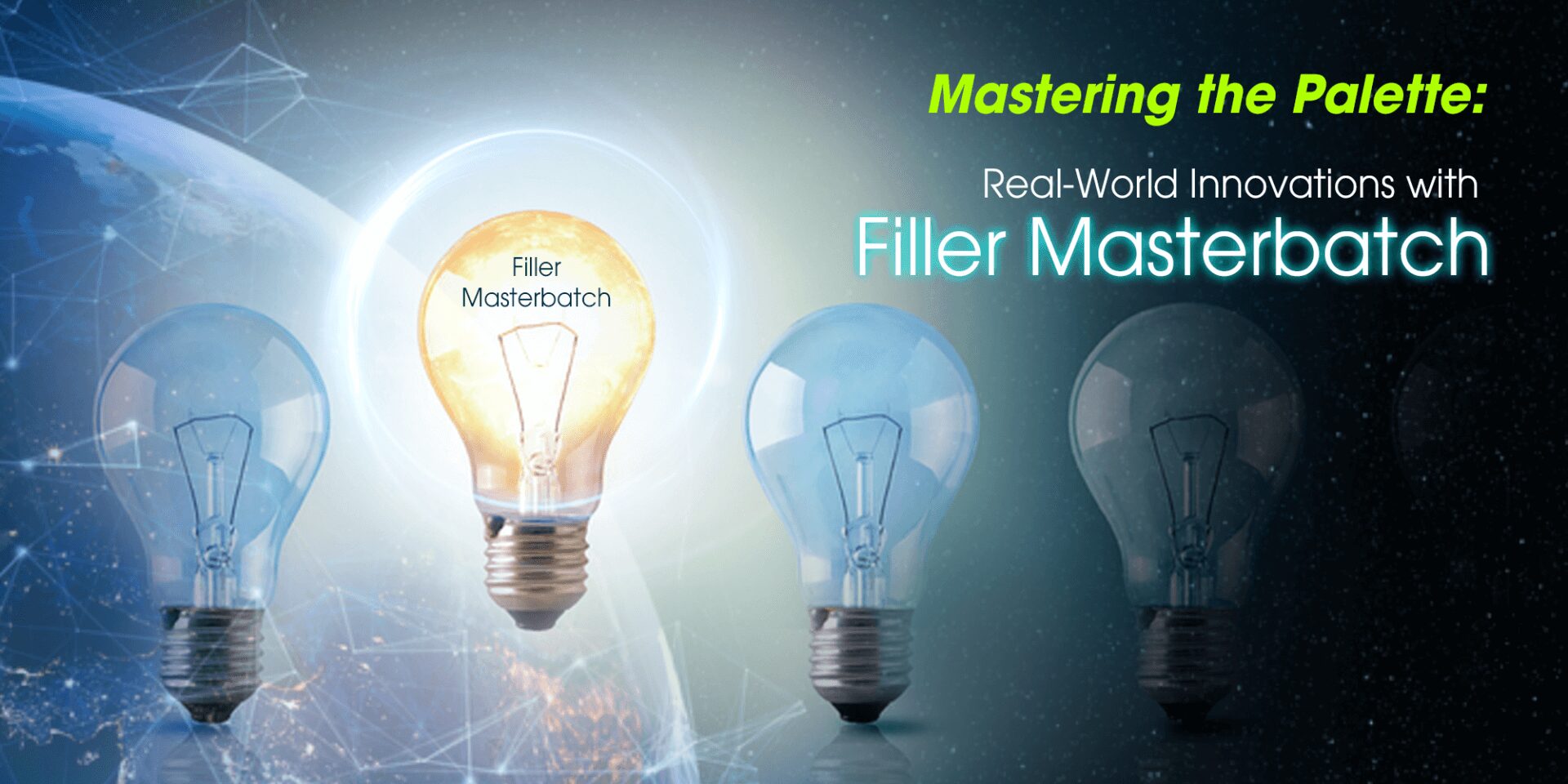
In the colorful world of plastics and polymers, the subtler, yet vital, components can often be overshadowed by the shine and structural glamor of the finished product. While the concept of masterbatches has long been an unsung hero in the plastics industry, it’s high time we give the lesser-known, filler masterbatch a spotlight. Within these pages, we will elaborate on the uses and implications of this silent partner, providing an in-depth exploration of how it has revolutionized various manufacturing processes and ultimately, the products they yield.
