Table of Contents
The Color Masterbatch is a game-changing aggregate that combines super constant pigments with resin in a uniform manner.
Also known as pigment preparation, this innovative polymer-colorant is composed of four essential elements: pigment or dye, carrier, dispersant, and additives. By harnessing the power of supernatural pigments or dyes attached to the resin, the Color Masterbatch achieves a higher coloring force compared to traditional pigments. Don’t miss the chance to experience the next level of vibrant and long-lasting colors with this remarkable pigment concentration.
Revealing the Secrets of Different Types of Color Masterbatch
Color masterbatch can be divided up into roughly the following types:
- Mono Batches or “Single Pigment Concentrates” (SPC): These masterbatches consist of a specific pigment with a supporting base. They may also contain wax and dispersing agents for better performance.
- Customized Masterbatches: These are tailor-made formulations that combine different powder pigments to create unique color solutions.
- Custom Coloring: This involves mixing different SPC granules to achieve the exact color desired by the customer.
Choose from these options to meet your specific color requirements.
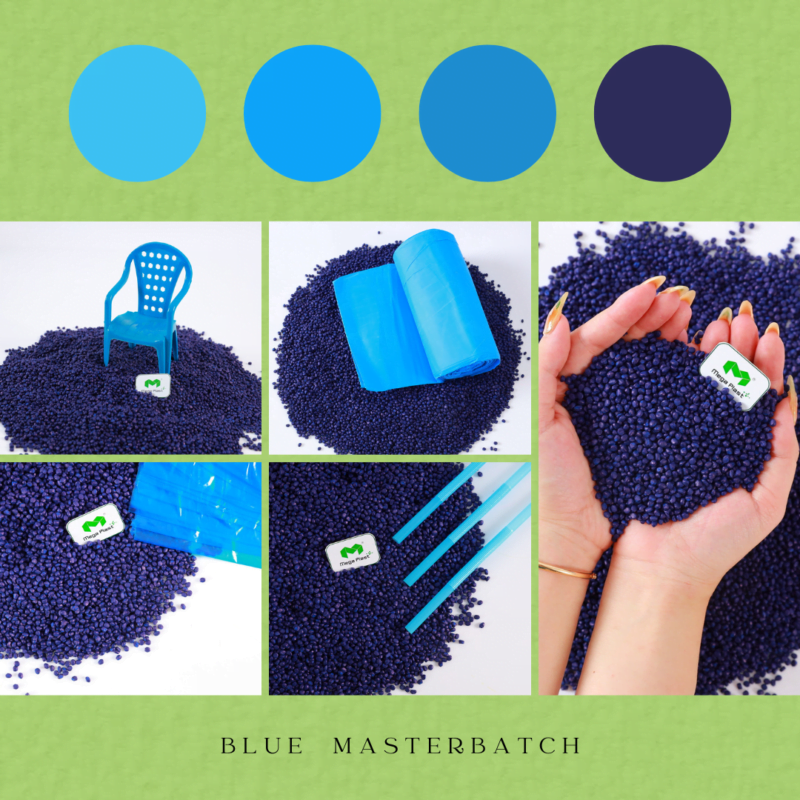
The 4-Step Formula to Color Masterbatch Manufacturing
✅ Pigment / Dye to produce Color Masterbatch
Discover a wide range of organic and inorganic pigments that promise exceptional color payoff and superior performance.
- Organic pigments: phthalocyanine red, phthalocyanine blue, phthalocyanine green, fast red, macromolecule red, macromolecule yellow, permanent solid yellow, permanent solid violet, azo red and so on.
- Inorganic pigments: cadmium red, cadmium yellow, titanium dioxide, carbon black, iron oxide red, iron oxide yellow and so on.
