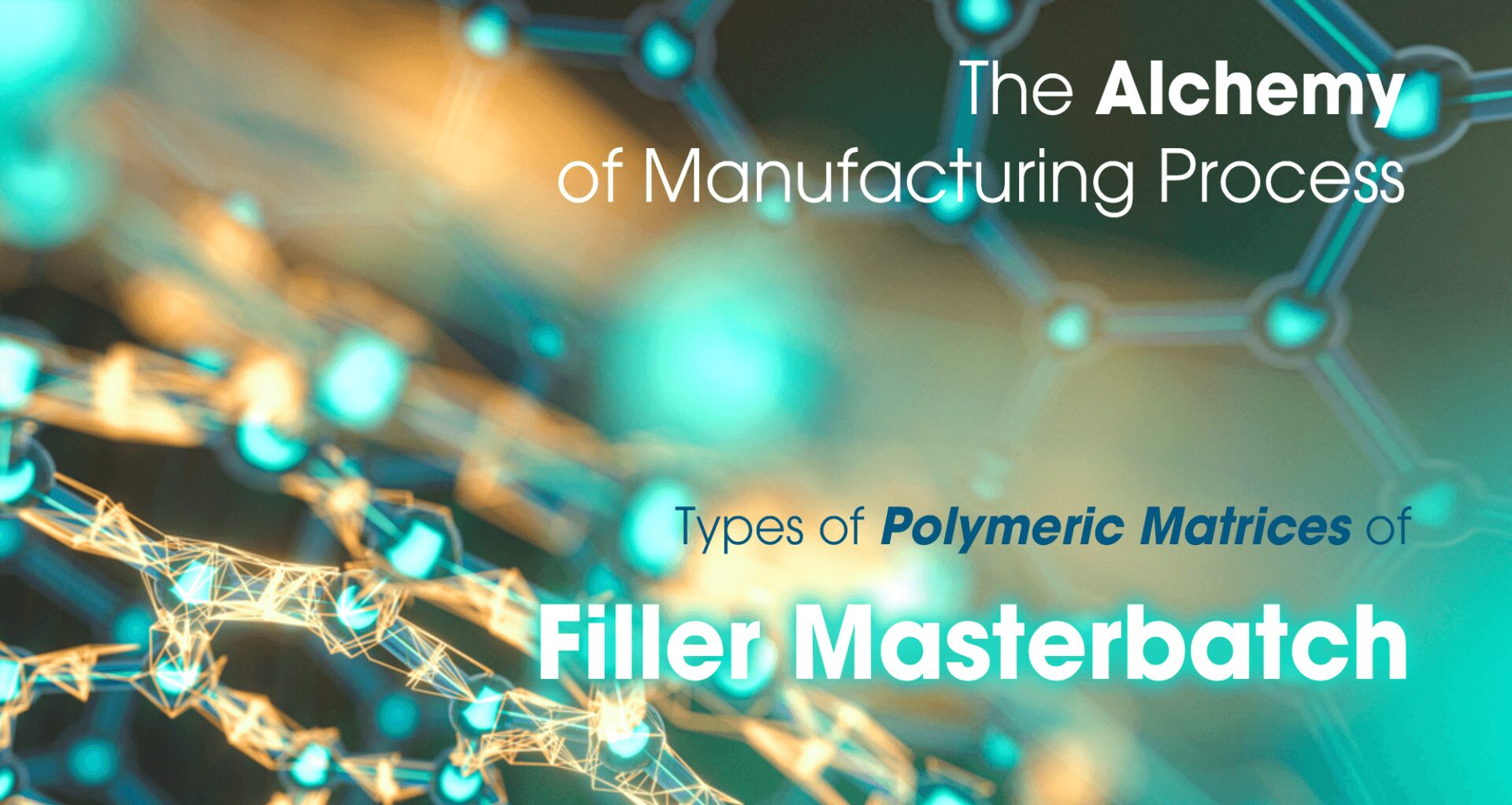
Modern manufacturing is akin to an alchemy of sorts—a meticulous blend of science and art, turning base materials into valuable products. At the heart of this alchemy lie the polymeric matrices, the very crucibles in which the magic of plastic transformation occurs. For manufacturers employing techniques like injection molding, blow molding, extrusion, and more, understanding these matrices is not just beneficial—it’s elemental.
