Table of Contents
In today’s competitive manufacturing landscape, injection molding companies are constantly looking for ways to cut costs and increase efficiency without compromising product quality. One of the most effective solutions gaining popularity is the use of Filler Masterbatch. This article explores how Filler Masterbatch can help injection molding operations save on costs and improve productivity.
1. What is Filler Masterbatch as a Injection Molding Material?
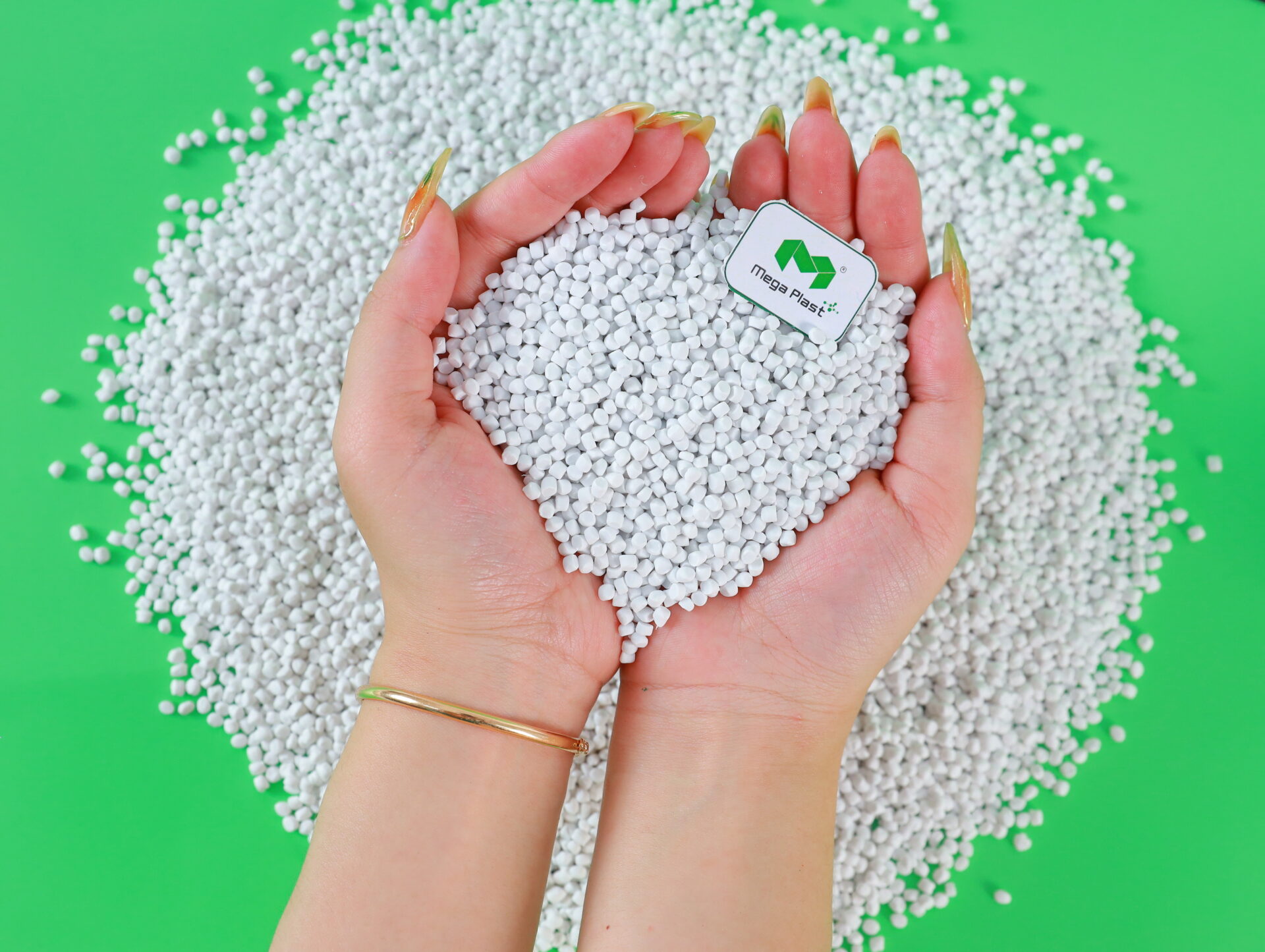
Filler Masterbatch is a game-changer in injection molding material for reducing costs and enhancing product properties in injection molding? Composed of fillers like Calcium Carbonate (CaCO3) or talc mixed with a polymer base, it helps manufacturers cut reliance on costly virgin resins while maintaining quality.
👉 Learn more about what Filler Masterbatch is and how it can transform your production process.
2. Benefits of Using Filler Masterbatch as a Injection Molding Material
2.1 Cost Savings
The primary advantage of Filler Masterbatch is its ability to reduce production costs. The price of filler materials like CaCO3 is significantly lower than that of raw polymers, so incorporating Filler Masterbatch into the injection molding process can lead to substantial savings, especially in large-scale production.
2.2 Enhanced Productivity
Filler Masterbatch can streamline the production process. Its composition allows it to melt faster during injection molding, reducing cycle times and allowing for quicker turnover. This increased efficiency directly contributes to enhanced productivity, helping manufacturers meet high demand while reducing machine wear.
