Film blowing process is a popular method in plastic production, especially for producing plastic bags and films used in packaging, agriculture, and many other industries. While efficient and cost-effective, this process presents certain challenges that, if unresolved, can impact product quality and production efficiency. Below are some of the most common problems encountered during film blowing and solutions to improve the process.
Table of Contents
1. Gel Formation in Film
- Problem: Gel formation appears as small, translucent spots on the film surface, resulting in uneven film quality. Gels can originate from impurities in the resin, degraded polymer, or inadequate melting.
- Solution: To prevent gel formation, use high-quality raw materials and ensure proper storage. Regularly clean the extruder to remove any residual materials that could degrade. Optimize the temperature settings to ensure complete melting without overheating.
2. Bubble Instability
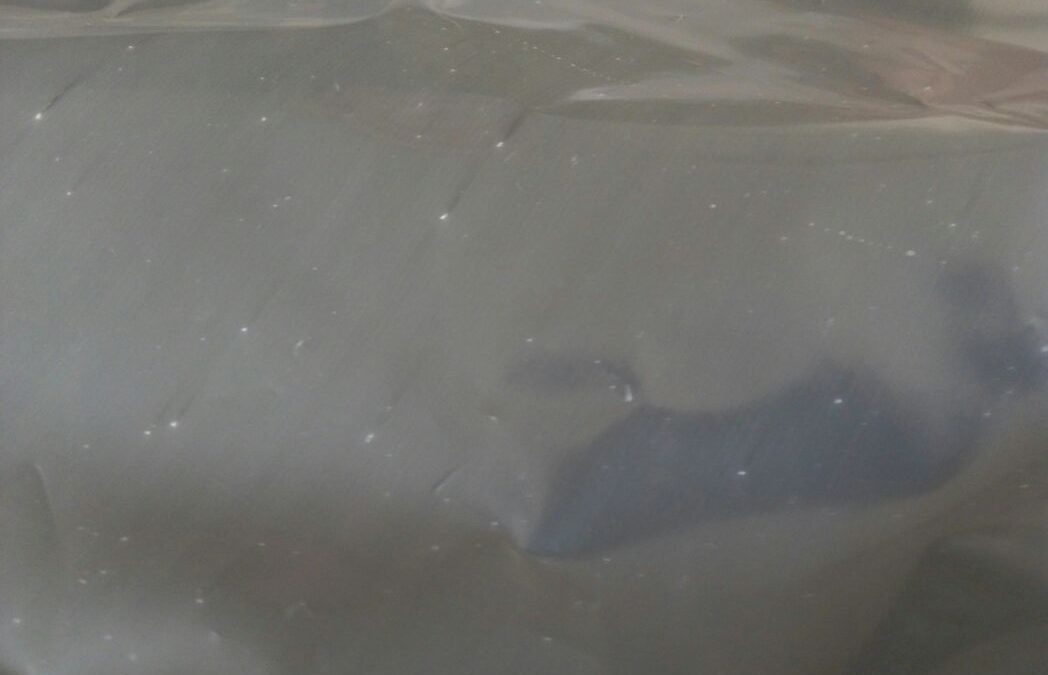
- Problem: During the film blowing process, the bubble can fluctuate, leading to inconsistent film thickness and quality. Causes include improper air flow, irregular resin feeding, and uneven temperature distribution.
- Solution: Adjust the air ring to stabilize airflow around the bubble. Ensure the resin feed is consistent by using quality resins and keeping the screw and barrel in good condition. Inspect and maintain the heating elements to ensure even temperature distribution.
3. Poor Film Clarity and Transparency
- Problem: Achieving high clarity and transparency is essential for many packaging films, but issues like haze and cloudiness can degrade appearance. This can result from impurities, improper cooling, or incorrect material choice.
- Solution: Use resins specifically designed for film clarity, and adjust the cooling rate by balancing the air ring and chiller settings. Regular maintenance of equipment helps to avoid contamination that affects film transparency.
4. Thickness Variation
- Problem: Thickness variation leads to inconsistent film quality, affecting product performance. It’s usually caused by fluctuations in extrusion speed, uneven cooling, or incorrect die gap settings.
- Solution: Regularly monitor and control extrusion speed. Inspect the die gap and adjust if necessary to ensure uniform thickness. Maintaining a consistent cooling rate is also essential, as uneven cooling can lead to thickness variation.
5. Wrinkles and Folds
- Problem: Wrinkles and folds in the film reduce its usability and strength. They often occur due to bubble instability, poor winding, or incorrect nip roll settings.
- Solution: To avoid wrinkles, ensure proper tension control and alignment between the nip rollers. Regularly check bubble stability and adjust nip rolls to eliminate wrinkles.