From automotive parts to household items and from food packaging to synthetic fibers for textiles, an in-depth understanding of polymeric matrices can steer manufacturers toward better products, more streamlined processes, and enhanced competitiveness. In this extensive exploration, we will unpack the significance and applications of polymeric matrices across various manufacturing paths, plunging deep into the nuances and intricacies of this impalpable yet indispensable element.
Polymeric Matrices Unveiled
The Essence of a Masterbatch
Diving into the manufacturing process, particularly in the realm of plastics, one often encounters the term ‘masterbatch.’ This single word encapsulates an entire world of possibilities and intricacies, and is the linchpin around which the manufacturing of plastic components revolves.
Masterbatches are concentrated additives in the form of pelletized, liquid or powder. They’re used to alter the properties of the base plastics and improve their performance or aesthetics. Usually, masterbatches contain pigments, anti-oxidants, UV stabilizers, flame retardants, and other additive components, fused within a polymer matrix.
What Composes a Masterbatch?
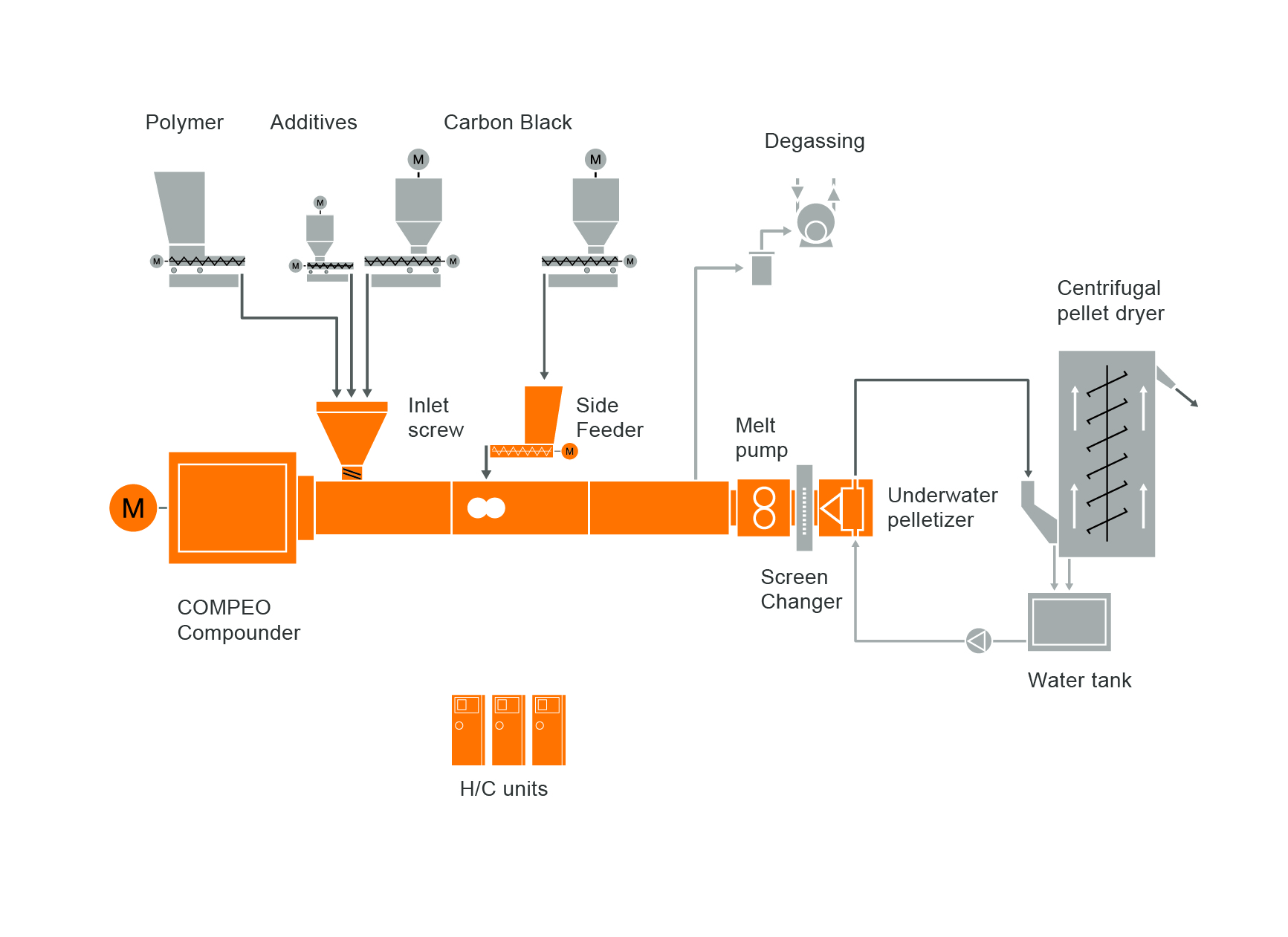
In order to comprehend how masterbatches fit into the picture, we must understand their components. Consider a simplified hierarchy:
Carrier Resin: This is the structural foundation of the masterbatch, a polymer in its own right. Often, this is the same material as the base resin into which the masterbatch will be incorporated, ensuring it’s compatibility.