Understanding the Masterbatch
Before plunging into the detailed stories of application, it’s paramount that we clear the fog around the term ‘masterbatch’. For the uninitiated, a masterbatch is a concentrated mixture of pigments, dyes, or additives encapsulated during a heat process into a carrier resin that’s cooled and cut into granules. This blend is later added to raw polymer material during the molding or extrusion processes, adding color or imparting unique properties. One such category of masterbatch, the ‘filler masterbatch’, incorporates a filler, typically of calcium carbonate, talc, or some other mineral, to enhance properties like stiffness, impact resistance, or anti-blocking in films.
The Birth of Filler Masterbatch
The dawn of the 21st century brought forth an age of sustainable development and meticulous resource management. This zeal for eco-consciousness and economic sensibility laid the foundation for the advent of filler masterbatches. Raw polymers were often costlier and not always ideal for certain applications without modifications. The idea of using cheaper fillers to add bulk and tailor properties emerged as an ingenious solution. Fast forward to today, the once modest filler masterbatch has evolved into an indispensable element, brimming with applications that cater to the diverse needs of various industries.
Product Development in Plastics Manufacturing
Product development in the plastics industry is an intricate dance between the artistic touch of fulfilling design aesthetics and the scientific precision required to produce aid in performance enhancement. Filler masterbatch contributes to this alchemy in several ways, and the subsequent sections will lift the veil on its versatility through the lenses of different manufacturing processes and end-product sectors.
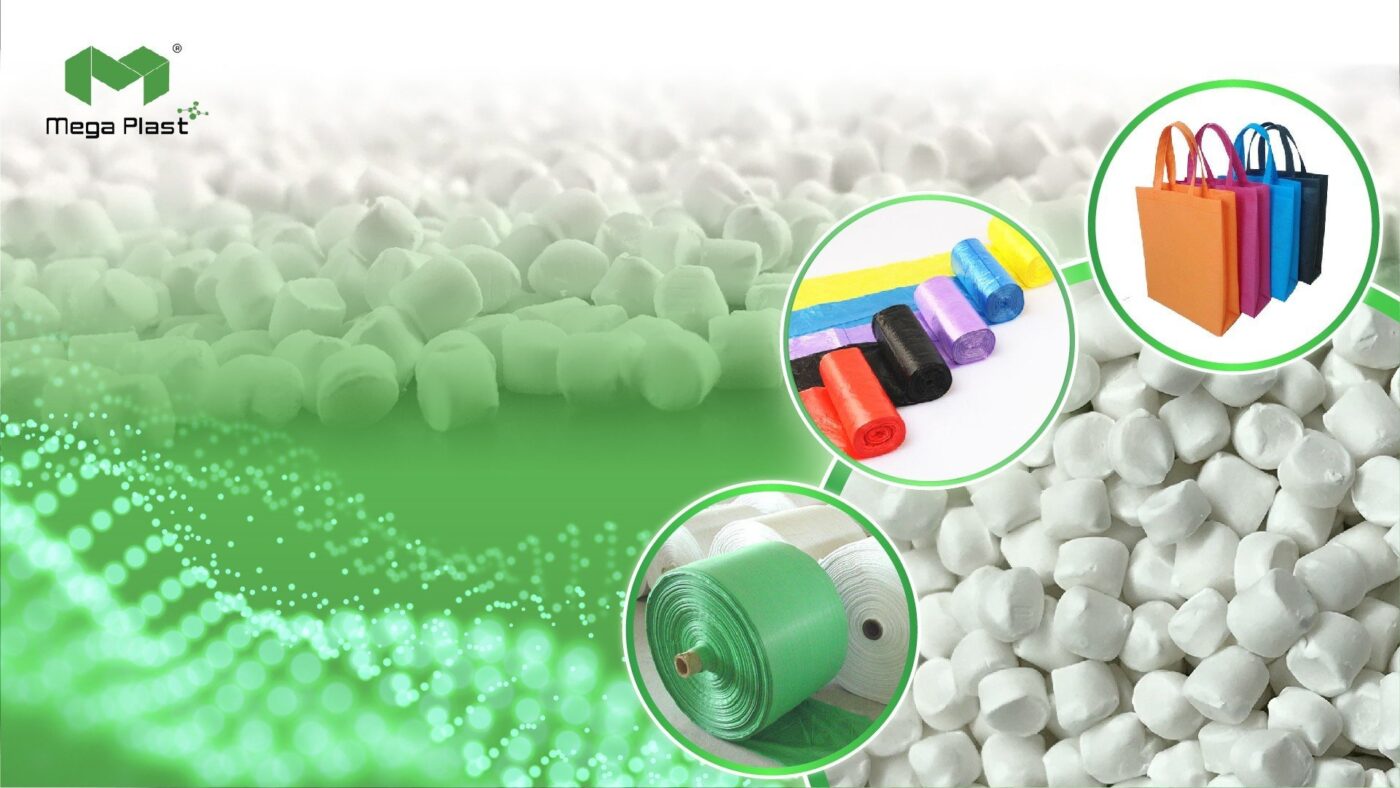
