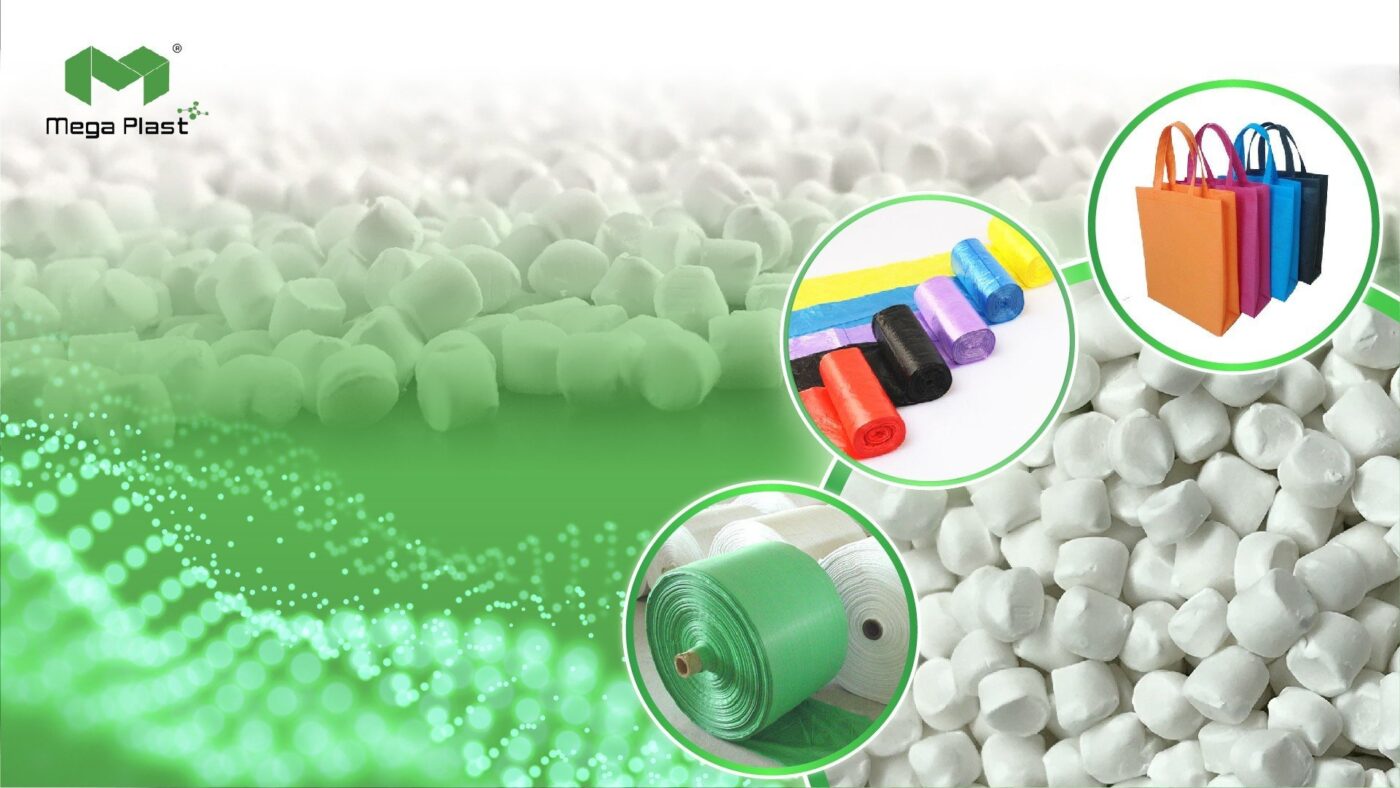
Masterbatch has been one of the most popular methods for adding color and reinforcement to plastic packaging for decades. It is often used to improve packaging materials’ physical and mechanical properties while reducing production costs. However, when choosing the masterbatch for your packaging needs, there are a few essential things to remember. This blog post will discuss five critical considerations before choosing filler masterbatch for the packaging industry.
Type of plastic granules
Are you looking for better packaging production results? Choosing the right plastic granules is one of the most important steps in packaging production. Each material’s processing conditions must be considered to ensure that the final product has remain durable and have an improved surface finish.
Consider the intended use of the end packaging
The packaging material’s application type plays a vital role in determining the kind of filler masterbatch used. For example, packaging materials used to store and transport food items must comply with FDA regulations and not release hazardous chemicals into the food. It is essential to consider the type of application when choosing the right filler masterbatch for your packaging needs.
Cost effective
Filler masterbatch has proven to be more cost-effective than other alternatives, such as colored plastic. However, the cost of filler masterbatch depends on the filler type and its percentage in the final product. While some fillers like calcium carbonate are cheaper, others like talcum powder can be more expensive. It is essential to c onsider overall cost-effectiveness when choosing the right sub-masterbatch.
