracking or breaking under pressure.
Application of Filler Masterbatch in Injection Molding
Filler masterbatch is widely used across a wide range of industries, from automotive components and electronics to household goods and packaging. As industries continuously seek to optimize costs while adhering to strict quality standards, filler masterbatch offers a practical solution in injection molding processes. By partially replacing virgin resin, manufacturers can reduce material costs without compromising their products’ strength, durability, or aesthetic properties, making it an essential additive for high-volume production environments.
In the automotive industry, filler masterbatch produces durable yet lightweight plastic parts, such as dashboards, interior panels, and bumpers, which maintain impact resistance, rigidity, and heat stability. This enables automotive manufacturers to achieve cost savings while ensuring the structural integrity and safety of their components. In the packaging industry, filler masterbatch reduces the overall weight of products, such as containers and bottles, without sacrificing critical mechanical properties like tensile strength and flexibility. This reduces production costs and supports sustainability initiatives by minimizing plastic usage and waste, making filler masterbatch an ideal choice for industries focused on efficiency and environmental responsibility.
Conclusion
Filler masterbatch effectively reduces injection mold costs while boosting productivity and maintaining high product quality. By incorporating filler masterbatch into manufacturing, businesses can save on raw materials, streamline production, and remain competitive.
If your business faces the high costs of plastic injection molding, Mega Plast offers a range of customized Filler Masterbatch solutions to help you optimize your production process and reduce costs.
Are you interested in learning how Mega Plast can help you reduce costs in plastic injection molding? Contact us today to explore tailored filler solutions that meet your manufacturing needs.
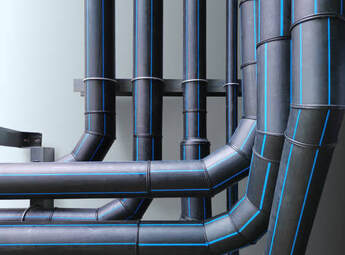