Filler masterbatch or CaCO3 Filler is the flagship product of Megaplast. It can be said that filler masterbatch is a significant step forward, opening a new era for the plastic industry. It is the best solution that manufacturers use to improve the performance of raw plastics. Filler masterbatch (CaCO3 Filler) contributes to solving problems for manufacturers, which is to reducing production costs.
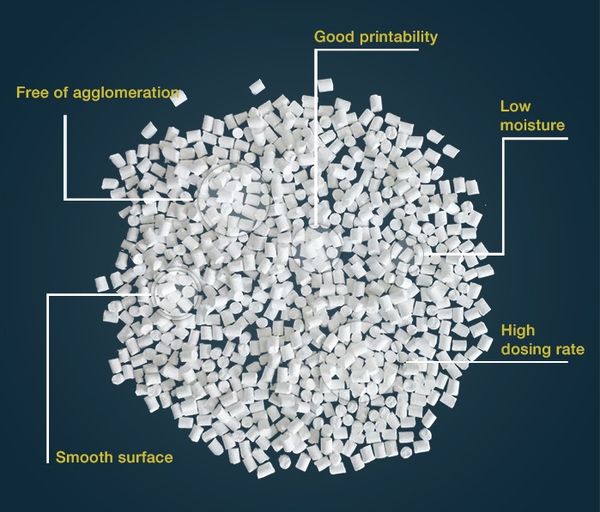
Table of Contents
The properties of filler masterbatch (CaCO3 Filler) are created from the nature of the base resin
Base resin (Polymer resin) is the base material used in plastic manufacturing, providing the desired properties and characteristics to the final product. On the other hand, Filler Masterbatch is an additive that contains a high concentration of fillers, such as Calcium Carbonate (CaCO3), which is added to enhance certain qualities of the plastic, such as hardness, dimensional stability, and cost-effectiveness.
The main difference between base resin and Filler Masterbatch lies in their composition and purpose.
Filler masterbatch on the production and consumer market is very diverse. Each type has distinct features, roles & characteristics. This difference is largely due to the different types of resin bases.
Talking about plastic – the original ingredient of filler masterbatch, plastic is a synthetic material derived from organic ingredients such as coal, natural gas, salt, cellulose, and especially crude oil. The nature of plastic is a polymer chain, so it can also be said that polymer refers to plastic, with molecules made of hydrogen and carbon atoms, sometimes in the presence of other elements such as oxygen, nitrogen, chlorine, silicon, fluoride, sulfur, phosphorus, etc.
Plastics are classified in many ways depending on their properties, function, or composition. One of the most common ways to divide plastics into groups is based on the thermal aspect. According to this feature, there are 2 types of plastic: thermoset and thermoplastic. Besides the thermal aspect, its molecular structure and composition (how many types of monomers are there?) are also basic principles for classifying plastics.
Therefore, it can be said that the variety of filler masterbatch (CaCO3 Filler) is based on the variety of the base resins.
Related news: Filler Masterbatch: Top 10 Powerful Applications and Benefits Across Key Industries
How is filler masterbatch (CaCO3 Filler) different from plastic polymer resin?
The plastic polymer resin is purely polymer chains without any other components. Filler masterbatch, on the other hand, is a mixture consisting of multiple ingredients.
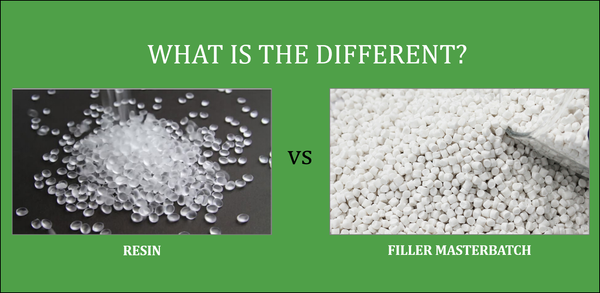
Plastic is one of the most important components of the calcium carbonate masterbatch that serves as the carrier. Another vital element, that accounted for the vast majority of plastic filler, approximately 70-80% of the mixture, is calcium carbonate powder. Besides base plastic and CaCO3 powder, filler masterbatch also consists of pigment powder and several additives depending on the customer’s requirements.
Why do you need filler masterbatch (CaCO3 Filler) when you already have plastic resin?
First of all, in essence, primary plastic is composed of macromolecular groups (Polymers). These polymer groups are again made up of monomers (monomolecular) through a binding reaction. To create plastic, people synthesize natural materials such as Cellulose, rubber latex, etc., or Ethin, Benzol, Ethen gas, etc.; the essential element is kerosene.
Thus, the use of 100% virgin plastic to produce plastic products has the following disadvantages:
- Firstly, virgin plastic is less environmentally friendly. Products made from primary plastic are almost non-biodegradable under natural conditions.
- Second, kerosene – the main raw material that makes up primary plastic must be imported mainly from abroad. This makes the end product expensive and vulnerable to the relatively unstable supply of kerosene.
- Third, petroleum is a non-renewable resource. Therefore, relying on kerosene as an input material will make the product less stable and sustainable.
From these facts, plastic filler masterbatch was born – fully meeting the requirements of finished plastic products and helping businesses save significantly on costs.
Related news: Masterbatch Explained: The Secret Ingredient Transforming Plastic Manufacturing
Filler masterbatch (CaCO3 Filler) production process
The production process of filler masterbatch takes place in the following 4 basic stages:
- CaCO3 stone powder, base resin, and additives are mixed by machine at a high speed.
- The mixture is melted into a liquid form at a high temperature.
- The liquid mixture is cooled and then pushed forward by the screw in the twin-screw extruder and pressed into the mold.
- Plastic is put into the cutter to cut into granules. These particles will be added to the resin to bring new features to the raw plastic.
Explore Megaplast’s filler masterbatch products
For more information about Megaplast – a member of Nhat Huy Group: https://megaplast.com.vn/news/introduction/
For more information about Nhat Huy Group: https://nhathuygroup.com.vn