Injection Molding Transformations
Injection molding stands firm as a versatile manufacturing process. By injecting molten material into a mold under high pressure, intricate shapes can be replicated on a massive scale. Filler masterbatches have become a valuable ally in this arena, playing a pivotal role in delivering structural integrity, reducing warpage, and offering a cost-effective solution to components that do not require specific high-grade polymers.
Elevating Automotive Components
The automotive industry has a demand for components that are tough, durable, and lightweight. Filler masterbatches pave the way for these qualities, reinforcing ABS and polypropylene for use in bumpers, interior panels, and a range of structural elements. By introducing calcium carbonate fillers, the specific gravity of the plastic component is increased, leading to a weight reduction when compared to solid polymers, without sacrificing strength.
Optimizing Electrical and Electronic Devices
Precision is paramount in electronic devices, and even a micron’s deviation can lead to malfunction. Filler masterbatches can add that extra layer of accuracy and reliability, especially when used with high-temperature engineering plastics. The right mix can facilitate the dispersion of conductive fillers in the matrix, fine-tuning the electrical and thermal properties of the final product.
Blow Molding for Today’s Bottles and Tomorrow’s Future
The technique of blow molding sculpts plastic into hollow forms—a process well known in manufacturing bottles, containers, and potential ‘blue ocean’ products. Here, filler masterbatch finds its calling in modifying the physical properties of the bottles, such as improving the oxygen barrier for PET soda bottles or enhancing UV resistance for containers used in the agricultural, chemical, or pharmaceutical industries.