2.3 Improved Product Strength and Durability
Adding Filler Masterbatch to the polymer mix can improve the rigidity and tensile strength of the final product. This makes it especially suitable for applications requiring sturdiness, such as automotive parts, consumer goods, and electronic casings.
2.4 Eco-friendly Option
Filler Masterbatch not only reduces reliance on virgin polymers but also aligns with sustainable production goals. By substituting raw materials with natural fillers, manufacturers can lower their carbon footprint and support eco-friendly manufacturing practices.
3. How Filler Masterbatch Works in Injection Molding Production
When used in injection molding, Filler Masterbatch is mixed with virgin resin before being processed in the molding machine. The filler material improves the flow of the resin, allowing for better mold filling and fewer defects. Additionally, it helps reduce the amount of shrinkage during cooling, resulting in more accurate product dimensions and a better surface finish.
Explore more Filler Masterbatch Benefits in other applications
Applications of Filler Masterbatch for Injection Molding
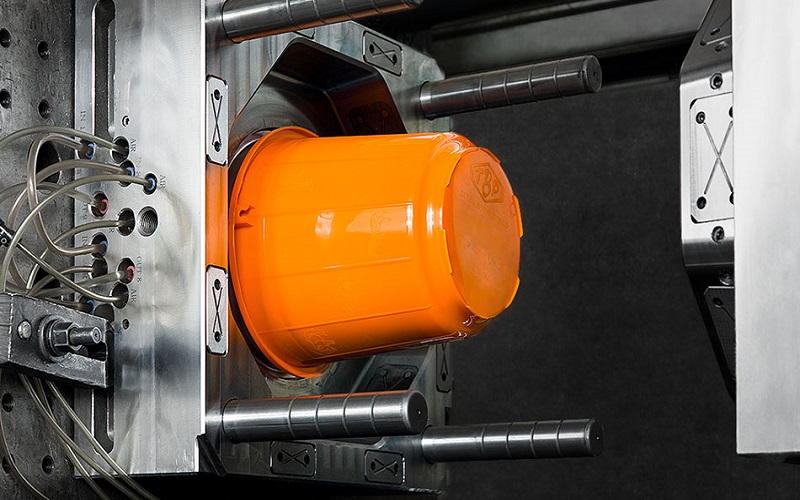
Filler Masterbatch is widely utilized in various injection molding applications to reduce costs, improve mechanical properties, and enhance productivity. Key applications include:
- Automotive Parts: In automotive manufacturing, Filler Masterbatch is used to produce components such as dashboards, interior panels, and under-the-hood parts. It enhances the rigidity and heat resistance of these components, ensuring durability while reducing material costs.
- Household Appliances: For household items like washing machine parts, vacuum cleaner components, and kitchen appliance casings, Filler Masterbatch helps achieve the desired strength and stability. By partially replacing raw polymers, it significantly reduces production costs.
- Consumer Goods: Filler Masterbatch is used in various consumer products, from plastic furniture and storage containers to toys and electronic casings. It improves impact resistance, dimensional stability, and cost-efficiency, making it ideal for high-demand consumer goods.
- Electrical Components: Injection-molded electrical components, such as cable conduits, switch boxes, and insulators, benefit from the added rigidity and durability provided by Filler Masterbatch. These properties are essential for products requiring consistent performance under varying environmental conditions.
4. Best Practices for Using Filler Masterbatch in Injection Molding
To maximize the benefits of Filler Masterbatch as a Injection Molding Material, consider the following best practices:
- Choose the Right Filler Content: Higher filler content can save costs but may affect the product’s flexibility. Finding the right balance is essential to maintain quality.
- Optimize Processing Parameters: Adjust temperature and pressure settings to suit the properties of Filler Masterbatch, ensuring smooth processing and consistent quality.
- Select the Appropriate Grade: Different applications require different filler compositions. For example, CaCO3 is suitable for standard products, while talc-based fillers may be better for applications requiring added stiffness.
- Filler Loading Ratio: The filler loading ratio should be carefully calibrated to ensure optimal results in blow film applications. A higher loading ratio helps reduce costs but may impact film transparency and flexibility. By adjusting the filler loading ratio according to specific product requirements, manufacturers can achieve the desired balance between cost-effectiveness and product performance.
Read more about case study using Filler Masterbatch in Injection Molding
5. Filler Masterbatch Grade for Injection Molding Application
6. Why Filler Masterbatch is the Future of Injection Molding
The use of Filler Masterbatch in injection molding material continues to rise due to its significant cost-saving potential and performance-enhancing properties. As more manufacturers prioritize sustainability and efficiency, Filler Masterbatch stands out as a practical, eco-friendly, and economically viable solution.
Conclusion
For injection molding companies looking to remain competitive, adopting Filler Masterbatch is an effective strategy to reduce costs and boost productivity. By following best practices and selecting the right filler mix, manufacturers can achieve optimal results without compromising quality. The use of Filler Masterbatch in injection molding is more than a trend—it’s a cost-effective innovation that offers long-term benefits to the industry.