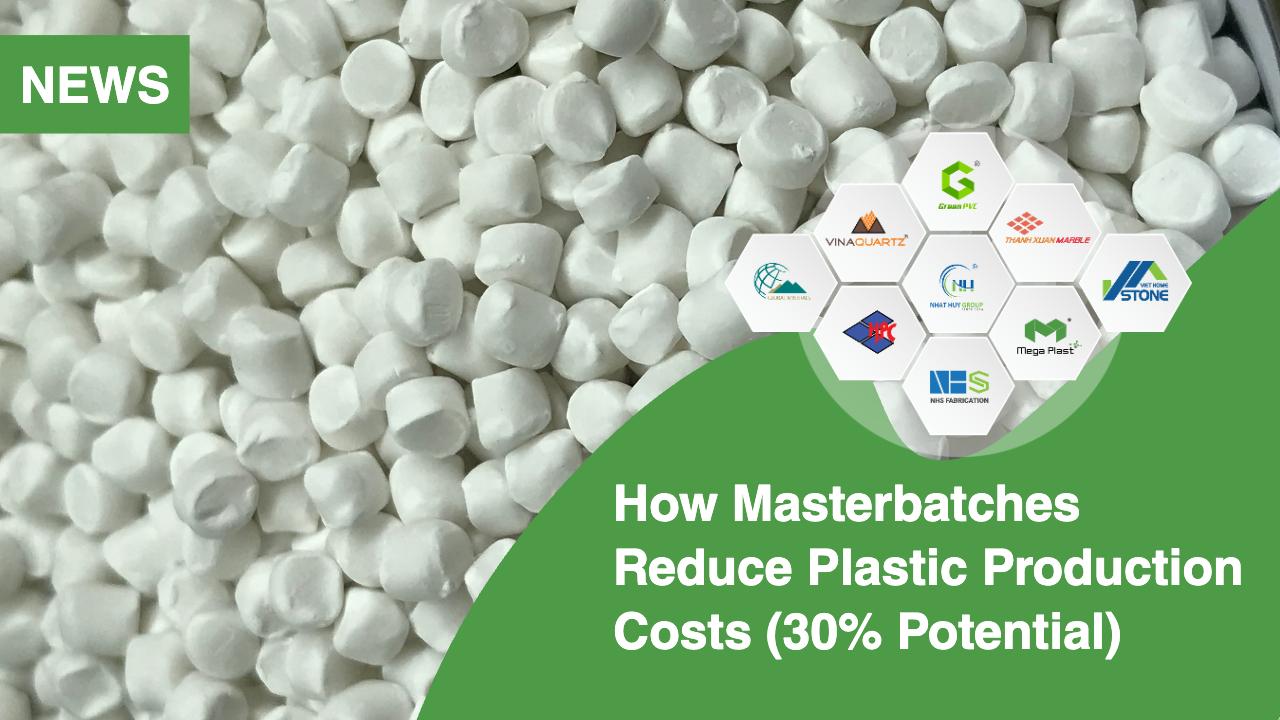
Here’s a breakdown of how masterbatches, particularly filler masterbatches, can contribute to a potential 30% cost reduction in plastic production. Please note the 30% figure is an illustrative example, and actual cost savings can vary significantly depending on specific material choices and production factors.
1. Cost of Raw Materials:
Base Resin: The carrier resin (like polyethylene or polypropylene) usually constitutes the largest portion of the cost of plastic production.
Filler: Filler materials, like calcium carbonate, are naturally abundant and significantly less expensive per unit volume compared to pure resins.
Additives and Pigments: These can be costly components but are used in smaller percentages in the overall masterbatch mix.
2. Dilution Factor:
High Loading of Filler: Filler masterbatches typically contain a high concentration of filler, potentially up to 80% by weight. This means a significant amount of the expensive base resin is replaced with a more affordable filler.