Active Ingredient: Ranging from colors to performance additives like anti-stats, these components deliver the primary functionality that the masterbatch is designed for.
Additive Protectants: Essentially, the guardian angels of the active ingredient. These are often functional to optimize dispersibility and to stabilize the active ingredient against environmental and processing conditions.
Other Additives: Depending on the application, masterbatches can contain a wide array of additives such as fillers, nucleating agents, and slip/anti-block agents.
Types of Polymeric Matrices of filler masterbatch
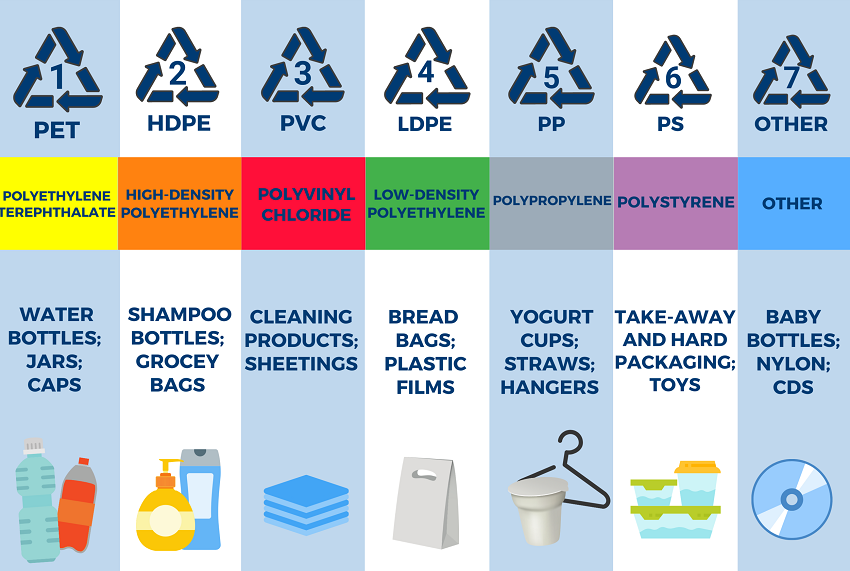
Polyethylene (PE)
- Characteristics: PE is known for its excellent chemical resistance, electrical insulation properties, and low moisture absorption. It’s flexible and has good impact resistance, although it has a relatively low melting point compared to other polymers.
- Applications: Given its versatility, PE-based filler masterbatches are widely used in packaging films, containers, household goods, and some automotive parts. It’s particularly favored in applications requiring good durability and flexibility.
Polypropylene (PP)
- Characteristics: PP is characterized by its stiffness, excellent chemical resistance, and higher melting point than PE. It also has good fatigue resistance.
- Applications: PP-based filler masterbatches are suitable for applications that require higher thermal resistance, such as microwaveable containers, automotive components, textiles, and various consumer goods.
Polyvinyl Chloride (PVC)
- Characteristics: PVC is known for its rigidity (in its unplasticized form), good chemical and corrosion resistance, and excellent flame retardancy.
- Applications: Filler masterbatches based on PVC matrices are used in construction materials (like pipes and fittings), medical devices, and packaging, where rigidity and flame retardancy are required.