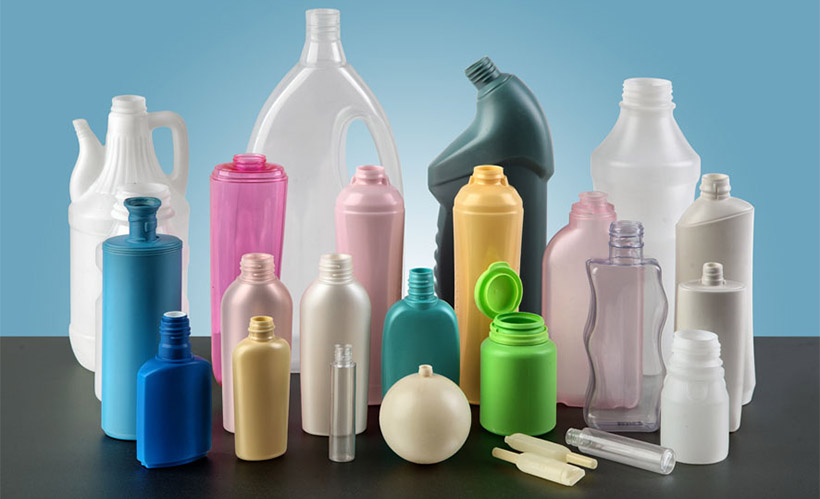
A Colorful Journey in Consumer Packaging
The psychology of color in marketing is a well-researched field, and consumer packaging often focuses on colors that evoke brand recognition, product differentiation, or communicate functionality. Filler masterbatches, designed for a rainbow of hues, ensure consistent color throughout the packaging material, without compromising the core traits of the polymer, like mechanical strength or light-blocking properties.
Reinventing the Wheel (and Barrels)
In industrial packaging, where load-bearing capability and longevity come at a premium, high-density polyethylene (HDPE) is a preferred material. Filler masterbatch reinforces the molecular structure of HDPE, significantly enhancing its capacity and shaping it into heavy-duty barrels that can weather time and transport.
Weaving Stories in Synthetic Fibers
The fashion industry is the modern-day playground for synthetic fibers, and filler masterbatch is the unseen artist behind their vibrant hues and specialized functionalities. The production of these fibers often involves the extrusion process, and filler masterbatch plays a role in maintaining the integrity of the materials, preventing bursting or sagging, and ensuring the colorfastness of the fibers.
Adding Texture to the Fabric of Our Lives
Fiber end products like rugs, carpets, and upholstery demand textural variety, stiffness, and resistance to atmospheric stresses. When mineral fillers are added to the polyethylene terephthalate (PET) fibers, a luxurious texture can be achieved alongside stronger resistance to pilling and static. This not only delights consumers but also reinforces the materials against everyday wear and tear.
Protecting Crops with Agricultural Films
Stretch films and silage bags protect crops, mitigate spoilage, and optimize storage. Filler masterbatch makes these films tougher, more opaque, and resistant to tearing, contributing to an extended shelf-life of the harvest. With the right fillers, the films can also be tailored to have anti-fogging properties, promoting visibility through humid conditions, essential for greenhouses and agriculture storage facilities.
The Digital Canvas of Consumer Electronics
Whether it’s the sleek monoliths of personal electronics or the robust casings of home appliances, the precision of plastics in the domain of consumer electronics cannot be overstated. Filler masterbatch here steps in to cut ounces from the weight, add tensile strength to protect intricate internals, and even shield the exposed plastics from UV degradation and fingerprints.
The Color Codes of Connectivity
In an era where devices have become extensions of self, the chromatic identity embedded in their casings speaks volumes. Filler masterbatch assists in formulating custom colors that align with the brand language, ensuring the hue remains intact over the life of the product, and that it does not interfere with the wireless signals or the functionality of sensors that might be layered beneath.
Harmonizing with Household Harmony
From the milk jug in the refrigerator to the laundry basket by the machine, household items demand durability and resilience in the face of daily chores and chores. Filler masterbatch imparts these qualities to the polymers, often reducing the carbon footprint and manufacturing costs while enhancing the product’s aesthetics and lifespan.
Diving into the Manufacturing Mix
For all of its magnificence, the glass slipper must fit perfectly, and that’s where the manufacturing mix comes into play. The intricacies of blending, extrusion, and molding processes are as much an art as they are a science. This section offers a profound understanding of how the ratio and the raw combination of elements lead to masterbatch magic.
