What is PE Filler Masterbatch?
PE filler masterbatch is a combination of 80-85% pure Calcium Carbonate CaCO3 powder with polyethylene PE as the carrier and other appropriate additives. PE filler masterbatch helps to reduce production costs and improve the physical properties of the finished product.
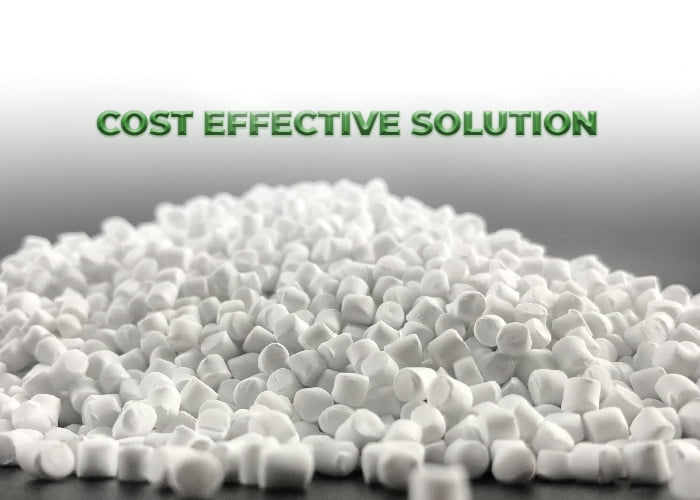
It is normally bright white, glossy, uniform-grain-size.
The usage rate is 15%-50% depending on your specific products
May you interested: What is Filler Masterbatch? How do manufacturers use filler masterbatch to achieve optimal profit today?
Application of PE Filler masterbatch
• Blown film: PE-based films & bags (Roll bags, T-shirt bags, garbage bags, shopping bags, agricultural films, breathable films…)
• Injection molding: Housewares, tanks, toys
• Extrusion: PE/HDPE pipe, bar, …
• Blow molding: HDPE bottles, containers, cans, …
• Woven: HDPE Tarpaulin
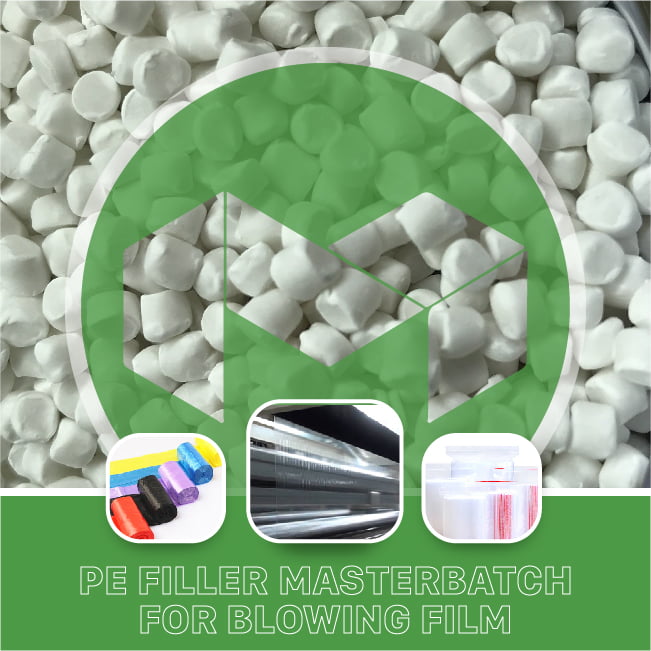
The common problems in the use of PE Filler masterbatch
Blown film
- Water carry over
Main reasons: Due to the moisture content of fillers
Treatment method: Need to dry filler masterbatch to remove moisture before using, reduce the rate of additives. Add anti-moisture additive.
- Uneven dispersion
Main reasons: low processing temperature, the poor mixing ability of ingredients, unsuitable materials
Treatment method: Increase the processing heat and increase the mixability of the material. Change the raw materials or the recipe of the ingredients; reduce the percentage of filler masterbatch.
- Film loses the transparency
Main reasons: The recipe for mixing ingredients and filler masterbatch is not suitable, there are many low heat running additives. Running low cooling wind, the glue has not completely crystallized.
Treatment method: Adjust the recipe for mixing ingredients. Adjust the processing temperature, select the appropriate plastic code. Large, fast cooling gas boost to increase clarity.
Read more: What is Film adhension, Water carry over and Uneven dispersion in Blown Film while using filler masterbatch? How to solve it?
Extrusion
- Easy warping
This problem can be caused by the following reasons:
+ The base resin has an unsuitable MFI index.
+ The thickness between the plates is not uniform
+ The glue between the layers is uneven or the water glue should have moisture, the moisture removal process also causes warping.
- Easy breaking
+ Due to the plastic resin not guaranteed quality. You have to use the correct plastic resin code which is suitable for each specific application.
+ The cooling process should perform slowly to avoid rapid heat loss. Rapid heat loss and uneven heat loss between areas of the plate also cause breaking errors.