Polystyrene (PS)
- Characteristics: PS offers ease of processing, dimensional stability, and a glossy finish. However, it is brittle and lacks the toughness of other polymers.
- Applications: PS-based filler masterbatches find applications in disposable cutlery, CD cases, and insulation materials where rigidity and aesthetics are important but where the product is not subjected to significant mechanical stress.
Polyethylene Terephthalate (PET)
- Characteristics: PET is valued for its strength, thermal stability, and barrier properties against gases and liquids.
- Applications: PET-based filler masterbatches are primarily used in the beverage industry for making bottles, as well as in packaging films and fibers for textiles, owing to their strength and clarity.
Polyamide (Nylon)
- Characteristics: Nylons are tough, have high tensile strength, excellent abrasion resistance, and a high melting point. They also absorb more moisture than most other polymers.
- Applications: Filler masterbatches with nylon matrices are used in automotive components, mechanical parts, and high-strength textile fibers.
Polycarbonate (PC)
- Characteristics: PC is noted for its high impact strength, transparency, and excellent temperature resistance.
- Applications: Given its clarity and strength, PC-based filler masterbatches are used in eyewear lenses, bulletproof glass, and various transparent applications requiring high impact resistance.
Thermoplastic Elastomers (TPE)
- Characteristics: TPEs combine the processing strengths of plastics with the elasticity of rubbers. They are flexible, can be stretched to moderate elongations, and return to their original shape.
- Applications: TPE-based filler masterbatches are used in seals, gaskets, and soft-touch components in consumer electronics.
Injection Molding and the Matrix
Here, we’ll identify the nitty-gritty of how polymeric matrices impact the injection molding process.
Masterbatching in Injection Molding
Injection molding is a versatile process used to manufacture a range of products, from small components to entire panels. Masterbatches come into play by transitioning the inherent properties of the base plastic—often starting life as pellets—towards the desired end product. For instance, they might alter the material color, introduce flame retardancy, or enhance UV resistance. By employing masterbatches, manufacturers can significantly reduce the production costs and complexity associated with handling multiple separate additives.
Application Insights: Automotive Resilience
In the automotive sector, the use of masterbatches is instrumental in rendering polymers suitable for a demanding environment. Here, a blend of UV-resistant and impact-modified polymers, facilitated by masterbatches, creates a useful resilience. Auto interior panels, exterior trim, and complex systems are all beneficiaries of this synergy between polymeric matrices and masterbatches.
Extrusion: Pushing the Possibilities
The polymeric matrices also shape the extrusion process, nudging the pliable under the heat and pressure to form long lengths of a consistent cross-section.
Film Extrusion and Matrix Optimization
Film extrusion is a key technique for the manufacture of plastic films used in packaging, agriculture, and construction. By employing specific masterbatches tailored for film extrusion, one can enhance the clarity, or introduce tactile properties such as soft-touch surfaces. The barrier properties of films can be fortified via masterbatches containing EVOH (ethylene-vinyl alcohol) resins, helping to keep perishables fresh or pharmaceuticals untainted.
Bagri-Cultural Films and Matrix Fertility
In the context of agricultural films, the polymeric matrix plays a crucial role in fertility, so to speak. Masterbatches formulated to improve light transmission, and those that incorporate infra-red (IR) reflecting elements, effectively demarcate the sunlight spectrum that reaches the soil, aiding in crop growth cycles.