The Alchemy of Manufacturing Process
The manufacturing process itself is an amalgamation of insightful steps, where precision is key. The method, whether compounding or continuous blending, significantly influences the dispersion and effectiveness of the filler masterbatch. Additives like coupling agents can be introduced, which bond the filler to the polymeric matrix, ensuring a stronger, more uniform blend with superior performance.
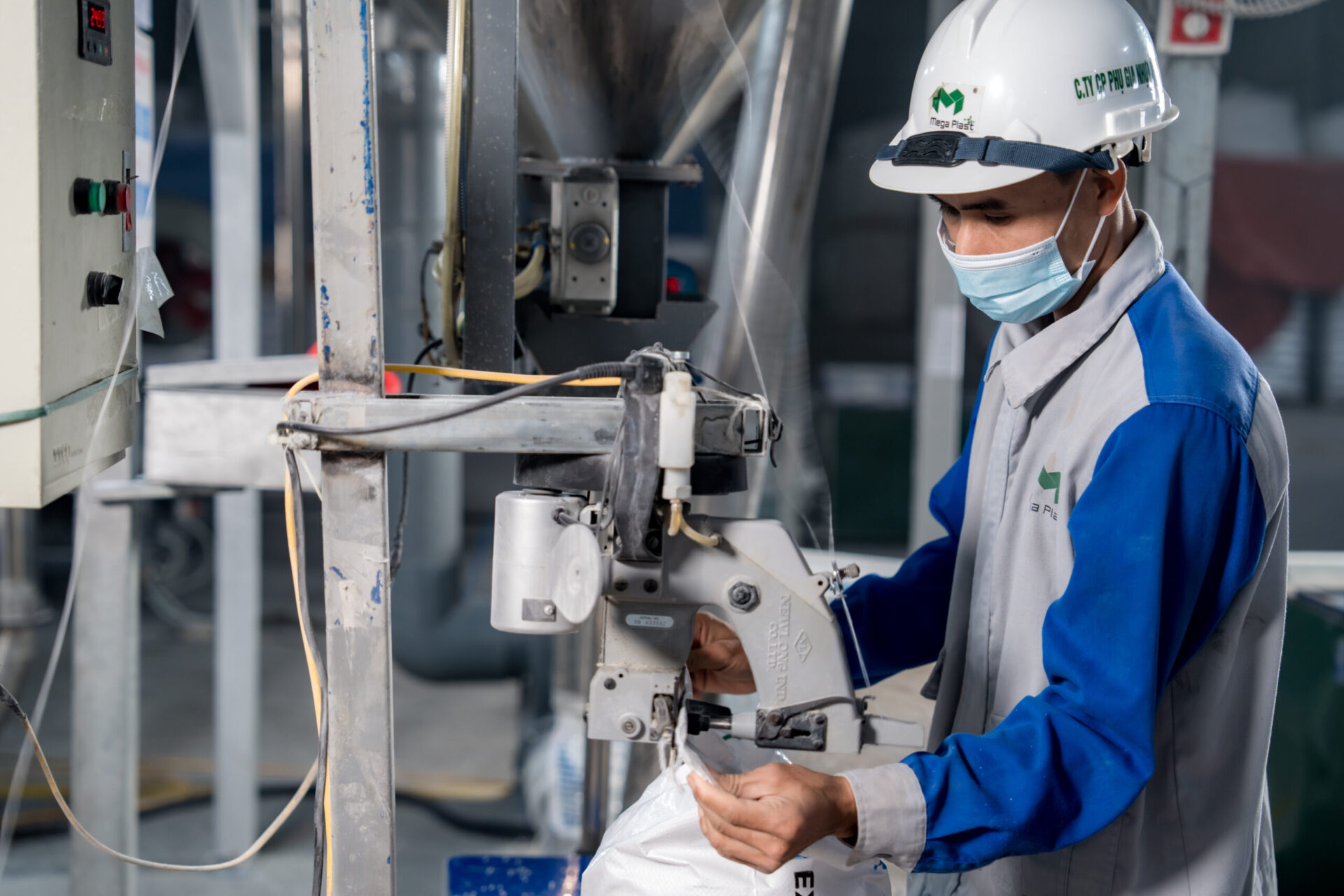
The Cardinal Role of Carrier Polymer
The choice of carrier polymer, be it PE, PP, or PS, is not arbitrary. It must be compatible with the raw material used in the subsequent processing, and its properties must align with the desired final product attributes. Additionally, it’s essential to consider the long-term characteristics, especially for applications subjected to external environmental or mechanical stressors.