6. Low Film Strength
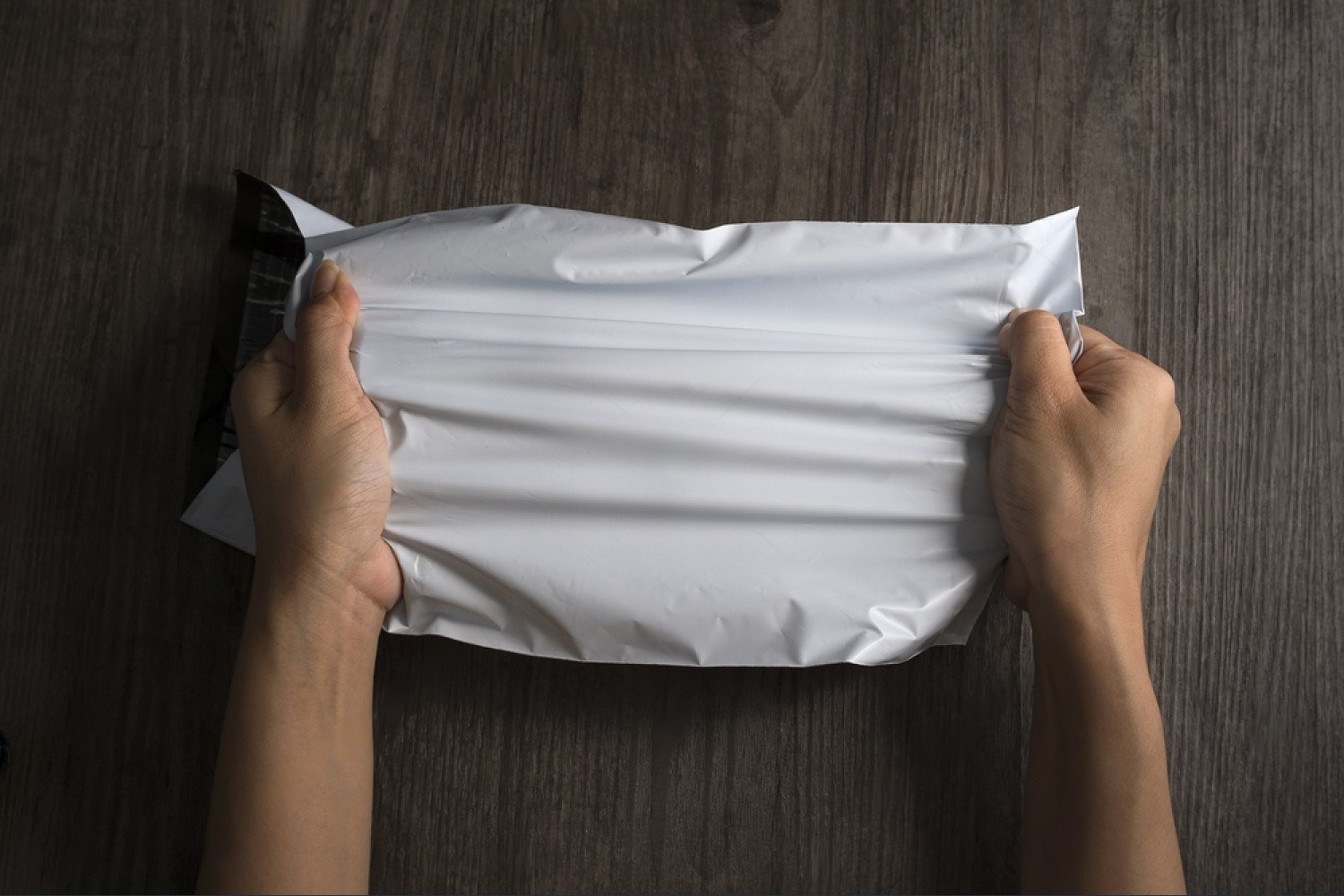
- Problem: Film strength is crucial, especially for heavy-duty applications. Low strength can result from inadequate polymer blending, improper stretching, or use of unsuitable additives.
- Solution: Use high-quality resins and additives designed to enhance strength. Optimize stretching during the cooling stage to achieve a stronger, more durable film.
7. Poor Adhesion Between Film Layers
- Problem: In multilayer film applications, poor adhesion can compromise the integrity and functionality of the product. This issue can arise due to incompatible resins or insufficient heat.
- Solution: Choose compatible resins and adjust processing temperatures to ensure effective bonding. Adding adhesion promoters or using coupling agents can further enhance interlayer adhesion.
8. Contamination and Black Spots
- Problem: Contaminants in the film, such as black spots, can come from dust, degraded material, or burnt resin, leading to a decrease in film quality.
- Solution: Implement rigorous cleaning and maintenance protocols. Ensure a clean working environment, and replace any worn-out parts that could cause degradation or burning of resin.
9. Film Blocking
- Problem: Blocking occurs when layers of film stick together, making them difficult to separate, which can be inconvenient for end-users.
- Solution: Add anti-blocking agents to the resin formulation and use proper cooling and winding techniques. Adjusting the air gap between layers during the winding process can also prevent blocking.
10. Blown Film Defects Due to Weather Conditions
- Problem: Temperature and humidity fluctuations in the surrounding environment can impact the quality of blown film.
- Solution: To mitigate the effects of weather changes, maintain a stable environment around the machinery by controlling indoor temperature and humidity levels. This helps ensure consistent film quality regardless of seasonal changes.
Sucess case study using filler masterbatch to sovle film blowing issues
Benefits of Using Filler Masterbatch in Film Blowing
- Cost Efficiency: By replacing a portion of the polymer with filler, costs are reduced without compromising essential film properties.
- Enhanced Strength and Durability: Filler masterbatch improves film strength and makes it more resistant to punctures and tears.
- Improved Processability: Filler masterbatch can enhance the film blowing process by stabilizing the melt flow and reducing common issues like thickness variation.
- Improved Film Appearance and Opacity: Filler masterbatch can enhances the opacity of the film, giving it a more desirable, uniform appearance that is often required in packaging
More benefits of Filler Masterbatch in Film Blowing
Conclusion
Filler masterbatch serves as a valuable addition to the film blowing process, helping to tackle common production challenges while providing a cost-effective solution. With careful selection and proper application, filler masterbatch enhances film quality, process stability, and economic efficiency, making it an ideal choice for manufacturers looking to optimize their film production.
Explore more 10 Powerful Filler Masterbatch Applications and Benefits Across Key Industries