Table of Contents
In the world of non woven fabric production, filler masterbatch has emerged as a game-changer, offering manufacturers an efficient way to reduce costs, enhance product properties, and meet the ever-growing demands of various industries. This guide delves into everything you need to know about filler masterbatch for non woven applications, covering its benefits, applications, and the latest industry trends.
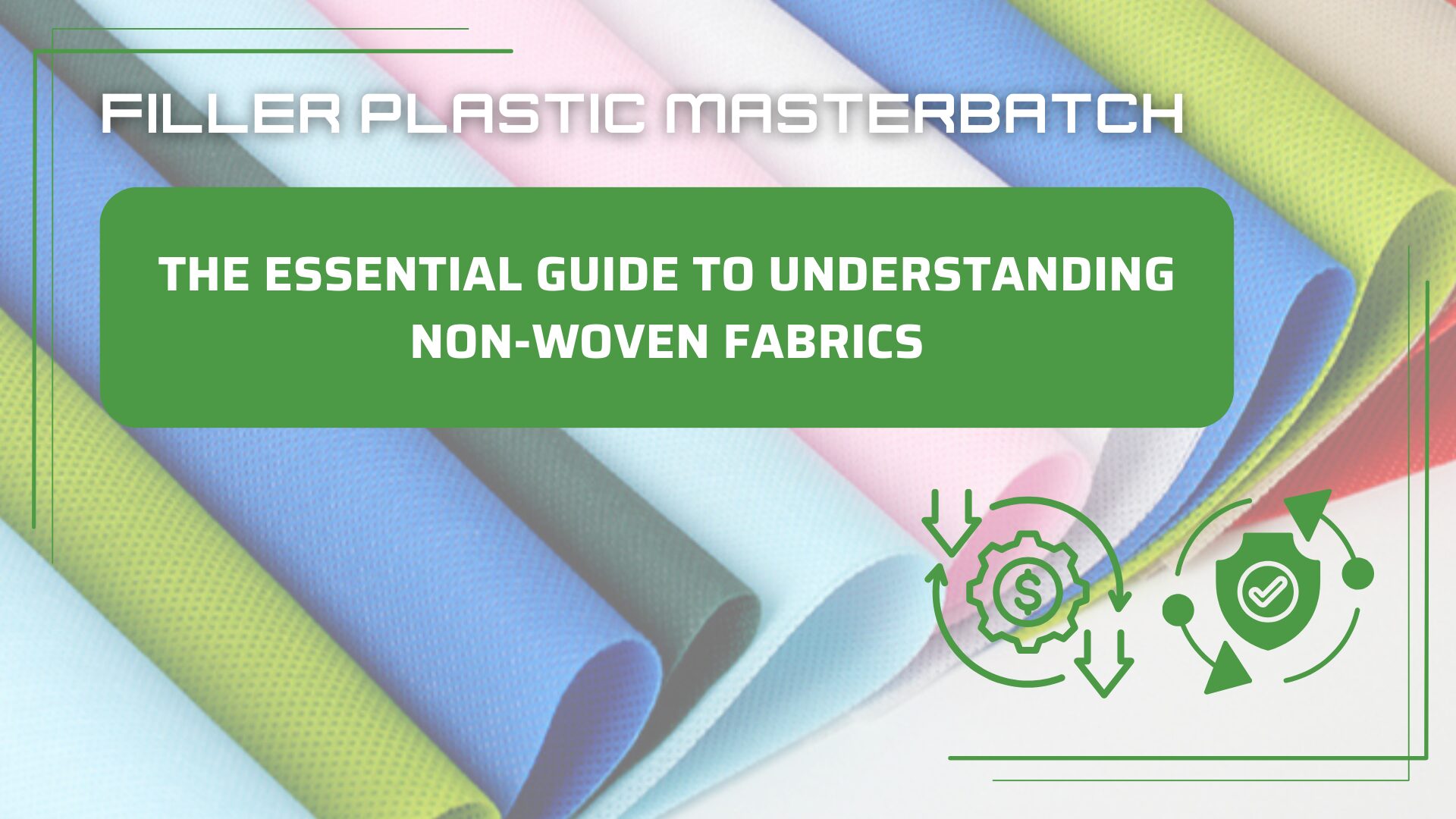
What is Filler Masterbatch?