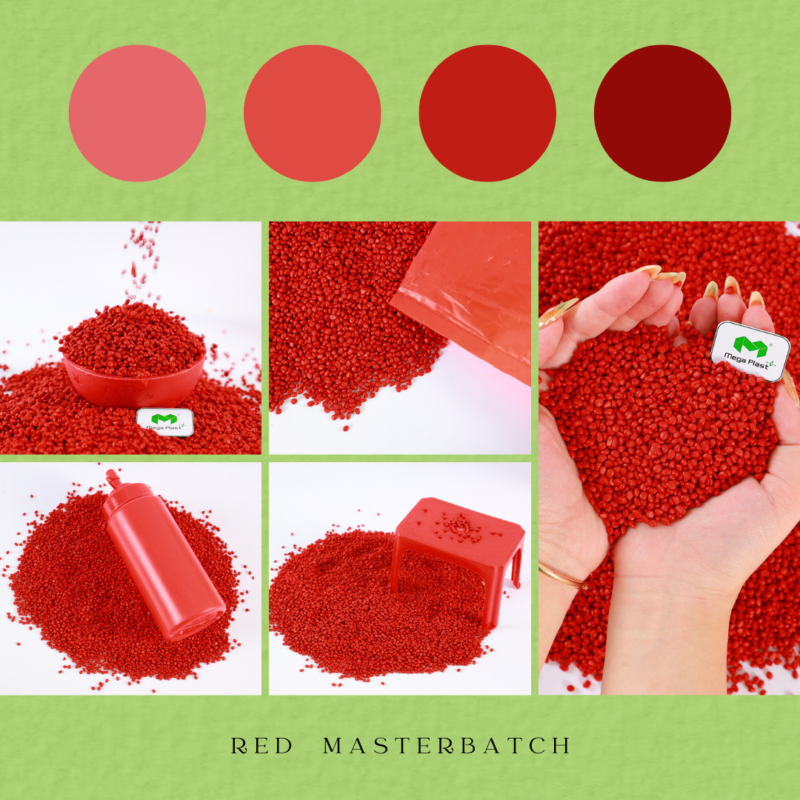
✅ Carrier Resin Plastic
Our range of special masterbatch includes carriers made from PE, PP, ABS, PVC, PET, EVA, and more. To ensure optimal performance, we recommend selecting a carrier resin that matches the product resin. This not only enhances compatibility but also improves fluidity.
✅ Dispersant
In order to achieve uniform dispersion of pigments and prevent them from clumping together, it is important to use a dispersant with a lower melting point than the resin. Additionally, the dispersant should have good compatibility with the resin and a strong affinity for the pigment. Some commonly used dispersants include polyethylene low molecular waxes and stearates.
✅ Additive
Unless specifically requested by the customer, our masterbatch does not typically include additives such as flame retardant, brightening, antibacterial, anti-static, and anti-oxidation.
To ensure consistent and vibrant coloring of plastic, it is crucial for the pigment particles to be finely refined and evenly dispersed throughout the plastic. The dispersion of the pigment not only impacts the visual appearance of the colored product, but also directly affects its quality, including strength, flexibility, durability, and electrical resistance.
- Optimal pigment size for a smooth surface is greater than 30 μm, avoiding spots and streaks.
- A matte finish is achieved with a particle size ranging from 10-30 microns.
- For regular product use, a particle size of less than 5 microns is recommended.
- When working with fiber (single wire diameter of 20-30 microns) and ultra-thin film (less than 10 microns), a pigment particle size of less than 1 micron is required.
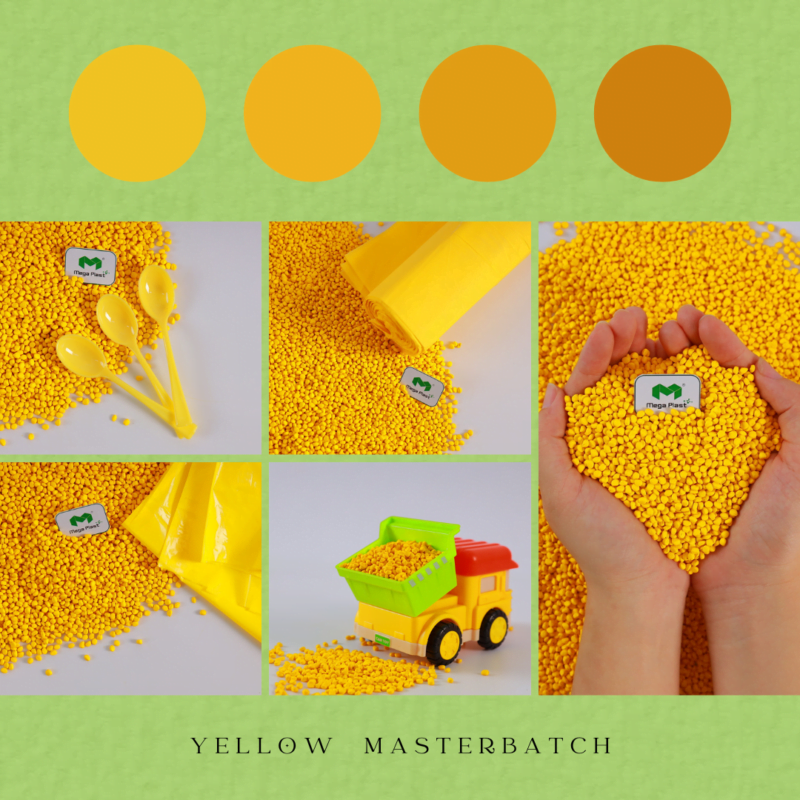
Why should choose color masterbatch from Mega Plast?