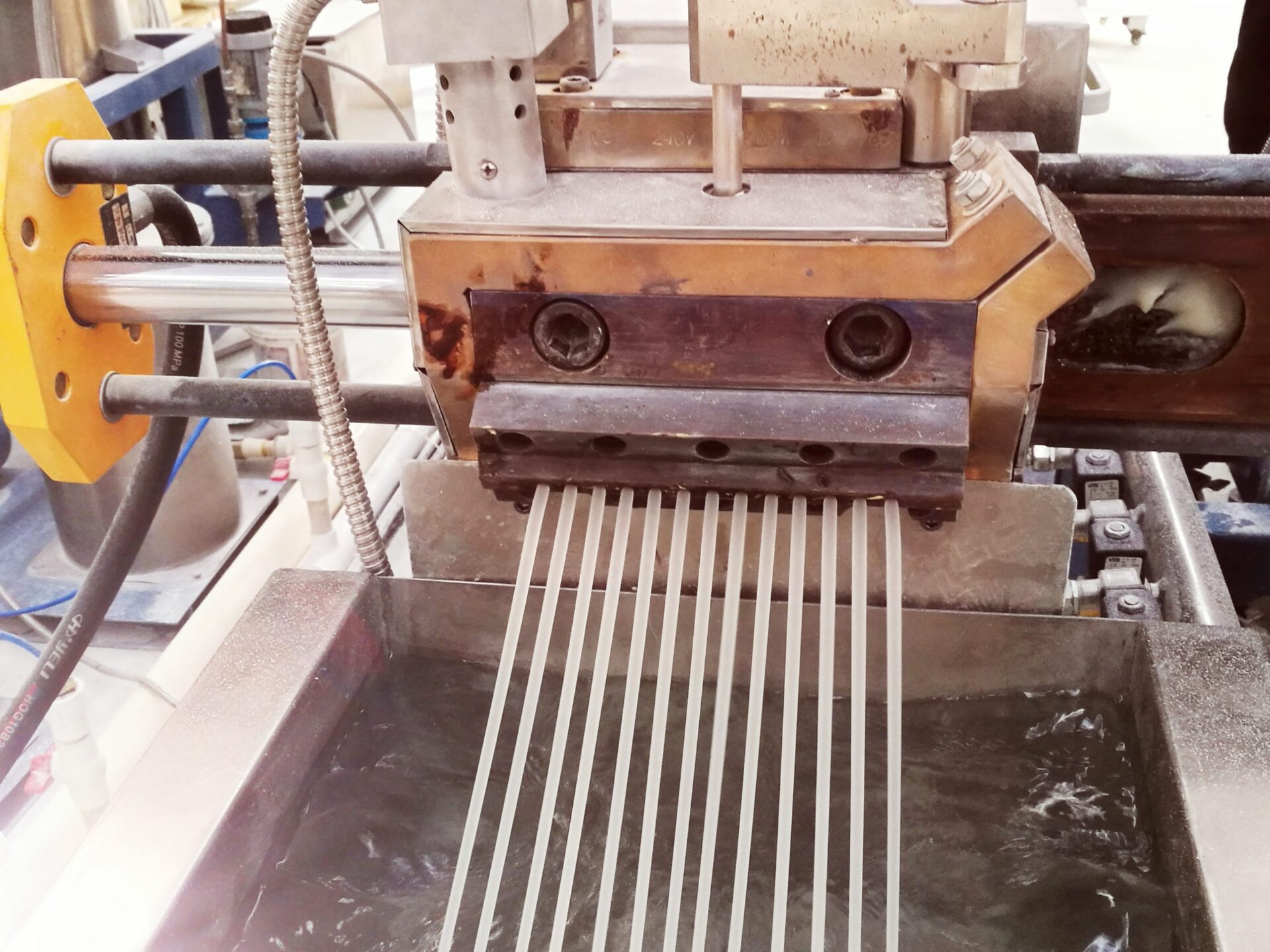
Textiles and the Polymeric Spin
The textile industry, too, is deeply woven with the impact of polymeric matrices and masterbatches.
Synthetic Fibers and Masterbind
Synthetic fibers like nylon, polyester, and polypropylene often start life as masterbatches. The spinning process, which turns these materials into fibers, can be significantly augmented by masterbatches designed to impart specific properties such as color consistency, mechanical strength, or flame retardancy.
Coloration Harmonization
Maintaining color consistency across textile materials is a significant challenge. With masterbatches, manufactures can ensure that colors are vibrant, uniform, and durable, meeting the stringent requirements of textile applications.
A Spectrum of Applications
The matrix and the masterbatch are not just confined to the realms of large-scale manufacturing. They find varied applications across the spectrum.
Household Items and Customization
From kitchen gadgets to storage solutions and from children’s toys to furniture, the versatility of masterbatches allows for intricate injection molding processes. Manufacturers can create a rainbow of color options, tailor products to be durable or flexible, and even bring intelligent surfaces to everyday items through active ingredient masterbatches.