Did you know Filler Masterbatch, a concentrated mix of fillers like calcium carbonate (CaCO3) or talc combined with a polymer base, is a game-changer in injection molding?
By replacing a portion of virgin resins with Filler Masterbatch, manufacturers not only reduce costs but also enhance product properties.
👉 Learn more about what Filler Masterbatch is and how it can transform your production
Key Benefits of Filler Masterbatch for Non Woven Fabric
- Cost Efficiency: The primary advantage of using filler masterbatch is cost reduction. By substituting a portion of the polymer with filler, manufacturers can lower production costs while maintaining fabric quality, which is essential for high-volume, cost-sensitive industries.
- Enhanced Mechanical Properties: Filler masterbatch improves tensile strength, rigidity, and durability in non woven fabrics, making them suitable for applications that require added toughness and resilience.
- Improved Fabric Weight and Thickness: Adding filler masterbatch can help control the weight and thickness of non woven fabrics, ensuring consistency across production batches, which is crucial for industries that demand precise specifications.
- Eco-Friendly Advantages: By replacing a percentage of the synthetic polymer with natural minerals, filler masterbatch reduces the environmental impact of production, aligning with global sustainability goals.
- Better Processability: Filler masterbatch enhances the overall processing performance by improving flow properties, reducing shrinkage, and stabilizing the extrusion process.
Applications of Filler Masterbatch in Non Woven Fabric
Filler masterbatch is highly versatile and supports various applications in the non woven industry. Below are some key sectors where it plays an essential role:
- Medical and Hygiene Products
- Non woven fabrics used in medical applications, such as surgical gowns, masks, and wipes, benefit from the enhanced durability and stability filler masterbatch provides. Its cost-effectiveness makes it an ideal choice for disposable items.
- Agricultural Applications
- In agriculture, non woven fabrics are widely used for crop covers, weed control mats, and soil stabilization fabrics. Filler masterbatch contributes to these products’ UV resistance and durability, ensuring longer product life under outdoor conditions.
- Automotive Interiors
- Filler masterbatch enhances the rigidity and aesthetic qualities of non woven materials used in automotive interiors. These include headliners, insulation, and trunk liners, where both cost efficiency and material strength are essential.
- Construction and Civil Engineering
- Non woven geotextiles, commonly used in construction for soil stabilization, drainage, and filtration, benefit from the added strength and durability filler masterbatch provides. It ensures that these fabrics maintain structural integrity in demanding conditions.
- Home and Furniture Products
- Non woven fabrics used in home furnishings, such as mattress covers, upholstery, and carpet backings, benefit from filler masterbatch, which improves their thickness, feel, and resilience.
Industry Trends in Filler Masterbatch for Non Woven Applications
The demand for non woven fabrics is continually growing, driven by industries such as healthcare, agriculture, and construction. Here are some key trends shaping the use of filler masterbatch in non woven applications:
- Sustainable and Eco-Friendly Solutions
- There is a global shift toward sustainability, and the use of natural mineral-based filler masterbatch supports eco-friendly initiatives by reducing the dependency on virgin polymers. Many manufacturers are focusing on recyclable and biodegradable options to meet green standards.
- Advanced Additives for Improved Performance
- The non woven industry increasingly uses filler masterbatch combined with advanced additives, such as UV stabilizers, anti-static agents, and flame retardants, to enhance the material’s functionality and durability in specific applications.
- Increasing Demand in Emerging Markets
- The rapid industrialization in Asia, Africa, and South America is boosting the demand for non woven fabrics in various sectors. As a result, filler masterbatch is gaining traction as an economical and efficient option for producers in these regions.
- Integration with Automation and AI in Production
- To meet high-volume demand, non woven fabric manufacturers are adopting automated production processes. Filler masterbatch aids in stabilizing these processes, ensuring consistent quality in large-scale operations.
