Undeniably, the appearance of Filler masterbatch (or calcium carbonate filler) is increasingly promoting the development of the plastic industry to become the industry of the world. The benefits of filler masterbatch for the plastic industry, in general, have been mentioned quite a bit. The information below refers to the use of CaCO3 filler masterbatch for the packaging industry in particular – one of the largest areas in the plastic industry.
The final products of the packaging industry can be mentioned as shopping bags, wrapping films, roll bags, garbage bags, etc. They all contain the filler masterbatch ingredient but are consumed differently between the end products because of the difference in characteristics and technical requirements of each product. Therefore, it is quite risky for plastic enterprises to randomly select any kind of auxiliary material for the production of packaging because it can reduce the quality of the final product.
So what kind of filler masterbatch should the packaging industry use?
PE filler masterbatch
PE filler masterbatch is made from PE (Polyethylene), CaCO3, and other additives. It is a familiar additive for the packaging industry, especially in blown films due to its suitable mechanical properties such as high ductility, impact strength, and low friction.

Using calcium carbonate PE filler significantly reduces production costs, helping to lower the cost of the final product. Some common applications of PE masterbatch filler in blown films include shopping bags, T-shirt bags, garbage bags, etc. In addition, calcium carbonate PE filler is also used in the production of PP woven bags, poly films, multi-layer films, etc
PP filler masterbatch
PP filler masterbatch is composed of PP (polypropylene), CaCO3, and other additives. Its properties are similar to those of polyethylene, but a bit stiffer and more heat resistant. Therefore, synthetic PP filler is often used in PP woven sacks and nonwovens to reduce production costs and minimize the environmental impact of the production process.
Transparent filler masterbatch
Another type of filler that can be used in the production of packaging is a transparent filler, which is a combination of BaSO4 (Barium sulfate) or Na2SO4 (Sodium sulfate), plasticizers, and other special additives. Most plastic manufacturers use transparent fillers to improve some end product properties such as stiffness, mechanical properties (bending strength, impact strength), tear-resistance, and criticality. The most important is whiteness.

Thanks to the two ingredients barium sulfate & sodium sulfate, the final products have stunning luminosity and transparency. In addition, the use of transparent fillers shortens the time required for each product cycle, thereby facilitating improved production efficiency. Because of those advantages, this material is widely used in many applications such as packaging films, containers, bottles, cans, etc.
What are the advantages of CaCO3 filler masterbatch in the packaging industry?
One of the most important plastic fillers is CaCO3 Filler Masterbatch, also known as calcium carbonate filler. It is a blend of calcium carbonate (CaCO3), which accounts for more than 70% of the total weight, plastic resins, and other specific additives. Because CaCO3 is less expensive than plastic resin, incorporating it into a plastic combination reduces the amount of resin required, allowing plastic enterprises to save money on production costs.
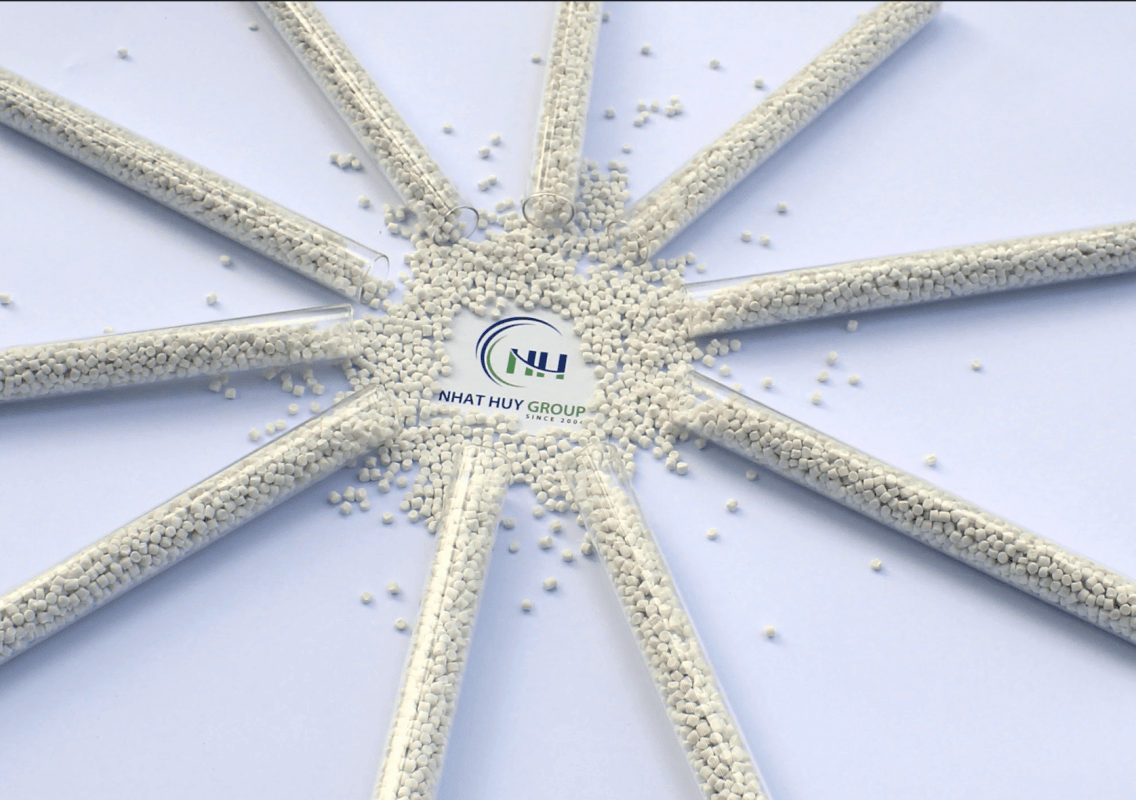
Furthermore, calcium carbonate provides numerous benefits to end-products, such as shortening the product’s cycle (due to CaCO3’s high thermal conductivity) and improving the product’s mechanical properties (impact strength, tear resistance, etc.). As a result, filler masterbatch is widely used in a variety of packaging applications such as shopping bags, wrapping films, roll bags, garbage bags, and so on.