Consumer Electronics and Performance Packaging
The stringent requirements of consumer electronics – like durability, conductivity, and heat resistance – are effortlessly met through the polymeric alchemy. Additionally, packaging for high-tech gadgets benefits from the color-coding and UV-resistance insulation that masterbatches can provide.
The Stratagem of Making the Right Matrix Choice
Choosing the right matrix is not simply about matching the colors or mixing in fillers. It’s about understanding the application, the environment in which the product will operate, and the characteristics that must be skilfully integrated.
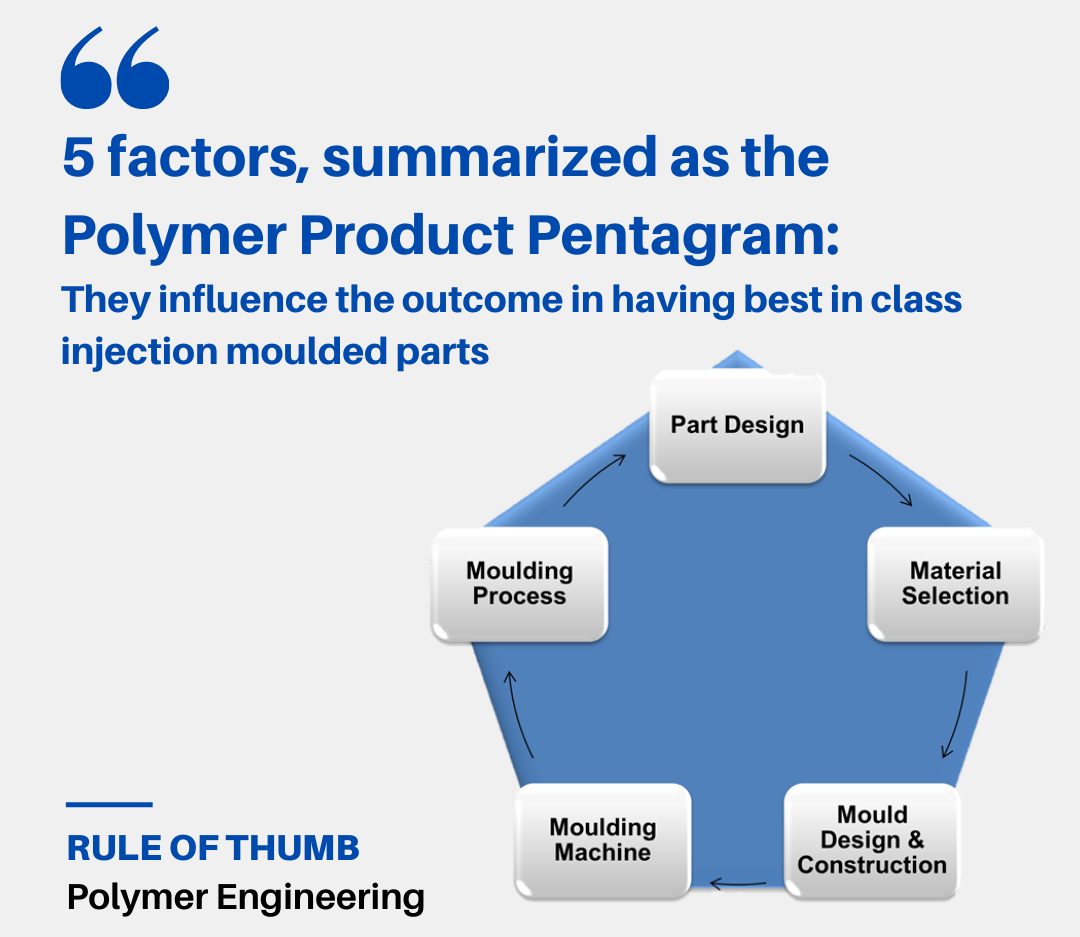
Considerations for Polymeric Selection in Molding
- Mechanical Properties: Is the end product going to be stressed? The polymeric matrix should be selected for its ability to maintain form under pressure.
- Environmental Conditions: High heat, chemical exposure, or outdoor weathering calls for specific matrix features to be imbued, such as weather-resistance or resistance to certain chemicals.