- Customized Filler Solutions
- Manufacturers are increasingly opting for customized filler masterbatch solutions tailored to specific applications. This trend allows for optimized performance, particularly for non woven fabrics with unique requirements.
Filler Masterbatch: Top 10 Powerful Applications and Benefits Across Key Industries
Choosing the Right Filler Masterbatch for Non Woven Fabric
Selecting the right filler masterbatch for non woven fabric applications depends on various factors, including the desired material properties, application requirements, and production process. Here are some considerations to keep in mind:
- Material Compatibility: Ensure that the filler masterbatch is compatible with the primary polymer, such as polypropylene (PP) or polyethylene (PE), commonly used in non woven fabric production.
- Particle Size: Choose a filler masterbatch with an appropriate particle size to ensure even dispersion within the polymer matrix, resulting in better material properties.
- Additive Requirements: Consider filler masterbatch products that include additional additives like UV stabilizers or flame retardants if your non woven fabrics require enhanced functionality.
- Cost-Performance Balance: Evaluate the cost-performance ratio of the filler masterbatch to ensure optimal production costs without compromising quality.
Case Study: The secret to Reducing 20% of Non Woven Bag Production Costs
Filler Masterbatch for Non Woven Application
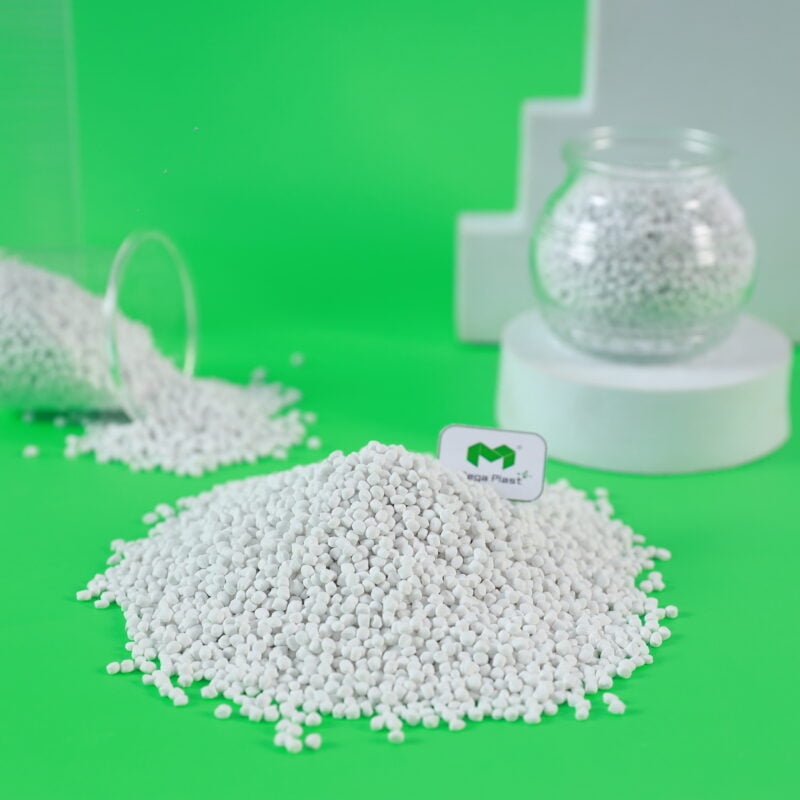
PP Filler Masterbatch for PP Non Woven – N202
- High dosage rate: up to 50% for GSM>50
- Good tensile strength
- No Dropping problem
Conclusion
Filler masterbatch plays a pivotal role in the non woven fabric industry, offering numerous advantages from cost savings to enhanced product performance. As the demand for non woven fabrics continues to grow, so does the importance of efficient, sustainable solutions like filler masterbatch. By understanding its benefits, applications, and industry trends, manufacturers can make informed decisions to stay competitive in the ever-evolving market.
Whether you’re looking to improve material strength, reduce production costs, or meet sustainability goals, filler masterbatch provides a flexible and economical solution for high-quality non woven fabric production.