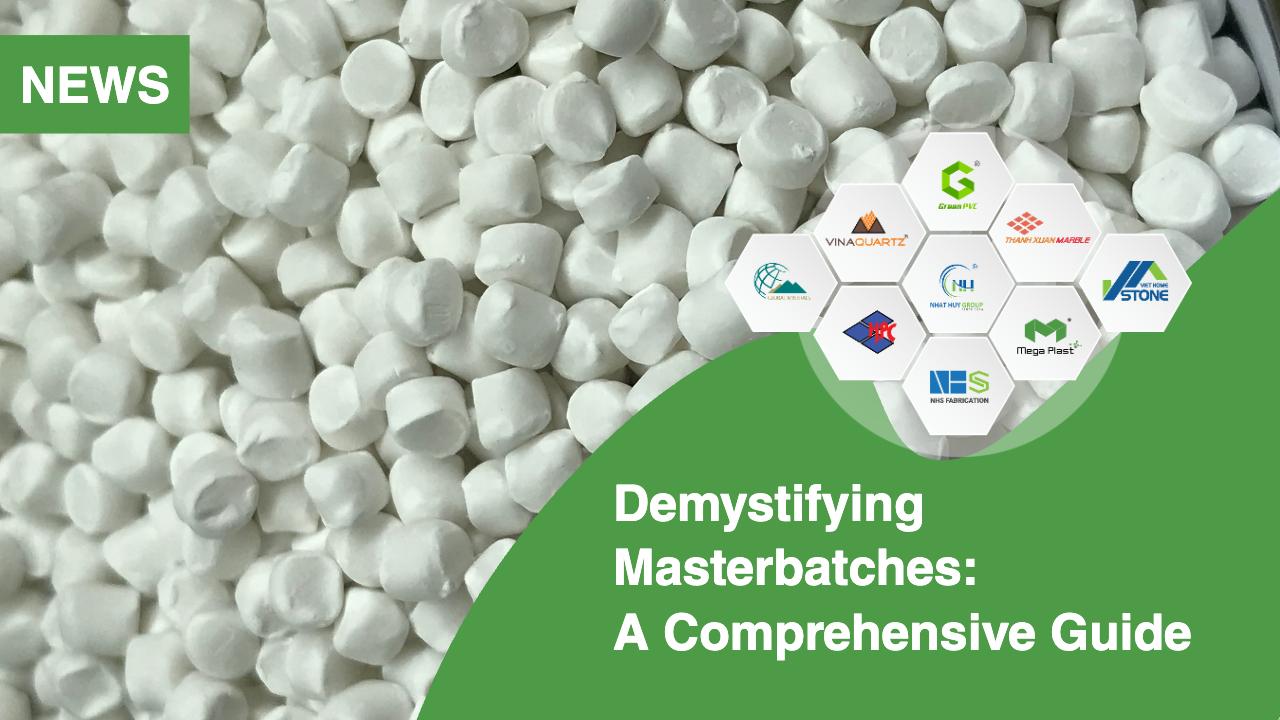
Masterbatch play a crucial role in the world of plastics, adding functionality and aesthetic appeal to diverse applications. But what exactly are they? This guide delves into the world of masterbatch, focusing specifically on filler masterbatch and their unique properties, production process, and key components. But before we dive into the masterbatch market trends, let’s understand what masterbatch are.
Table of Contents
Masterbatch Explained
Think of a masterbatch as a concentrated concoction of additives, pigments, or fillers blended into a carrier resin. Imagine a tiny pot of concentrated color that, when mixed with plain yogurt, transforms it into a vibrant fruit-flavored treat. Masterbatch function similarly, transforming base polymers (the plain yogurt) into functional or aesthetically pleasing final products.
Masterbatch are concentrated mixtures of pigments and/or additives blended together in a carrier material like resin or wax. These additives can be used for coloring plastic products (color masterbatch) or imparting other properties like strength, flame retardancy, or UV resistance (additive masterbatch). By adding small quantities of masterbatch during plastic processing, manufacturers can achieve desired colors and functionalities in their final products.
