Introduction
In the dynamic realm of plastic manufacturing, the significance of masterbatch cannot be overstated. Among the array of masterbatch variants, Polypropylene (PP), Polyethylene (PE), and White Filler Masterbatch stand out as exemplars of high-quality solutions, offering unparalleled versatility and performance. This article delves into the intricacies of these masterbatches, unraveling the excellence they bring to the world of plastics. For a more comprehensive explanation of masterbatches, including their types and applications, you can refer to our guide: Demystifying Masterbatches: A Comprehensive Guide
Polypropylene (PP) Masterbatch
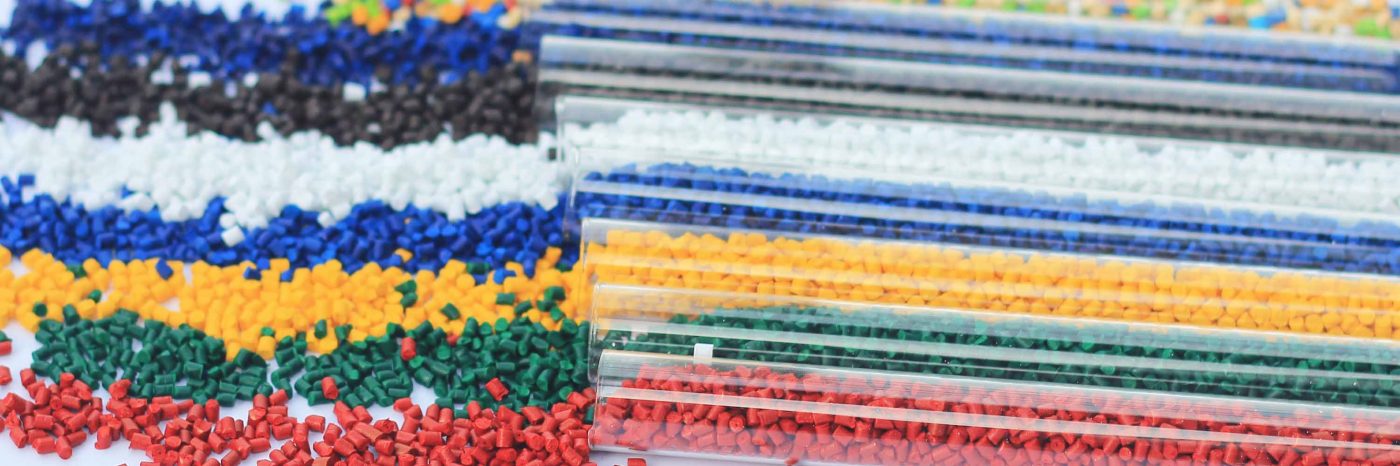
Polypropylene (PP) Masterbatch is a concentrated mixture of pigments and/or additives encapsulated during a heat process into a carrier resin, typically polypropylene. It is used in the plastics industry to impart color, enhance properties, and facilitate the manufacturing process of polypropylene-based products. The masterbatch ensures uniform dispersion of pigments and additives in the final plastic product, offering advantages such as ease of handling, improved color consistency, and efficient production.
The chemical characteristics of Polypropylene (PP) Masterbatch depend on its composition, which includes pigments, additives, and the carrier resin (polypropylene). Here are some general features:
- Carrier Resin (Polypropylene): As the base material, polypropylene is a thermoplastic polymer with high chemical resistance, good heat resistance, and excellent stiffness. It serves as the matrix for the pigments and additives.
- Pigments: These are colorants added to the masterbatch for coloring the plastic product. Pigments can be organic or inorganic compounds, and their chemical characteristics vary based on the desired color and application.
- Additives: Various additives may be included to enhance specific properties of the final product. Common additives include UV stabilizers, antioxidants, antistatic agents, and processing aids. Each additive has distinct chemical characteristics to provide desired functionalities.
It’s important to note that the exact chemical composition can vary between different formulations of Polypropylene Masterbatch, as they are tailored for specific applications and requirements. Manufacturers often customize masterbatch formulations to meet the needs of different industries and end products. For exemple at Megaplast we use
Polyethylene (PE) Masterbatch

Polyethylene (PE) Masterbatch is a concentrated mixture of pigments, additives, and a carrier resin (polyethylene) that is used to color or impart specific properties to plastic products during the manufacturing process. Here are key components and features:
- Carrier Resin (Polyethylene): Polyethylene is a common thermoplastic polymer that serves as the base material for the masterbatch. It provides the matrix in which pigments and additives are dispersed.
- Pigments: Pigments are colorants added to the masterbatch to achieve the desired color for the plastic product. They can be organic or inorganic compounds and are finely dispersed in the carrier resin.
- Additives: Various additives may be included in the masterbatch to enhance specific properties of the final plastic product. These additives can include UV stabilizers, antioxidants, flame retardants, and other functional agents.
Polyethylene Masterbatch is designed to simplify the coloration and modification of plastic resins. It allows manufacturers to incorporate color and other desired properties into the plastic product without having to handle raw pigments and additives separately. The masterbatch is typically added to the base polymer during the processing of plastic materials, ensuring uniform color distribution and consistent performance in the final product.