Continue your journey into the world of masterbatch by reading ‘The Alchemy of Manufacturing Process – Types of Polymeric Matrices of Filler masterbatch’.Click here to read more and expand your understanding
Sustainability and Green Initiatives
In an age where the vision of sustainability stands amid an environmental and economic tumult, filler masterbatch becomes increasingly relevant. Scalable use of fillers like calcium carbonate serves to reduce the weight of plastics, thereby cutting material costs and CO2emissions due to transportation. This section details the sustainable spin-offs of filler masterbatch, from lightweighting to recycling.
Meeting the Green Benchmarks
Regulatory and societal pressures have pushed manufacturers to greener pastures. Filler masterbatch aids in energy conservation by allowing for lower processing temperatures or reduced cycle times, aligning with energy-efficient molding practices. Furthermore, they contribute to improving the recyclability potential of plastics, a crucial aspect in the current global climate crisis.
The Recycling Revolution
The concept of a circular economy is not just a utopian idea; it’s increasingly a necessity. Filler masterbatch applied to recycled polymers ensures that these materials can compete against virgin resin, both functionally and aesthetically. This encourages the use of recyclates without compromising the quality of the final product, paving the path for a sustainable future.
The Manufacturer’s Guide to Mastering Masterbatches
Manufacturer, beware! The right path is often the hardest to tread, and in the world of masterbatches, there are pitfalls aplenty. This segment provides insights and best practices for manufacturers to wield the power of filler masterbatch effectively, ensuring that it adds value without unintended consequences.
Initial Research and Formulation
Knowledge is power, and eureka moments are rare without curiosity. Invest in thorough research and understand the specifics of your polymer, processing, and end-use conditions before formulating the masterbatch. Even a découpaged portion of fillers can tilt the balance, so getting it right in the lab is as crucial as nailing it on the floor.
Partnering with Masterbatch Manufacturers
The collaboration between the masterbatch manufacturer and the end-user is a symbiotic relationship. The former offers expertise in compounding and comprehension of the subtle interplay between fillers and polymers, while the latter sheds light on the exact customer requirements and the environmental stresses the product may face. A harmonious partnership can yield masterbatches customized to perfection.
Quality Assurance and Control
The potency of a filler masterbatch can be its undoing if included in the process without proper quality checks. Set stringent quality standards for incoming raw materials, ensure batch-to-batch consistency, and validate the dispersion of fillers in the carrier. Regular audits and feedback loops ensure that the masterbatch performs consistently in the real world as it did in controlled conditions.