Types of Masterbatch
Masterbatch can be categorized into various types based on its function or application:
1. Color Masterbatch
Used to impart specific colors to plastic products, color masterbatch is a cost-effective and precise way to ensure vibrant and uniform hues across production batches.
2. Additive Masterbatch
This type enhances the functional properties of plastic products, such as:
- Anti-UV Masterbatch: Improves resistance to sunlight and prevents degradation.
- Flame Retardant Masterbatch: Adds fire-resistant properties to plastic materials.
- Anti-Static Masterbatch: Reduces static electricity build-up on plastic surfaces.
3. Filler Masterbatch
Filler Masterbatch, commonly made with calcium carbonate (CaCO3) or talc, reduces raw material costs and enhances the mechanical properties of plastics, such as rigidity and heat resistance.
4. Black and White Masterbatch
Specialized masterbatch used for creating black or white plastic products with high opacity, brightness, and consistency.
Summary of Market Trends in the Masterbatch Industry
The masterbatch industry is experiencing significant growth driven by several key trends, according to market research experts at Mordor Intelligence.
Dominant Packaging Segment
- Masterbatch are widely used in various packaging applications, including rigid containers (like bottles and tubs) and flexible films (like food wraps).
- White masterbatch are particularly popular due to their ability to enhance product aesthetics, ease of use, and excellent dispersion. They are also considered food-safe, making them ideal for food packaging.
- Rising demand for packaged food, particularly in Asia-Pacific due to changing lifestyles and busy schedules, is driving the use of masterbatch in food packaging.
- Growth in the North American food processing industry and reliance on packaged foods are further contributing to the demand for masterbatch.
- Statista predicts a 4.4% CAGR for the European plastic packaging industry by 2026, suggesting a continued rise in masterbatch use.
Asia-Pacific Leads the Market
- This region, with China and India as key players, is projected to dominate the masterbatch market.
- Asia-Pacific is a major hub for electronics production, supplying to various industries globally. This necessitates a large volume of masterbatch for electrical components.
- China, the world’s largest food industry and plastic producer, is expected to see consistent growth in customized food packaging, further boosting the demand for masterbatch.
- India’s booming e-commerce sector, predicted to reach USD 350 billion by 2030, will significantly increase the demand for packaging and consequently, masterbatch.
Overall, the masterbatch market is poised for steady growth globally due to these trends. To understand the masterbatch’ role in driving industry growth, let’s delve into the production process itself. While the specifics can be intricate, a basic understanding of the key steps involved sheds light on their importance.
The journey of a masterbatch begins with the selection of high-quality raw materials. Let’s explore the key ingredients:
- Pigments: These vibrant colorants are responsible for adding color to the masterbatch. Mega Plast offers a diverse range of pigments to cater to various color requirements.
- Polymers: The carrier resin acts as the base, holding the pigments and other additives together. We carefully select the most suitable polymers based on compatibility and desired final product properties.
- Additives: These specialized ingredients enhance specific functionalities like UV protection, flame retardancy, anti-static properties, or improved processing characteristics.
Each raw material plays a vital role:
- Pigments: These come in various forms, such as organic and inorganic pigments, and are chosen based on desired color intensity, opacity, and lightfastness.
- Polymers: The selection of polymers depends on the target application, compatibility with other components, and desired final properties like strength, heat resistance, and flexibility. Common carrier resins include polyethylene (PE), polypropylene (PP), and polystyrene (PS).
- Additives: A wide range of additives can be incorporated, each offering specific functionalities. For example, anti-oxidants enhance shelf life, while slip agents improve processing efficiency.
Unveiling the Masterbatch Production Process: From Raw Materials to Finished Product
While the previous section briefly touched upon the production process, let’s now delve deeper into the fascinating journey of transforming raw materials into a functional masterbatch. Here’s a further breakdown of the key steps involved:
1. Weighing and Pre-Mixing:
Each raw material, including pigments, polymers, and additives, is meticulously weighed according to a predetermined formulation.