PE masterbatch, with its wide-ranging applications and adaptability, is a cornerstone in the plastic industry. The distinctive features of PE masterbatch, includes its flexibility, excellent electrical insulation, and resistance to chemicals. Whether in the production of films, pipes, or containers, PE masterbatch stands as a reliable choice for enhancing the properties of diverse plastic products.
White Filler Masterbatch
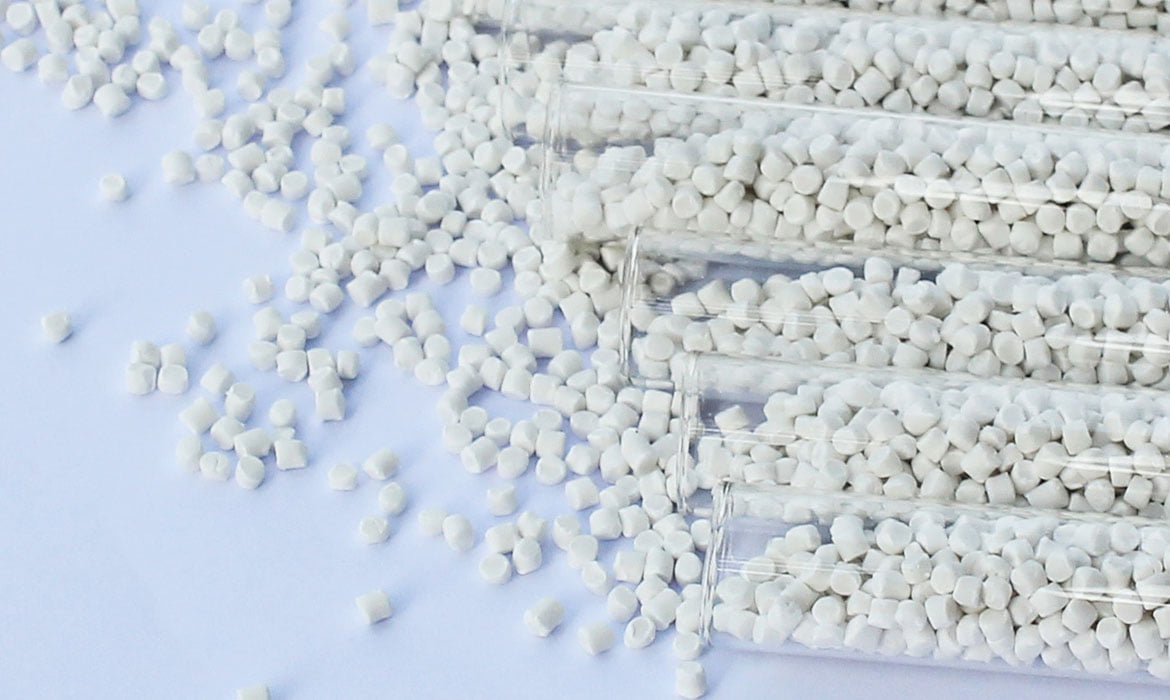
White Filler Masterbatch is a specialized additive used in the plastics industry to achieve a white color in plastic products while simultaneously enhancing certain properties. Here are the key components and features:
- Carrier Resin: The masterbatch consists of a carrier resin, which is often a polymer like polyethylene (PE) or polypropylene (PP). This resin acts as the base material that carries and disperses the pigments and additives.
- Titanium Dioxide (TiO2): The primary component responsible for the white color in the masterbatch is usually titanium dioxide. TiO2 is a white pigment widely used in various industries, including plastics, for its excellent opacity and brightness.
- Fillers: In addition to TiO2, White Filler Masterbatch may contain other fillers to improve the overall performance of the plastic, such as calcium carbonate (CaCO3). Fillers can enhance properties like stiffness, impact resistance, and dimensional stability.
- Additives: Depending on the desired properties, the masterbatch may include additional additives such as dispersants, stabilizers, or processing aids.
White Filler Masterbatch is added to the base polymer during the plastic manufacturing process to achieve a consistent and uniform white color in the final product. It finds applications in a wide range of industries, including packaging, textiles, automotive, and consumer goods, where a bright and opaque white appearance is desired.
White filler masterbatch emerges as a beacon of excellence in achieving the desired color and opacity in plastic products. This section of the article navigates through the formulation and production processes of white filler masterbatch. From its composition of high-quality pigments and carrier resins to the meticulous blending techniques, the result is a masterbatch that imparts an impeccable white hue to a spectrum of plastic applications.
Environmental Considerations
As sustainability takes center stage, the article discusses the eco-friendly aspects of PP, PE, and White Filler Masterbatch. It examines how these masterbatches contribute to resource efficiency, recyclability, and reduced environmental impact, aligning with the global thrust toward greener and more sustainable plastic solutions.
Conclusion
In conclusion, the article offers a comprehensive overview of the excellence encapsulated in Polypropylene (PP), Polyethylene (PE), and White Filler Masterbatch. From their unique properties to applications, market trends, and environmental considerations, this exploration unravels the layers of innovation and quality that define these high-performance masterbatches in the realm of plastic manufacturing.