Real-world Success Stories
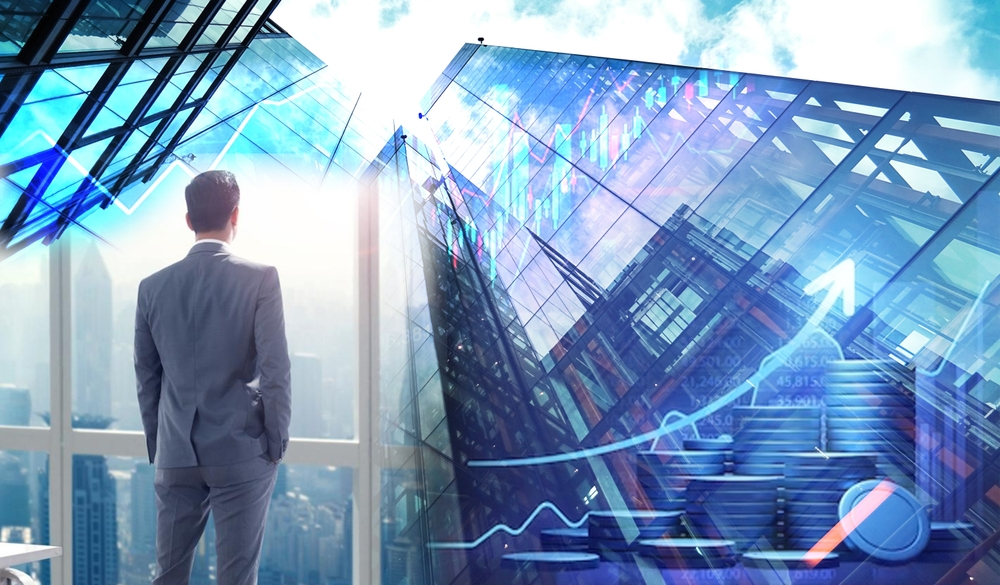
In this section, we pivot from theory to practice, bringing you real-world examples of manufacturers who leveraged filler masterbatch to enhance their products. From the rice paddies of Southeast Asia to the fashion runways of Milan, masterbatch has a diverse array of applications that speak to its versatility and ubiquity – and we’ve got the stories to back it up. So, buckle your seatbelts and get ready for a masterclass on mastering with masterbatches.
Case Study 1: Mastering Agricultural Mulch Films
In Thailand, farmers grappled with low crop productivity due to infertile soil. Enter Polyplast Asia – a manufacturer that introduced an innovative mulching film solution made using filler masterbatch. By incorporating calcium carbonate in the masterbatch, they created a product with superior tensile strength and thermal properties while being lightweight and cost-effective. This allowed farmers to increase their yield by 30% without increasing their costs.
Case Study 2: Mastering the Art of Fashion
In the fast-paced world of fashion, Danish designer Henrik Vibskov embraced filler masterbatch to revolutionize his creations. By incorporating recycled plastic in his designs and experimenting with different colors, he created truly unique collections that spoke to sustainability and creativity. His work has been showcased at major fashion weeks and exhibitions worldwide, proving that masterbatches have a place beyond traditional manufacturing industries.
Case Study 3: Start connecting to Africa
Nylon bags used to be a common item in Kenya. However, due to environmental concerns, the government has banned the use of nylon bags. In response to market demand, ECO LAB Limited has introduced non-woven bags. These environmentally friendly products are not only aesthetically pleasing but also reusable. Importantly, incorporating filler masterbatch as a production material has enabled the company to achieve optimal cost-effectiveness, making it suitable for the Kenyan market.
Conclusion
In conclusion, filler masterbatch is the unsung hero of the plastic industry, adding value and sustainability to products in ways that go beyond the surface. With its ability to enhance performance, reduce costs, and promote recycling, it’s no wonder that masterbatches are becoming increasingly popular. Manufacturers who leverage the power of masterbatches effectively will undoubtedly see a competitive edge in the market, allowing them to thrive in an ever-evolving industry.
We encourage you to continue the conversation. Share your thoughts, experiences, and insights in the comments section below. The exchange of knowledge and ideas is essential if we are to collectively unlock the potential of filler masterbatch technology and drive the industry forward.
Whether you’re looking for a reliable supplier, interested in exploring our product range, or simply wish to learn more about our cutting-edge manufacturing processes, our team is ready to assist you. Contact us today to schedule a visit or consultation, and let’s explore how Megaplast can elevate your business to new heights. Your partnership in innovation starts here.
Pingback: Filler Masterbatch: The Unsung Hero of Plastics Shaping Our Tomorrow