- Regulatory Requirements: Products often have to meet standards for health and safety. The polymeric choice should align with these stipulations, ensuring a safe and compliant product.
Technical Readiness for Masterbatching
- Compatibility Testing: The masterbatch and base resin should be chemically compatible to ensure a homogeneous blend.
- Life Cycle and Aging Studies: Assessing the long-term performance of the final product can dictate the masterbatch content needed for longevity.
- Process Optimization: Not all masterbatches work with all processing parameters; optimizations for temperature, pressure, and cycle times must be noted.
Continue your journey into the world of masterbatch by reading ‘Global Trends: The Demand for Filler Masterbatch Across Regions’.Click here to read more and expand your understanding.
The Art and Science of Mixing
Creating a masterbatch is where the art marries the science in the most literal sense. A resin blend’s proportions must be exact, the compounding process precise, and the additives evenly dispersed. This blend is then transformed into the characteristic pellets or products that will eventually wind up in the manufacturing line.
The Mixing Process
Polymeric compounds are mixed in specialized machines under controlled conditions. This stage of the process is critical, as it impacts the efficiency and efficacy of the masterbatch in altering the properties of the base resin.
Quality Control at the Mixing Stage
Quality control during mixing is not just about assessing the materials’ homogeneity visually; it must also include analytical testing to confirm chemical and physical changes have occurred as intended.
Masterbatch Manufacturing and Safety
The handling of the concentrated masterbatches, particularly those containing hazardous materials, is critical both for worker safety and to prevent environmental contamination.
Best Practices for Safe Handling
- Training and Awareness: Workers must be fully trained on the handling and emergency actions related to the relevant materials.
- Personal Protective Equipment (PPE): PPE should be provided and worn as mandated for the specific materials being handled.
- Containment and Spillage Management: Avoiding spillages and having a full procedure in place for cleanup are essential.
The Far-Reaching Impact of the Right Matrix
The polymeric matrix’s choice can be the pivotal point between a superior product and a mediocre one. It affects aspects ranging from the product’s appearance and utility to its durability and safety.
Market Penetration and Reputation
Products that stand out on the shelves for their consistency in color and quality, partially thanks to the right masterbatch, are more likely to be noticed and selected by consumers. Over time, they build a reputation for reliability and innovation, a valuable asset in the marketplace.
The Environmental and Cost Equation
Choosing a matrix that supports recyclability or is derived from sustainable sources can also have a profound impact on the eco-friendliness and costs of production.
Looking Forward: Matrix Technologies in Development
The world of masterbatches is not stagnant. New techniques, additives, and applications are continuously being developed, expanding the boundaries of what products can achieve.
Smart Additives and IoT Integration
With the rise of smart devices and the Internet of Things (IoT), masterbatches containing conductive elements or optical sensors are emerging—ushering in an era of intelligent, communicative products that respond to their environment.
Biodegradable Matrix Formulations
The quest for sustainable materials continues, with biodegradable and compostable masterbatches paving the way for a new breed of environment-friendly products that retain the convenience of plastic.
The Mastery of the Matrices Continues
In the final analysis, the corporate alchemists of today’s manufacturing environments stand upon the shoulders of giants. The polymers they shape into products are the raw material for modern magic. The polymeric matrices and the masterbatches are their wands.
Through a synthesis of innovation and traditional wisdom, today’s manufacturers can wield these wands to craft a better, brighter future, one product at a time. The decisions made in the matrix affect not only the finished product but the very fabric of the market it serves. The alchemy of manufacturing is a dynamic, continuous process, one that continuously refines the art and science of making things.
For those willing to dare, to dream, and to do, the possibilities are as boundless as the polymers themselves. It’s an exciting time to be in manufacturing, where the right matrix can be the catalyst for true transformation.
We encourage you to continue the conversation. Share your thoughts, experiences, and insights in the comments section below. The exchange of knowledge and ideas is essential if we are to collectively unlock the potential of filler masterbatch technology and drive the industry forward.
Whether you’re looking for a reliable supplier, interested in exploring our product range, or simply wish to learn more about our cutting-edge manufacturing processes, our team is ready to assist you. Contact us today to schedule a visit or consultation, and let’s explore how Megaplast can elevate your business to new heights. Your partnership in innovation starts here.