Example: Let’s say 100kg of pure plastic resin costs $100. For a filler masterbatch containing 80% filler and 20% carrier resin, you would only need 20kg of resin along with 80kg of cheaper filler to produce effectively the same 100kg end product.
3. Volume Savings:
Reduction in Resin Usage: By adding fillers, overall resin usage is reduced, leading to direct cost savings. In the previous example, you only use 20kg of resin compared to 100kg of pure resin.
4. Additional Benefits:
Lightweighting: In some cases, the lighter weight of filler masterbatches can lead to material savings and potentially lower shipping costs.
Processability: Certain fillers can enhance flow properties during molding, reducing cycle times and decreasing energy consumption.
Estimated breakdown of potential cost savings from using masterbatch
Raw Materials Variable | (-5% to +5%)
Masterbatch can introduce cost savings through filler content being cheaper than pure resin. However, this depends on the specifics:
* If your filler is 80% cheaper than resin and makes up 50% of the masterbatch, you might see a +5%** cost increase due to needing more masterbatch to achieve the same resin content.
* If your filler is 50% cheaper than resin and makes up 20% of the masterbatch, you might see a -5%** cost reduction due to using less expensive filler.
Example Calculation (Illustrative): Let’s consider a simplified example to illustrate potential savings:
- Pure Resin Cost: $1/kg
- Filler Cost: $0.20/kg
- Masterbatch Loading: 80% filler and 20% resin + additives
- Cost per kg of Masterbatch: ($1 x 0.20) + ($0.20 x 0.80) = $0.36/kg
- Effective Cost of Resin in Masterbatch: $0.36 / 0.20kg resin = $1.80/kg
While there’s an increase compared to pure resin cost, this calculation demonstrates how the overall amount of resin required decreases, leading to significant cost savings. In this scenario, by using a masterbatch, a 30% cost reduction could be achieved.
Important Considerations: The actual cost savings depend on the specific resin, filler, additive prices, and desired properties. Not all applications are suitable for high filler loading, as it can affect mechanical properties like strength and impact resistance.
It’s crucial to work with a reputable masterbatch supplier like Mega Plast to optimize formulations and achieve a cost-performance balance while ensuring your product meets specification requirements.
Dilution Factor (High Loading of Filler) | 5% to 20%
Using a high filler content (e.g., 50-80%) in masterbatch can decrease the amount of expensive resin needed. This translates to potential cost savings on resin usage. However, keep in mind that excessive filler might compromise product properties. Aim for an optimal balance.
Volume (Reduction in Resin Usage) | 3% to 10%
Similar to the dilution factor, using masterbatch can reduce the overall volume of resin required for production. This can lead to cost savings in material handling, storage, and potentially lower shipping costs due to reduced weight (see Lightweighting).
Lightweighting (Lower Shipping Costs) | 1% to 5%
Depending on the application and filler type, masterbatch can contribute to a lighter final product. This can lead to cost savings in transportation due to reduced weight. The impact might be smaller for bulkier items.
Processability (Decreasing Energy Consumption) | 2% to 8%
Some masterbatches can improve processability, allowing for faster cycle times or lower processing temperatures. This could potentially lead to energy consumption savings. However, this benefit depends on the specific masterbatch type and processing equipment.
Important Considerations:
Cost-benefit analysis is crucial: Carefully evaluate the cost of the masterbatch itself compared to the potential savings from reduced resin usage, volume reduction, and other factors.
Impact on product properties: Ensure the chosen masterbatch filler doesn’t compromise the desired properties of your final product.
Testing is recommended: Conduct trials with different masterbatch options to determine the optimal balance between cost savings and product performance.
Overall, the estimated cost saving from using masterbatch can range from a slight decrease to a moderate increase (depending on raw material cost changes), with potential additional savings of 10-30% from dilution factor, volume reduction, lightweighting, and processability improvements.
Remember, these are just estimates. The actual cost savings will vary depending on your specific circumstances.
Pingback: What Is Filler Masterbatch? An In-Depth Overview