Mega Plast currently utilizes advanced high-speed mixing and twin-screw extrusion technology. This process involves combining various raw materials, including chromophoric resin, polyethylene wax, pigments, and additives, and feeding them into a high-speed mixer.
Within the mixer, the materials undergo high-speed mixing, resulting in the pre-crushing of coarse pigment particles and the even distribution of polyethylene wax with a low melting point. The high temperature produced during this process causes the resin particles to become plasticized and the polyethylene wax to adhere uniformly to their surface.
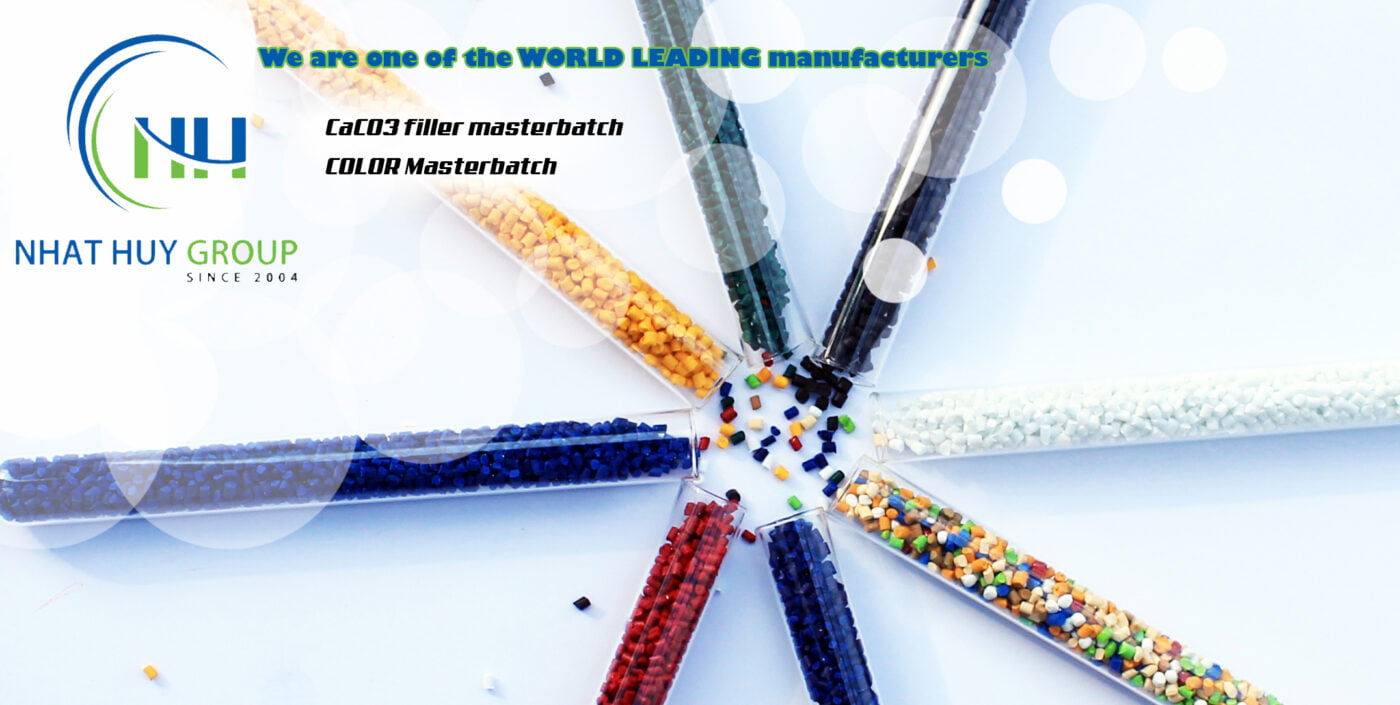
The mixture is then fed into a twin-screw extruder, where it undergoes further processing including melting, plasticization, mixing, and milling. Finally, the extruded material passes through a die to form a high-quality masterbatch product.
At Mega Plast, our customers always come first. We go the extra mile to provide the best experience possible. We offer samples, technical guidance, and consulting support so that businesses can make informed decisions. If you have any questions or need expert advice, don’t hesitate to contact us today!