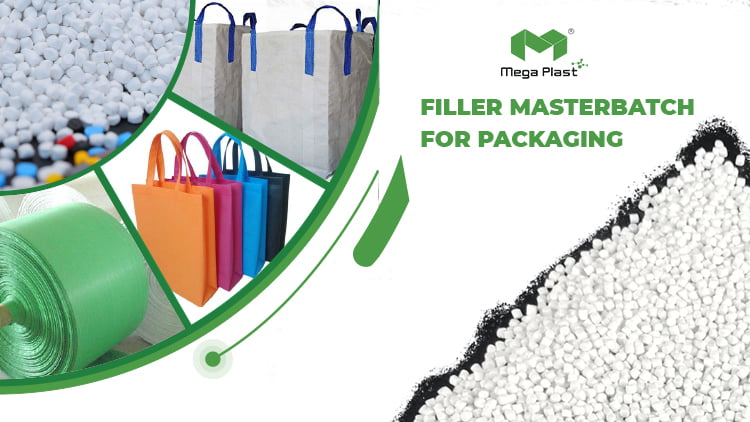
At Megaplast, product code NH2024/W262 is made from the best formula, a source of soft limestone powder, high quality, low impurities, and thanks to long experience; the Mega engineering team has designed the product code to help customers increase the filling rate up to 40%, helping to reduce production costs.
See detail at: https://megaplast.com.vn/product/pp-filler-masterbatch-for-pp-woven-nh2024-w262/
Filler dispersion
One of the essential aspects of filler masterbatch is the dispersion quality of the additive in the carrier resin. Poor filler dispersion can affect the final product’s mechanical properties and surface quality. Therefore, choosing fillers with good filler dispersion and uniform particle size is essential.
Compatibility with other additives
It is essential to ensure that the filler masterbatch is compatible with other additives used in the manufacturing process. Incompatibilities between additives can lead to processing problems and, in some cases, the production of a poor-quality product. Therefore, it is crucial to choose the right masterbatch to avoid any compatibility issues.
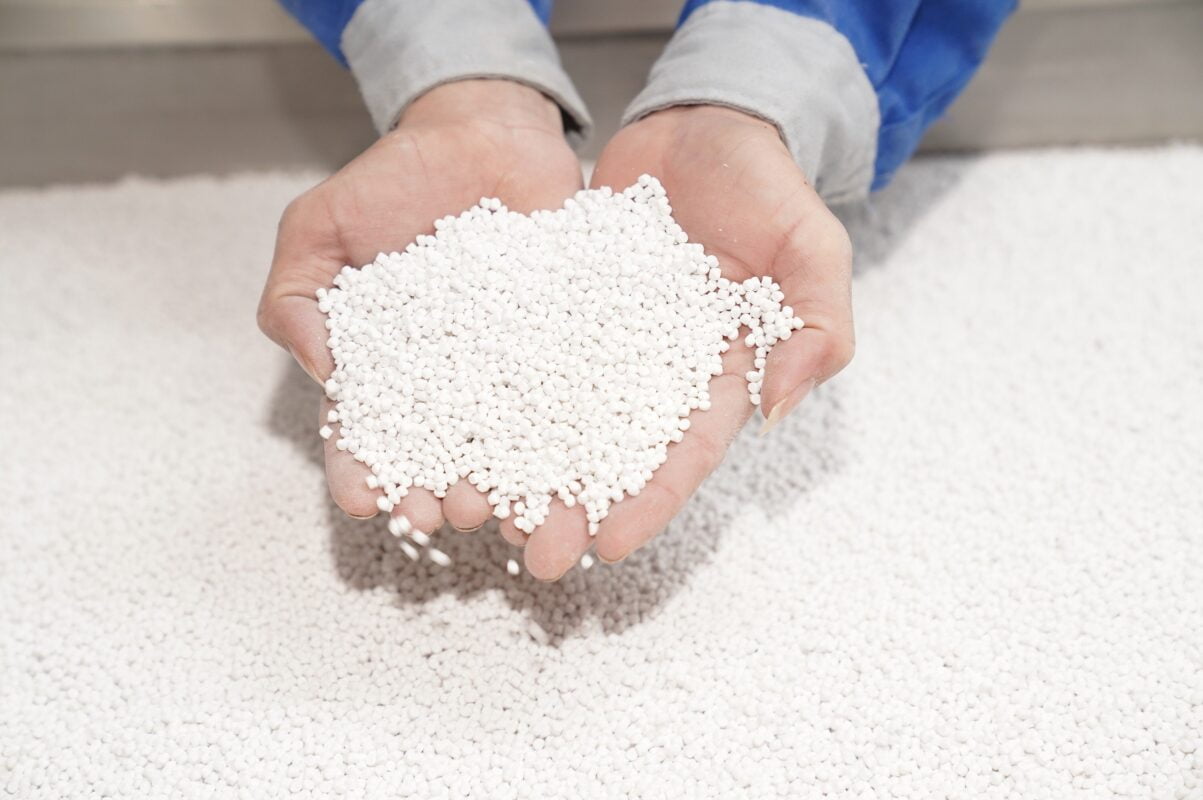
F261 or W202 of Megaplast brand is considered suitable for packaging production, meeting the above standards. The ingredient has a toughening additive that makes it possible for customers to use it at all machine speeds (including high rates> 400 MPM-550 MPM)
Refer to product codes F261 or W202.
By considering these factors, you can make informed decisions and produce high-quality, cost-effective packaging materials for your business. You need to work with a trusted supplier who can provide the filler masterbatch for your unique needs.