Pre-mixing these components ensures even distribution and facilitates the subsequent blending process.
2. High Shear Mixing:
The pre-mixed ingredients are fed into a high-shear mixer, where they are subjected to intense mechanical force and heat.
This process disperses the pigments and additives uniformly throughout the carrier resin, creating a homogenous mixture.
Different types of mixers are employed depending on the desired level of dispersion and the properties of the raw materials.
3. Extrusion:
The well-mixed material is then forced through a specialized extruder, resembling a large, heated screw.
The extruder applies additional heat and pressure, ensuring complete homogenization and melting of the components.
The molten masterbatch is then shaped through a die into various forms, such as strands, pellets, or granules, depending on the desired application and ease of handling.
4. Cooling and Drying:
The extruded masterbatch needs to be cooled rapidly to prevent unwanted changes in its physical properties.
Air or water cooling methods are typically employed to solidify the masterbatch efficiently.
Depending on the production process, the cooled masterbatch might require further drying to remove any residual moisture.
5. Quality Control:
Rigorous quality control procedures are implemented throughout the production process, from raw material inspection to final product testing.
This ensures the masterbatch meets the desired specifications for color consistency, dispersion, processing characteristics, and other crucial parameters.
6. Packaging and Storage:
The finished masterbatch is then packaged in moisture-proof containers to protect it from environmental factors and ensure long-term stability.
Proper storage practices, including temperature and humidity control, further guarantee the quality and performance of the masterbatch until it reaches its intended use.
The Final Results of Masterbatch
Masterbatch offer a wider range of final results than just vibrant colors. Here’s another example:
- Filler Masterbatch: As highlighted earlier, these masterbatch contain fillers like calcium carbonate or talc. These fillers not only reduce the cost of the final product but also offer benefits like:
- Improved stiffness and dimensional stability: This can be crucial for applications requiring structural integrity, such as automotive parts or furniture components.
- Reduced shrinkage: Filler masterbatch can minimize shrinkage during the molding process, leading to more precise and consistent final product dimensions.
- Enhanced processability: Some fillers can improve the flow properties of the plastic, making it easier to mold and shape.
By understanding the production process and potential final results of masterbatch, you gain a deeper appreciation for their versatility and impact on various plastic applications. Mega Plast is committed to providing high-quality masterbatch that empower manufacturers to achieve superior results, efficiently and sustainably.
Applications of Masterbatch
Masterbatch is used across a wide range of industries and applications, including:
- Packaging: For colored films, bottles, and containers with UV resistance or anti-static properties.
- Automotive: Enhances the performance and appearance of dashboards, bumpers, and interior trims.
- Consumer Goods: Provides vibrant colors and durability for household items, furniture, and toys.
- Construction: Adds strength, UV resistance, and color to pipes, cables, and profiles.
Explore all about Filler Masterbatch benefit and applications
Mega Plast’s Masterbatch: Standing Out from the Crowd
At Mega Plast, we take pride in crafting high-quality masterbatch. Here’s what sets our product apart:
- Cost-Effectiveness: Our masterbatch offer significant cost savings compared to using pure resins, making them ideal for non-critical applications where aesthetics are less crucial.
- Lightweight Potential: By incorporating fillers, we can reduce product weight, potentially lowering transportation and material costs.
- Enhanced Stiffness: Our masterbatch improve handling characteristics and reduce product warpage, ensuring a professional final appearance.
- Good Printability: We ensure smooth ink adhesion for clear and vibrant graphics on your molded parts.
- Efficient Processing: Our masterbatch are formulated for efficient mixing and dispersion, streamlining production processes.
Conclusion
Masterbatch is an indispensable component in the plastics industry, offering cost-effective solutions for adding color, functionality, and enhanced properties to plastic products. By understanding the types and applications of masterbatch, manufacturers can optimize their production processes and deliver superior-quality products.
Pingback: What Is Filler Masterbatch? An In-Depth Overview
Pingback: Masterbatch Manufacturing: Art and Science Explored